Nitrogen gas (N₂) is one of the most versatile and widely used industrial gases, playing a critical role in industries ranging from food packaging to aerospace. Its inert nature, non-reactivity, and abundance make it indispensable for processes requiring controlled environments, safety, and precision. However, accurately measuring nitrogen gas flow is essential to optimize operations, reduce waste, and ensure safety. This is where nitrogen gas flow meter come into play.
Table des matières
Principales propriétés de l'azote gazeux
Nitrogen is a diatomic gas (N₂) that makes up 78% of Earth’s atmosphere. Its unique characteristics include:
- Inertness: Nitrogen is chemically non-reactive under standard conditions, making it ideal for preventing oxidation, combustion, or contamination.
- Dryness: Pure nitrogen has low moisture content, critical for moisture-sensitive processes.
- Non-flammable and Non-toxic: Safe for use in hazardous environments.
- High Purity Availability: Easily produced at purities exceeding 99.999% for specialized applications.
Applications industrielles de l'azote gazeux
- Alimentation et boissons:
- Modified Atmosphere Packaging (MAP): Nitrogen displaces oxygen to extend shelf life.
- Beverage Dispensing: Prevents oxidation in beer and wine taps.
- Produits pharmaceutiques:
- Blanketing: Protects sensitive drugs from moisture and oxygen during production.
- Purging: Cleans equipment to maintain sterile conditions.
- Electronics Manufacturing:
- Soldering and Wave Soldering: Prevents oxidation of circuit boards.
- Semiconductor Fabrication: Creates inert environments for chip production.
- Chimie et pétrochimie:
- Inerting: Safeguards reactors and storage tanks from explosive reactions.
- Pipeline Purging: Removes hazardous residues during maintenance.
- Aérospatiale:
- Fuel Tank Inerting: Reduces fire risk in aircraft fuel systems.
Qu'est-ce qu'un débitmètre d'azote gazeux ?
A nitrogen gas flow meter is a device designed to measure the volumetric or mass flow rate of nitrogen gas in a system. It provides real-time data to ensure precise control over gas usage, which is vital for process efficiency, cost management, and safety compliance.
Key Functions:
- Monitor nitrogen consumption in real time.
- Detect leaks or irregularities in gas supply.
- Ensure compliance with industry standards (e.g., ISO).
Pourquoi un débitmètre d'azote est-il important ?
- Cost Efficiency:
- Prevents overuse of nitrogen, which can be costly in high-purity applications.
- Reduces waste in processes like MAP packaging, where excess nitrogen is vented.
- Process Optimization:
- Ensures consistent gas flow for critical operations (e.g., semiconductor fabrication).
- Maintains product quality in food and pharmaceutical industries.
- Safety:
- Monitors inerting systems to prevent explosions in chemical plants.
- Alerts operators to leaks in aerospace fuel systems.
- Conformité réglementaire:
- Meets strict standards for emissions, purity, and process control.
Types de débitmètres recommandés pour l'azote gazeux
Selecting the right flow meter depends on factors like flow rate, pressure, accuracy needs, and budget. Below are the top options for nitrogen gas:
1. Débitmètres massiques thermiques
Comment ils fonctionnent:
Measures flow based on heat dissipation from a heated sensor. The cooling effect of the gas correlates with mass flow rate.
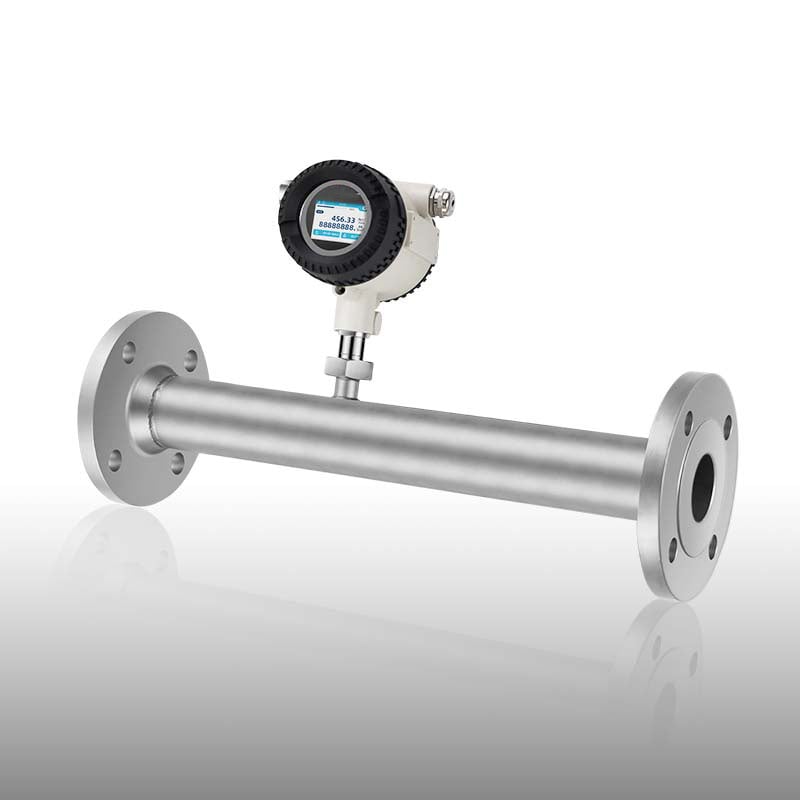
Avantages:
- Direct mass flow measurement (no temperature/pressure compensation).
- High accuracy (±1% of reading).
- Suitable for low to moderate flow rates.
- No moving parts, low maintenance.
Inconvénients:
- Requires calibration for gas composition.
- Less effective in high-humidity environments.
Meilleur pour: Food packaging, pharmaceutical blanketing, and low-flow industrial processes.
2. Débitmètres massiques à effet Coriolis
Comment ils fonctionnent:
Uses the Coriolis effect to measure mass flow via vibrating tubes.
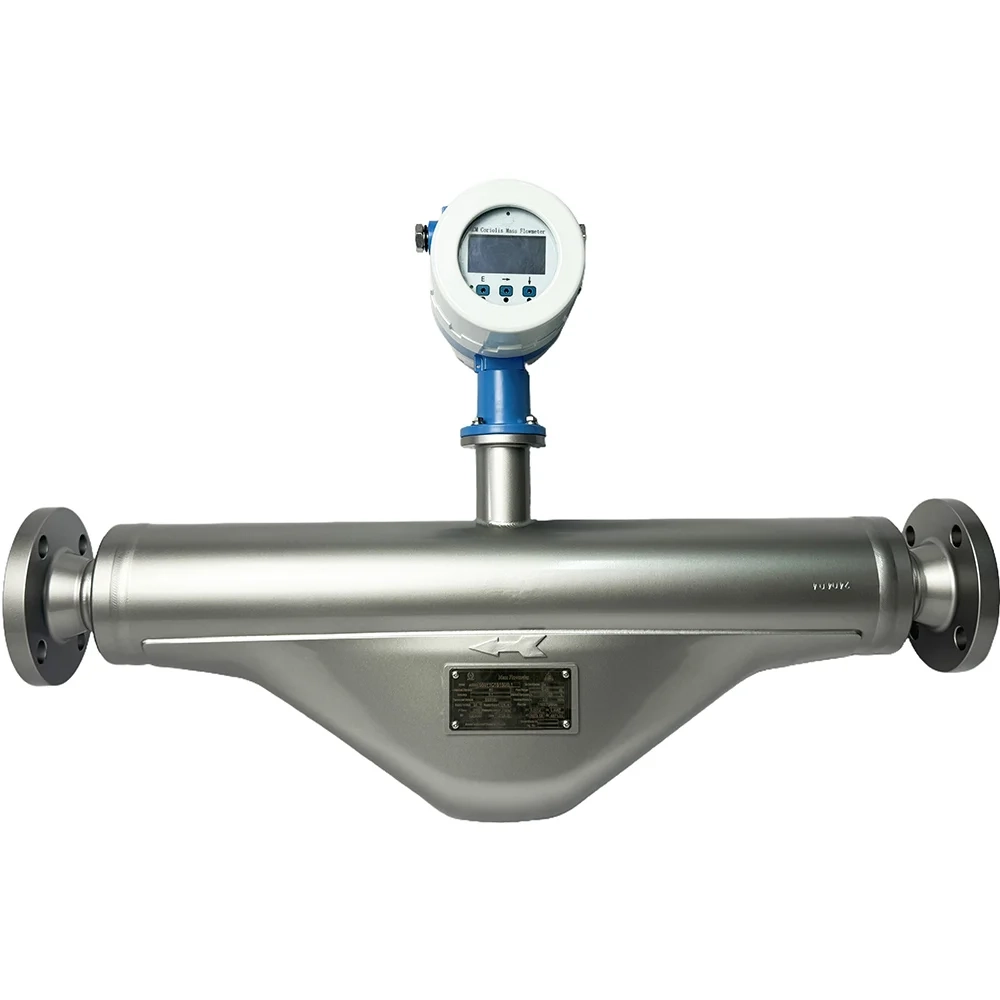
Avantages:
- Extreme accuracy (±0.1%).
- Measures mass flow, density, and temperature simultaneously.
- Immune to pressure or temperature changes.
Inconvénients:
- High upfront cost.
- Bulky design, not ideal for small pipelines.
Meilleur pour: Custody transfer, high-purity semiconductor processes, and aerospace.
3. Differential Pressure (DP) Flow Meters
Comment ils fonctionnent:
Calculates flow based on pressure drop across an orifice plate or venturi tube.
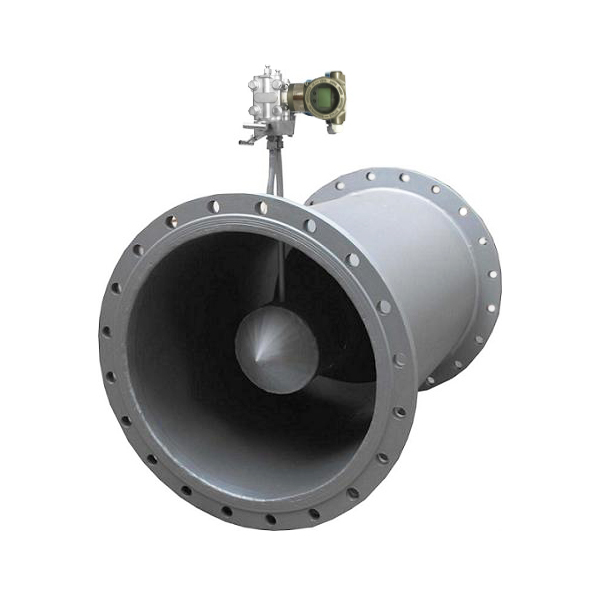
Avantages:
- Low cost and simple design.
- Suitable for high-pressure systems.
Inconvénients:
- Requires temperature/pressure compensation for accuracy.
- Limited turndown ratio.
Meilleur pour: General industrial applications with stable flow rates.
4. Débitmètres à ultrasons
Comment ils fonctionnent:
Uses ultrasonic waves to measure flow velocity (transit-time or Doppler method).
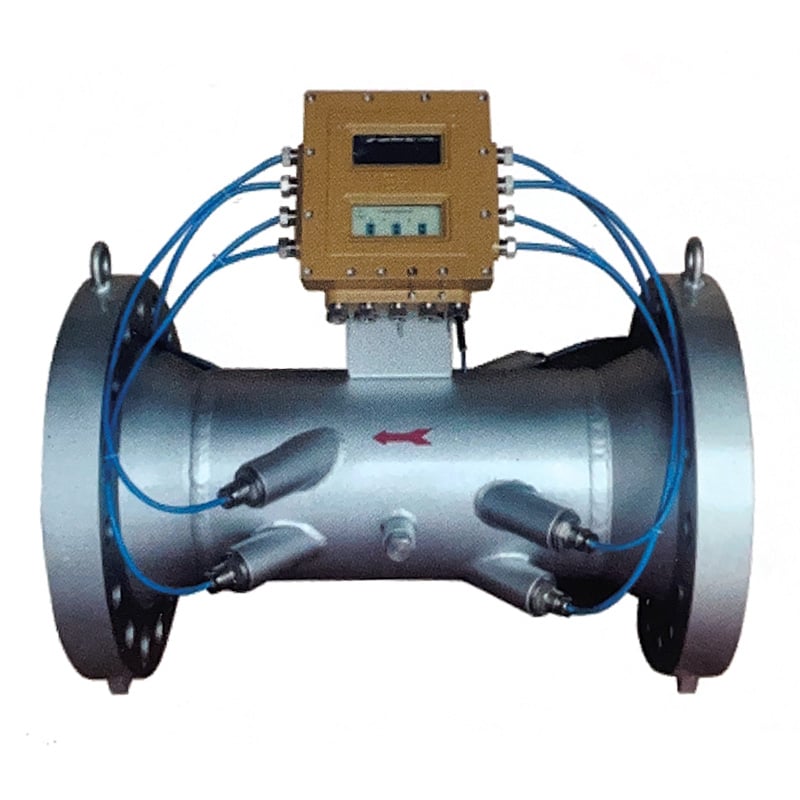
Avantages:
- Non-invasive clamp-on models available.
- Bidirectional flow measurement.
- No pressure drop.
Inconvénients:
- Accuracy affected by gas purity and pipe material.
- Higher cost for high-precision models.
Meilleur pour: Large pipelines in chemical plants or HVAC systems.
How to Choose a Nitrogen Gas Flow Meter
Follow these steps to select the best meter for your needs:
1. Define Your Application Requirements
- Plage de débit: Low (0–50 LPM), medium (50–500 LPM), or high (>500 LPM).
- Pression et température: Ensure the meter can handle system conditions.
- Besoins de précision: ±0.1% for custody transfer vs. ±2% for general monitoring.
2. Evaluate Gas Purity and Composition
- High-purity nitrogen (99.999%) may require specialized materials (e.g., stainless steel).
- Avoid meters sensitive to moisture if using dry nitrogen.
3. Consider Installation Environment
- Inline vs. Clamp-on: Clamp-on ultrasonic meters are ideal for retrofitting.
- Hazardous Areas: Look for ATEX or IECEx certifications for explosive environments.
4. Budget and Total Cost of Ownership
- Balance upfront costs with long-term savings (e.g., low-maintenance Coriolis vs. DP meters).
5. Compliance and Standards
- Ensure the meter meets industry-specific regulations (e.g., FDA for food packaging).
Nitrogen gas flow meters are critical tools for industries relying on precise, safe, and efficient gas handling. Whether you’re flushing potato chip bags with nitrogen or inerting aircraft fuel tanks, choosing the right meter—thermal mass, Coriolis, ultrasonic, or another type—ensures optimal performance and cost savings. By understanding your application’s flow rate, accuracy needs, and environmental conditions, you can select a meter that aligns with both technical and budgetary requirements.