Metlan Instruments places utmost importance on the quality, accuracy, and reliability of our flowmeters. We fully understand that measurement precision is critical across various industries, which is why we implement rigorous quality control measures throughout the entire production cycle to ensure that every flowmeter meets the highest industry standards. The following provides a detailed overview of our electromagnetic flowmeter production process, demonstrating how we achieve precise manufacturing and stringent quality control.
Elektromágneses áramlásmérő gyártási folyamat
At Metlan Instruments, our production process is carefully designed to ensure the stability and accuracy of each flowmeter. From the selection of high-quality raw materials to the final calibration, every step is tightly controlled. Our engineers and technicians follow strict assembly and calibration protocols to ensure each electromagnetic flowmeter performs accurately under various flow conditions, including low flow, high viscosity. We utilize state-of-the-art manufacturing technologies and precision equipment to produce durable components that meet high standards of accuracy and longevity, ensuring the flowmeter’s stability and reliability over its entire lifecycle. Prior to delivery, each unit undergoes a series of precise calibrations, including performance verification under operational conditions, signal integrity tests, and extensive validation under extreme flow conditions to ensure consistent and reliable measurement results.
1. Measuring Tube Processing
- Laser Cutting and Drilling: The measuring tube is precisely cut using high-precision laser cutting equipment, and holes are drilled according to detailed design specifications.
- Flange and Liner Dimension Verification: After confirming the flange standards and liner materials, the hole diameters and overall dimensions are rigorously inspected to ensure that tolerances are within ±1-2mm.
- Quality Inspection: Critical dimensions of the measuring tube (such as hole diameter, length, and wall thickness) are meticulously inspected to ensure compliance with design specifications, forming a reliable foundation for subsequent processes.
2. Electrode Installation
- Electrode Material Selection and Installation: Electrode materials (e.g., 316L stainless steel, tantalum, platinum-iridium alloy) are selected based on the chemical, physical, and mechanical properties of the measured medium to ensure optimal compatibility and durability. Three electrodes, including a grounding ring, are installed strategically to ensure stable contact with the medium and reliable measurement signals while minimizing signal interference and distortion.
- Electrode Wires: Double-layer silver-plated, high-temperature resistant electrode wires are employed to enhance signal transmission. The silver plating improves conductivity, while the high-temperature resistance ensures stable performance under extreme conditions. These wires offer superior anti-interference capabilities, ensuring long-term stability, accuracy, and reliability of signal transmission.
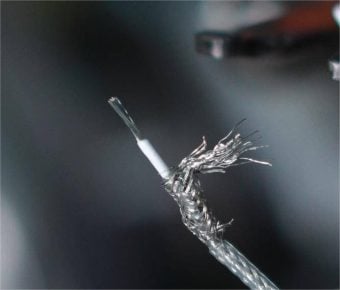
3. Coil and Internal Component Installation
- Pressure Testing: Pressure testing is conducted on the measuring tube prior to assembly to verify its compliance with the required pressure resistance standards.
- Coil Installation: Our products use high-quality pure copper coils, which distinguish our products from the more commonly used aluminum-wound coils in the market that reduce cost but compromise performance. All coils are sourced from reputable manufacturers, ensuring superior performance and reliability.
- Silicon Steel Sheets and Protective Plates Installation: High-permeability silicon steel sheets are installed around the coils to increase the strength of the electromagnetic field. Corrosion-resistant protective plates are also installed to shield internal components from environmental damage.
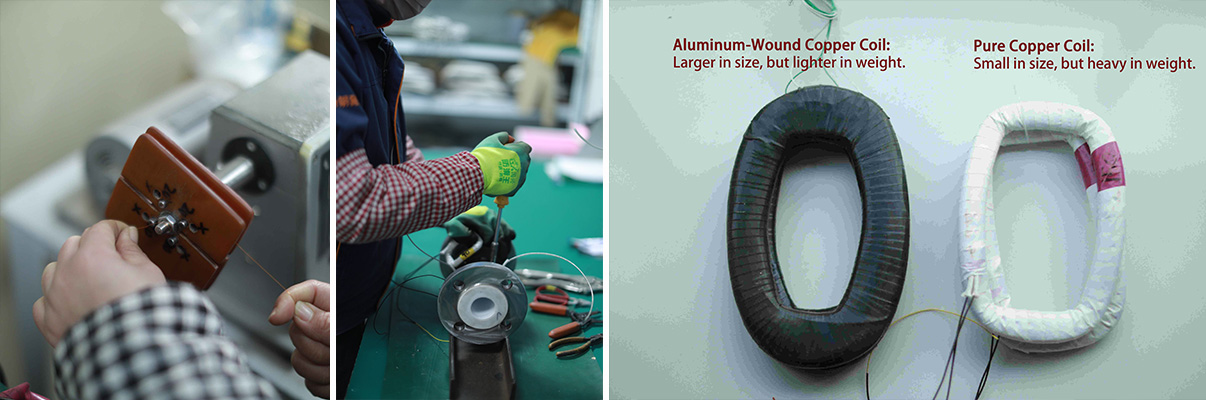
4. Transmitter and Connection Component Installation
- Transmitter Connection Parts: The connection parts for the transmitter are arc-cut to ensure a precise fit with the measuring tube, providing a secure seal while enhancing the aesthetic appearance.
- Circuit Board: The 3-layer circuit board is designed with a complex layout to support accurate measurement and display of slurry content in liquids.
- Transmitter Installation and Aging Test: The intelligent transmitter is installed and undergoes a 24-hour aging test to assess its operational stability and signal output accuracy, ensuring that the instrument performs reliably over time.
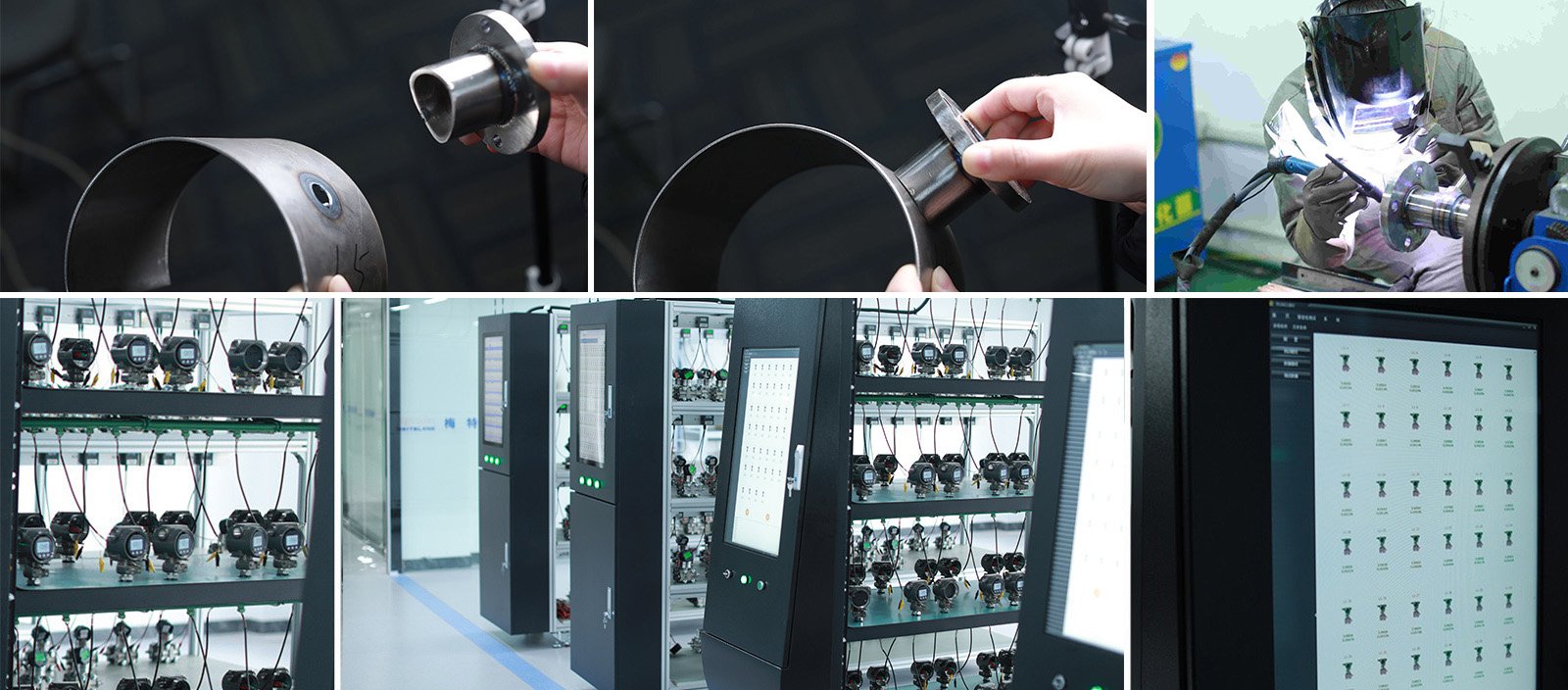
5. Calibration
- Each flowmeter undergoes a thorough calibration process, with its unique serial number recorded alongside a calibration report. The calibration equipment used is certified, ensuring that measurement accuracy meets the design specifications. The flowmeter is calibrated across its full flow range, with verification of indication errors, repeatability, and the adjustment of the instrument coefficient (K) to ensure precise measurement performance.
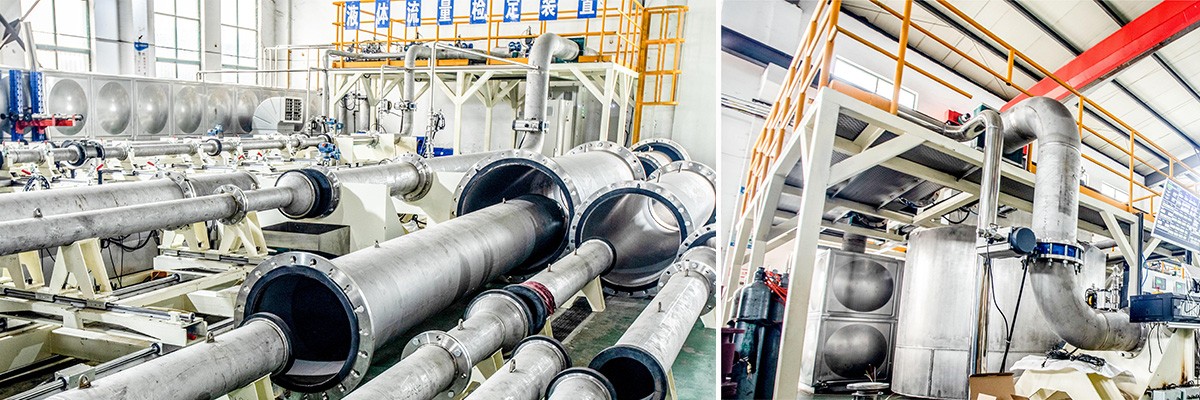
6. Surface Treatment
The instrument body is coated with an anti-corrosion primer and topcoat to enhance durability and corrosion resistance. The surface color can be customized according to customer requirements.
7. Packaging and Shipping
- Pre-Shipment Inspection: All flowmeters undergo a final inspection before packaging and shipment to ensure the product meets technical specifications and customer requirements. A complete product certificate and calibration report are provided.
- Product Documentation: All required product documentation is prepared in accordance with the contract specifications.
- Packaging: Packaging materials are selected based on the size and weight of the flowmeter to ensure safe transportation.
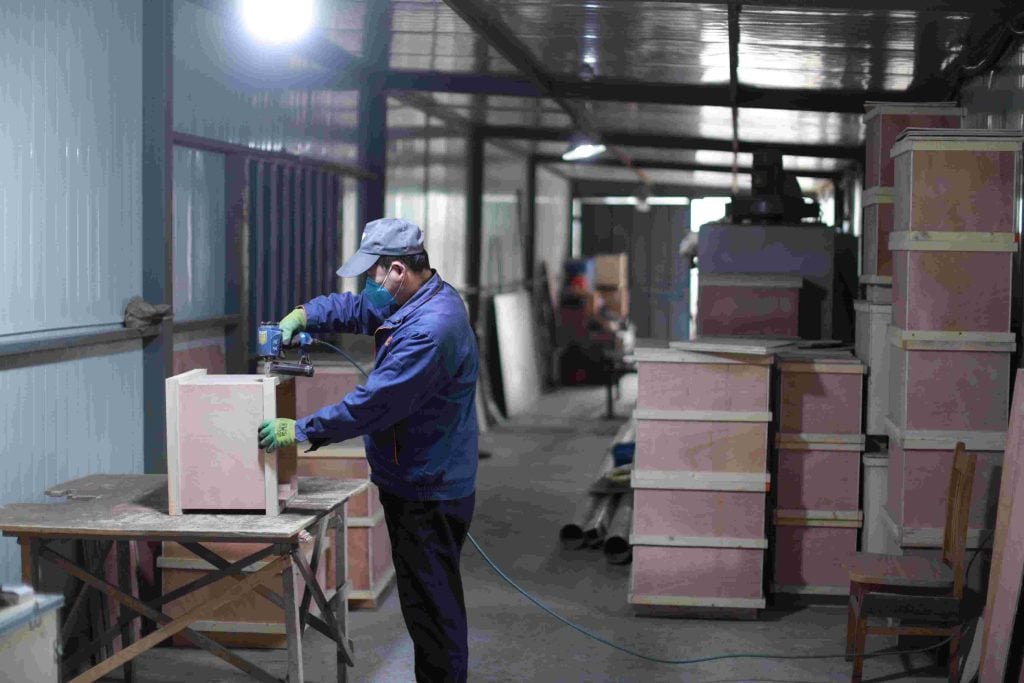
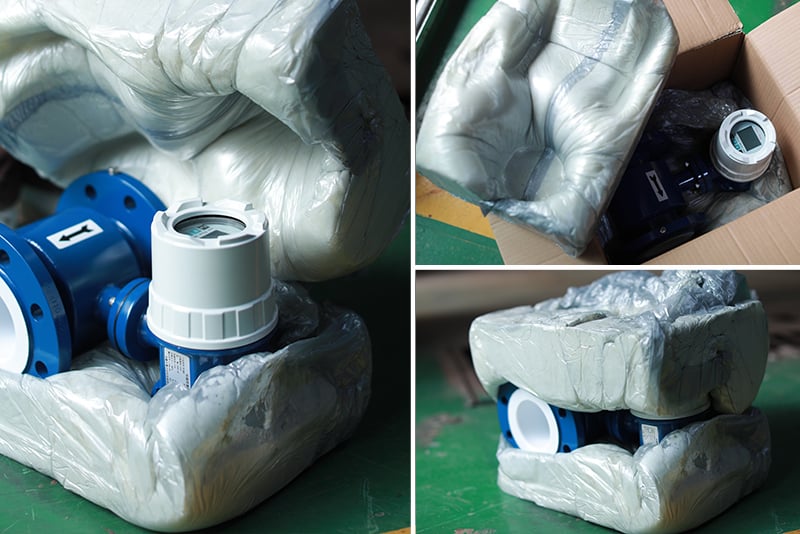