Liquid Flow Meters
A liquid flow meter is a device used to measure the flow rate of liquid in a pipe or conduit. It helps to quantify the amount of liquid passing through a system, ensuring accurate control, monitoring, and optimization of industrial processes. Liquid flow meters are widely used in industries like water treatment, oil and gas, food and beverage, chemical processing, and pharmaceuticals.
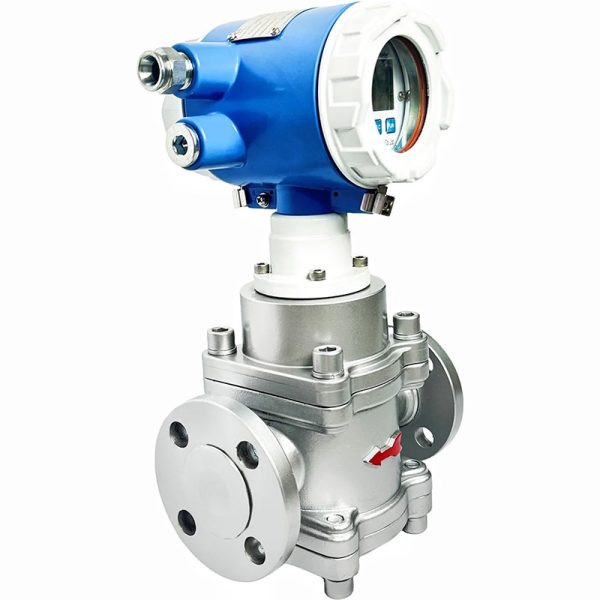
Bi-rotor Positive Displacement Flow Meter (MT-ABR)
- High accuracy up to ±0.1 %
- Strong applicability to viscosity changes.
- Good anti-interference performance and long service life.
Accuracy
Standard: ±0.5 %, Optional: ±0.2 %; ±0.1 %
Measuring Range
0.3 to 1800 m³/h
Medium Temperature Range
Standard: (-20~+100) ℃, Optional: (-20~+250) ℃
Max. Process Pressure
110 bar (1595 psi)
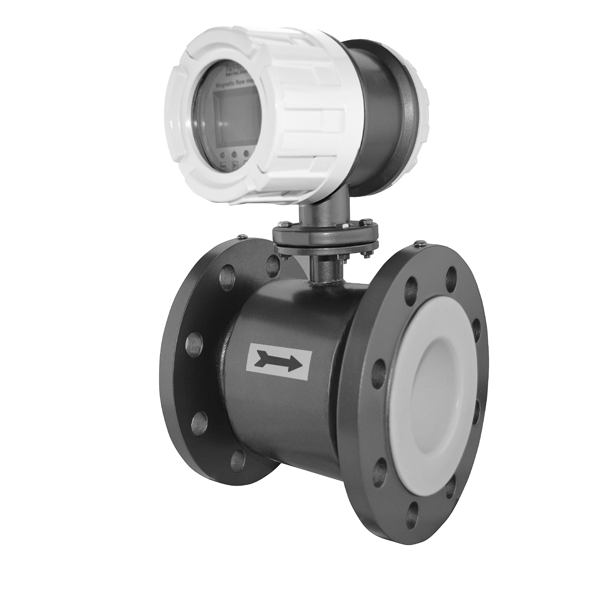
Magnetic Flow Meter for Water and Wastewater (MTF-W)
Accuracy
Standard: ±0.5 %, Optional: ±0.2 %
Measuring Range
1 m³/h to 125000 m³/h
Medium Temperature Range
PU:0 to 140°F (-18 to 60°C)
Neoprene:-13°F to 176°F (-25°C to +80°C)
PTFE:-13 to 300°F (-25 to 150°C)
Max. Process Pressure
100 bar (1450.38 psi)
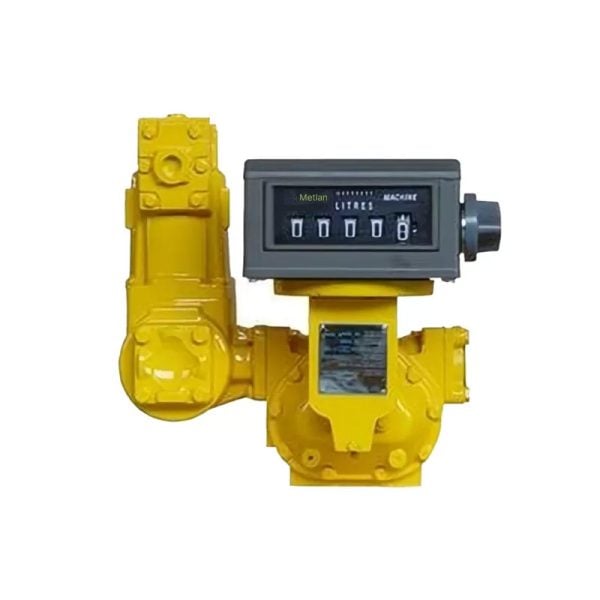
M Series Mechanical Positive Displacement Flow Meter
- ±0.2 % accuracy
- Strong applicability to viscosity changes.
- Good for fuel delivery trucks and tankers.
Accuracy
±0.2 %
Measuring Range
25 to 3000 L/Min
Medium Temperature Range
-20~+250 ℃
Max. Process Pressure
25 bar (350 psi)
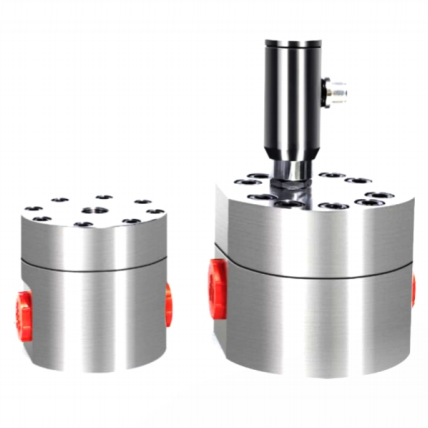
Low Flow Positive Displacement Gear Flow Meter MT-GF
- Designed for low flow liquids from 0.6 L/H.
- 150:1 wide turndown ratio
- Capable of measuring highly corrosive medium.
Accuracy
±0.5 %
Measuring Range
0.6 to 2000 l/h
Medium Temperature Range
Standard: (-40~+80) ℃, Optional: (-40~+200) ℃
Max. Process Pressure
Standard: 100 bar, Optional: 400 bar
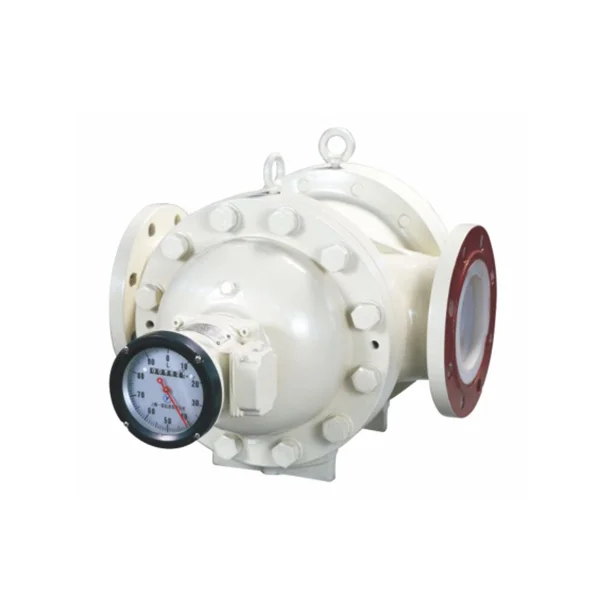
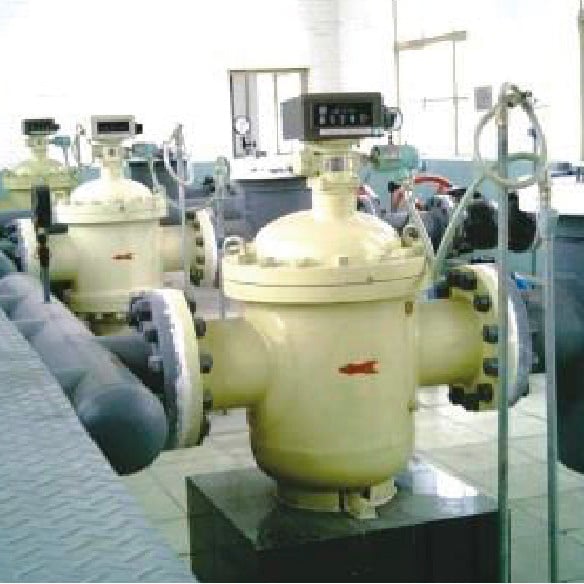
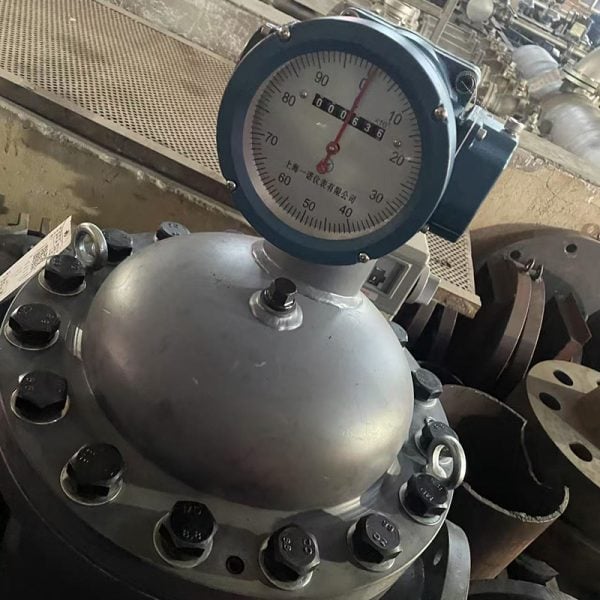
Birotor PD Flowmeter with Mechanical Counter (MT-ABRM)
- High accuracy up to ±0.1 %
- Strong applicability to viscosity changes.
- Good anti-interference performance and long service life.
Accuracy
Standard: ±0.5 %, Optional: ±0.2 %; ±0.1 %
Measuring Range
0.3 to 1800 m³/h
Medium Temperature Range
Standard: (-20~+100) ℃, Optional: (-20~+250) ℃
Max. Process Pressure
110 bar (1595 psi)
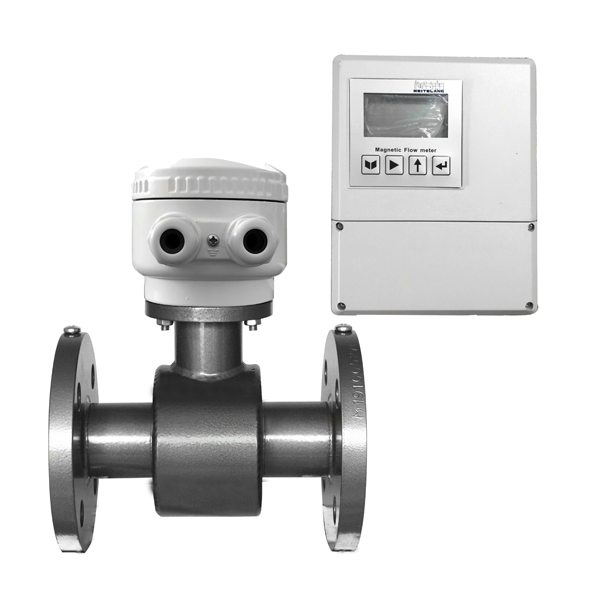
Remote Electromagnetic Flow Meter (MTF-F-200)
Accuracy
Standard: ±0.5 %, Optional: ±0.2 %
Measuring Range
0.3 m³/h to 125000 m³/h
Medium Temperature Range
PU:0 to 140°F (-18 to 60°C)
Neoprene:-13°F to 176°F (-25°C to +80°C)
IR:-13°F to 176°F (-25°C to +80°C)
FEP:-13 to 300°F (-25 to 150°C)
PTFE:-13 to 300°F (-25 to 150°C)
ETFE:-40 to 356°F (-40 to 180°C)
PFA:-40 to 356°F (-40 to 180°C)
Max. Process Pressure
100 bar (1450.38 psi)
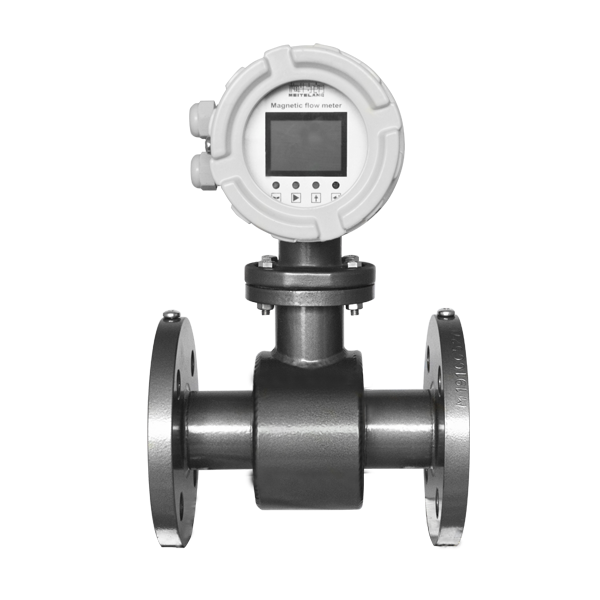
Flanged Electromagnetic Flow Meter (MTF-F-100)
Accuracy
Standard: ±0.5 %, Optional: ±0.2 %
Measuring Range
0.3 m³/h to 125000 m³/h
Medium Temperature Range
PU:0 to 140°F (-18 to 60°C)
Neoprene:-13°F to 176°F (-25°C to +80°C)
IR:-13°F to 176°F (-25°C to +80°C)
FEP:-13 to 300°F (-25 to 150°C)
PTFE:-13 to 300°F (-25 to 150°C)
ETFE:-40 to 356°F (-40 to 180°C)
PFA:-40 to 356°F (-40 to 180°C)
Max. Process Pressure
100 bar (1450.38 psi)
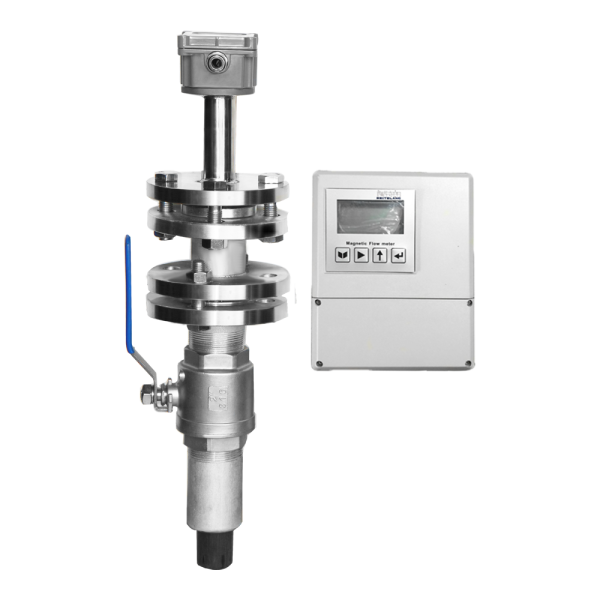
Insertion Magnetic Flow Meters (MTF-I)
Accuracy
Standard: ±1.5 %
Measuring Range
16 m³/h to 125000 m³/h
Medium Temperature Range
< 80°C (176°F)
Max. Process Pressure
25 bar (362.6 psi)
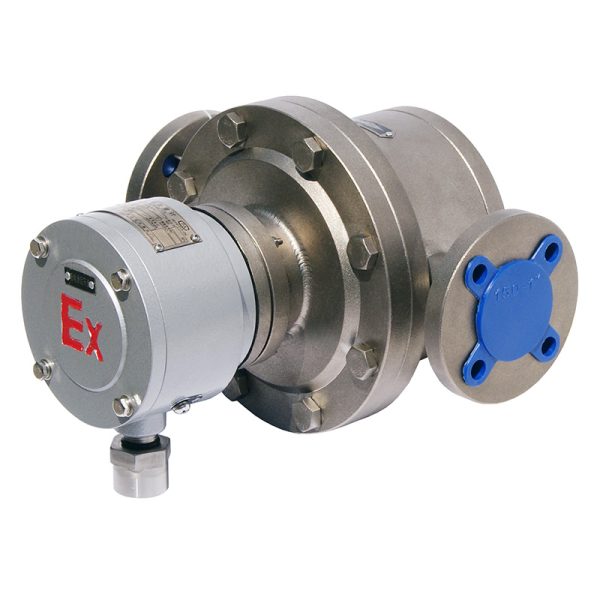
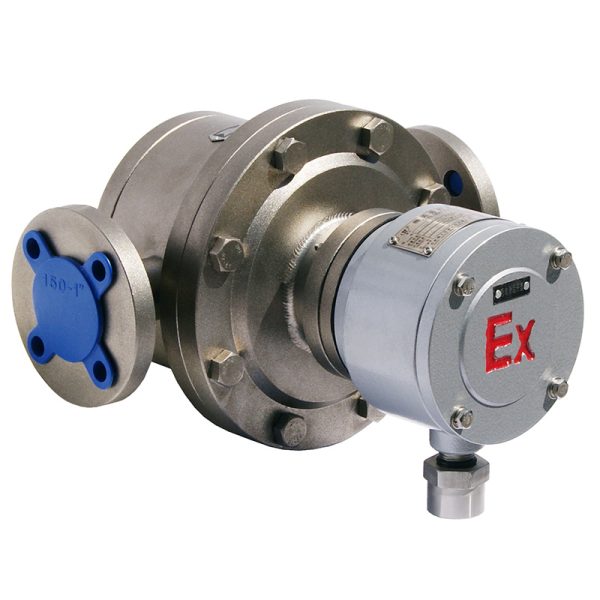
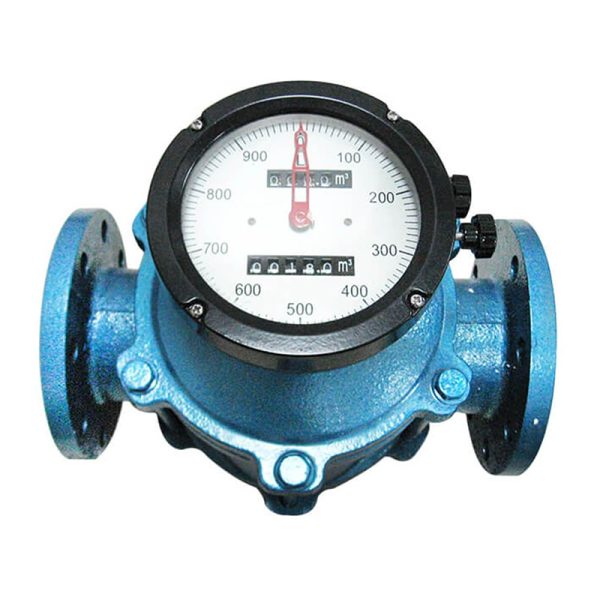
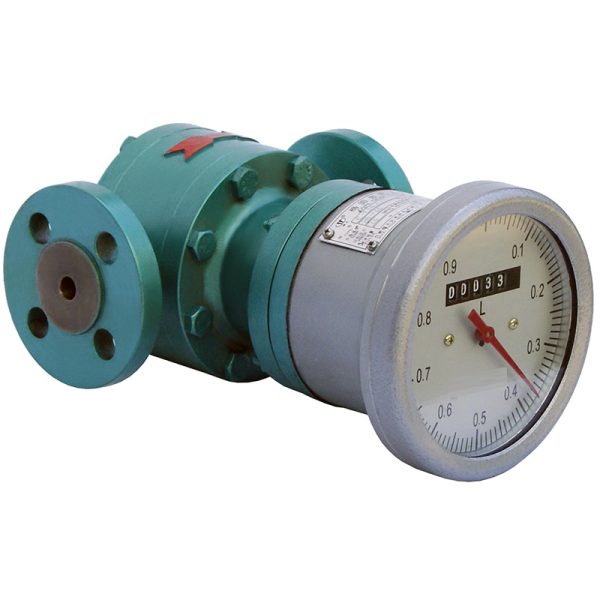
Oval Gear PD Flow Meter MT-LC
- Optimized for higher viscosity liquid measurement.
- Not sensitive to the viscosity change.
- Simple installation without requiring straight pipe runs.
Accuracy
Standard: ±0.5 %, Optional: ±0.2 %
Measuring Range
0.05 to 340 m³/h
Medium Temperature Range
Standard: (-20~+60) ℃ , Optional: (-41~+60) ℃
Max. Process Pressure
63 bar
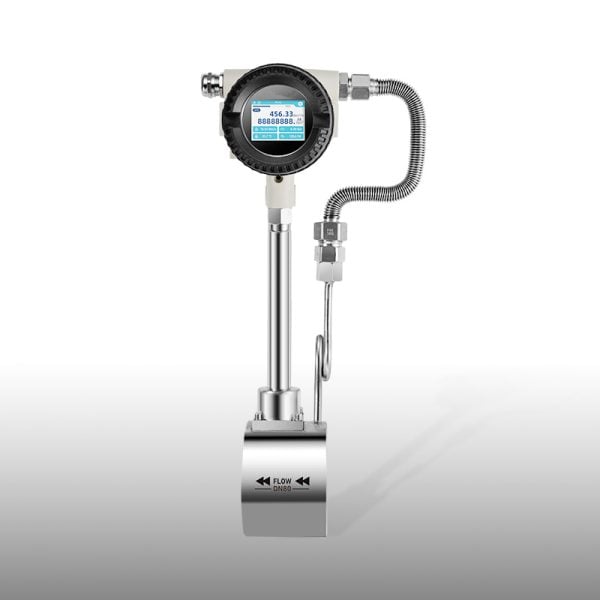
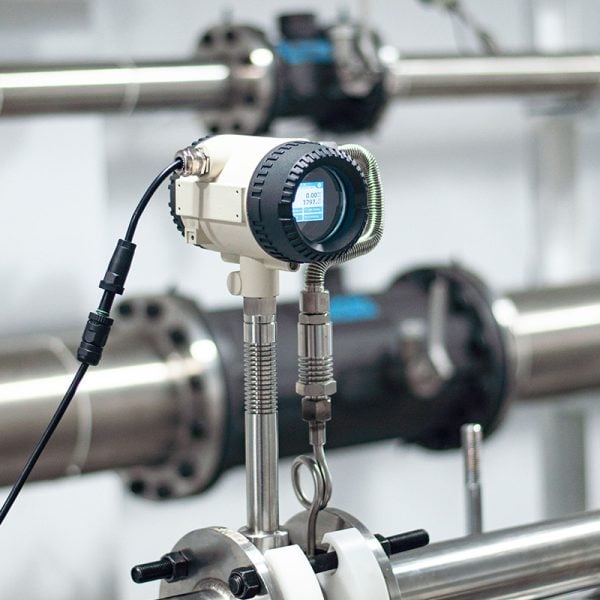
Steam Vortex Flow Meter Anti-vibration (LUGBMT-VS)
Accuracy
Liquid/Gas/Steam: ±1 %
Measuring Range
Steam/Gas: 3.5 to 20347.2 m³/h
Medium Temperature Range
Standard: –40 to +160 °C
High/low temperature (option): –180 to +350 °C
Max. Process Pressure
63 bar (913.74 psi)
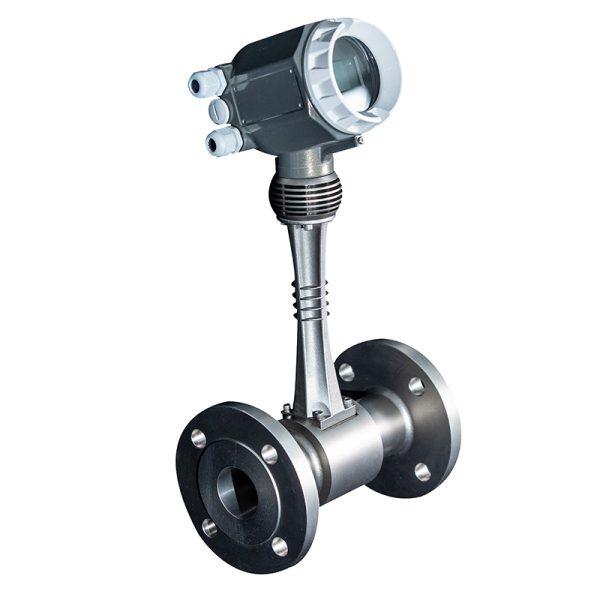
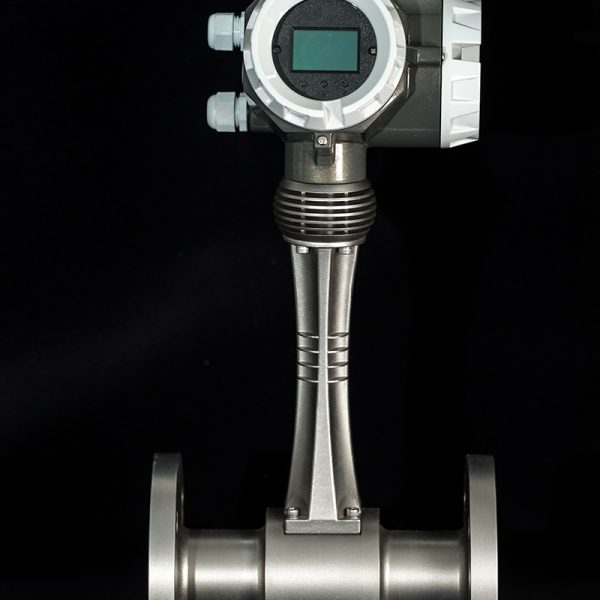
Vortex Flow Meters (LUGBMT-100)
Accuracy
Liquid/Gas/Steam: ±1 %
Measuring Range
Liquid: 0.8 to 3500 m³/h
Steam, gas: 5 to 18000 m³/h
Medium Temperature Range
Standard: –40 to +260 °C (–40 to +480 °F)
High/low temperature (option): –200 to +400 °C (–328 to +750 °F)
Max. Process Pressure
100 bar (1450.38 psi)
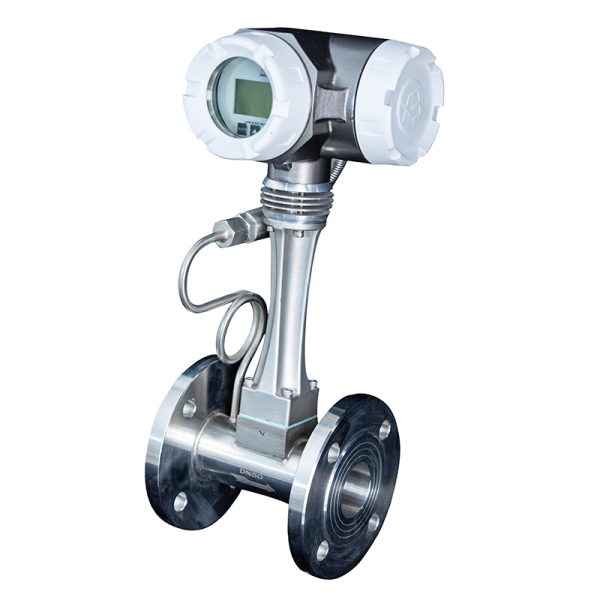
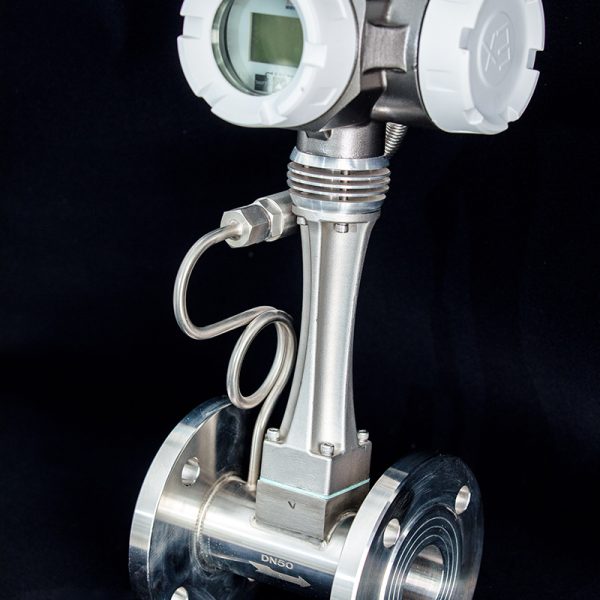
Vortex Flow Meters with Temperature and Pressure Compensation (LUGBMT-C)
Accuracy
Liquid/Gas/Steam: ±1 %
Measuring Range
Liquid: 0.8 to 3500 m³/h
Steam, gas: 5 to 18000 m³/h
Medium Temperature Range
Standard: –40 to +260 °C (–40 to +480 °F)
High/low temperature (option): –200 to +350 °C (–328 to +660 °F)
Max. Process Pressure
100 bar (1450.38 psi)
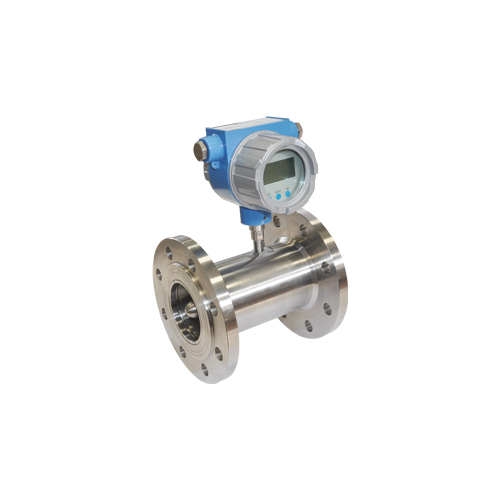
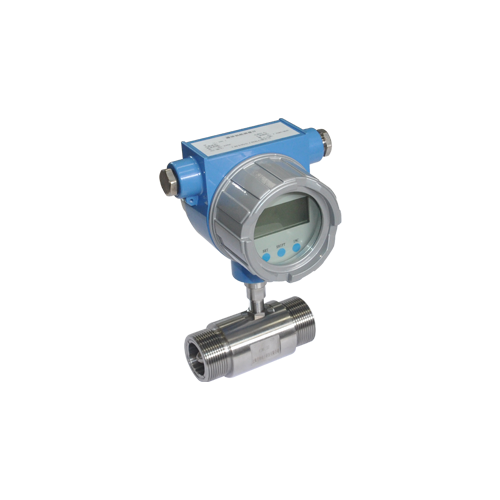
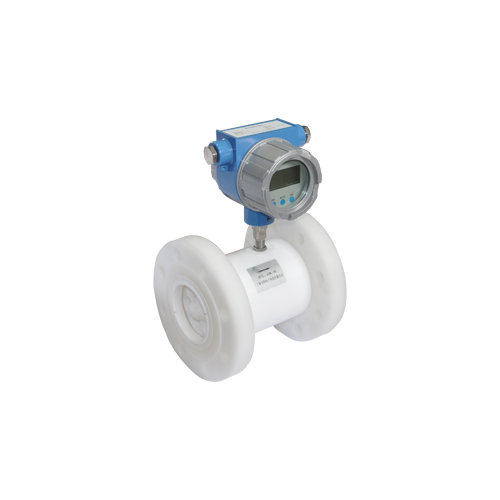
High Accuracy Liquid Turbine Flow Meter (LWGYMT-AJWL)
Accuracy
±0.2 %; ±0.5 %
Measuring Range
0.004 to 1800 m³/h
Medium Temperature Range
standard: -196 TO 180 °C (−320.8 to +356 °F)
Max. Process Pressure
350 bar
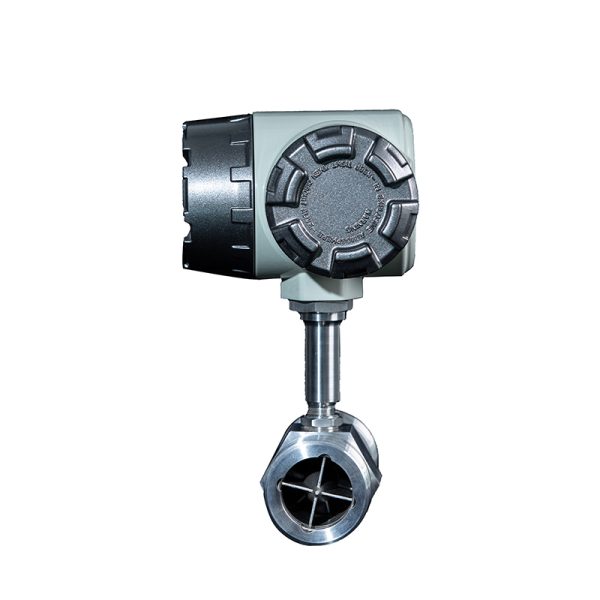
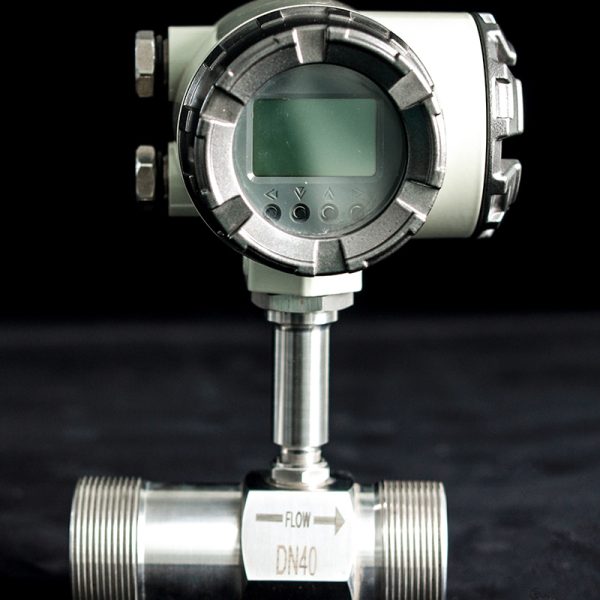
Liquid Turbine Flow Meter (LWGYMT-100)
Accuracy
Standard: ±1 %, Optional: ±0.5 %
Measuring Range
0.04 to 800 m³/h
Medium Temperature Range
standard: -20 TO 120 °C (–4 to +248 °F)
Max. Process Pressure
250 bar (3625.95 psi)
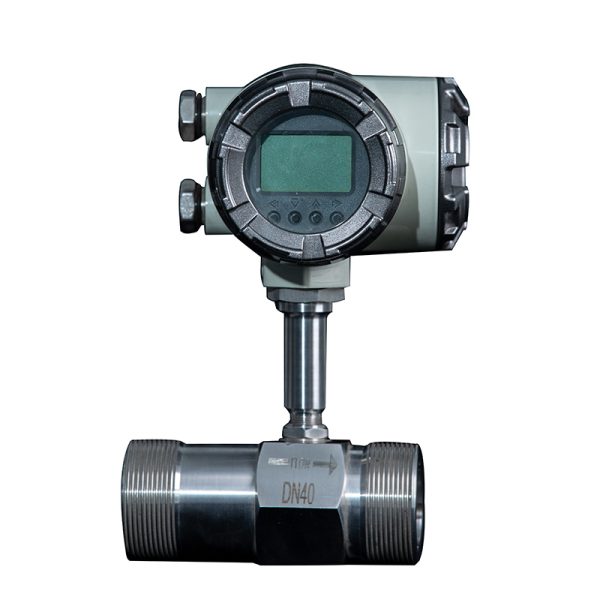
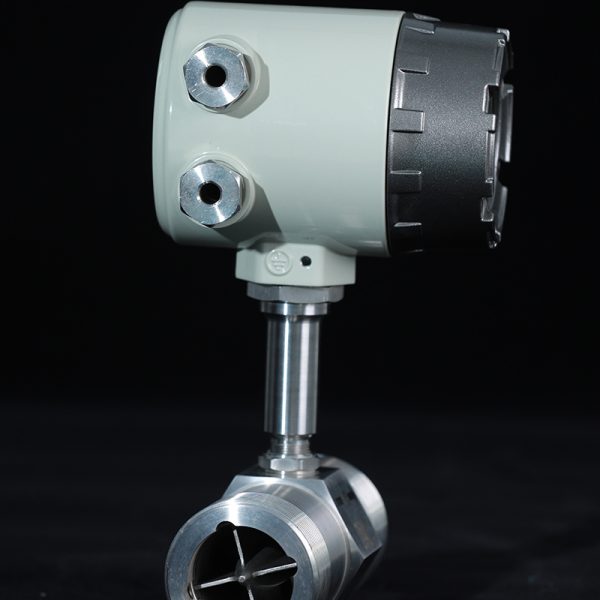
Low Flow Liquid Turbine Flow Meter (LWGYMT-F)
Accuracy
Standard: ±1 %, Optional: ±0.5 %
Measuring Range
0.04 to 200 m³/h
Medium Temperature Range
standard: -20 TO 120 °C (–4 to +248 °F)
Max. Process Pressure
160 bar (2320.6 psi)
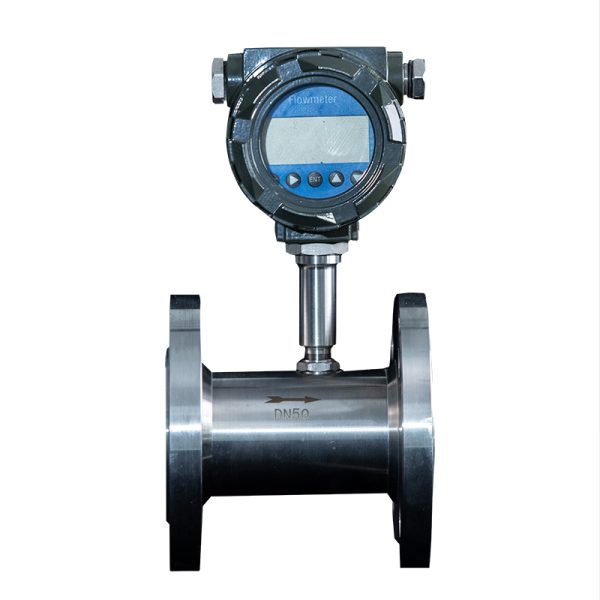
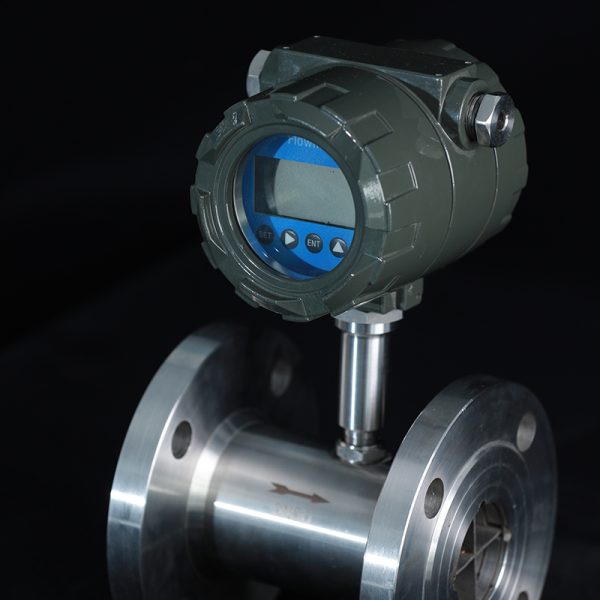
High Pressure Liquid Turbine Flow Meter (LWGYMT-P)
Accuracy
Standard: ±1 %, Optional: ±0.5 %
Measuring Range
0.4 to 800 m³/h
Medium Temperature Range
standard: -20 TO 120 °C (–4 to +248 °F)
Max. Process Pressure
250 bar (3625.95 psi)
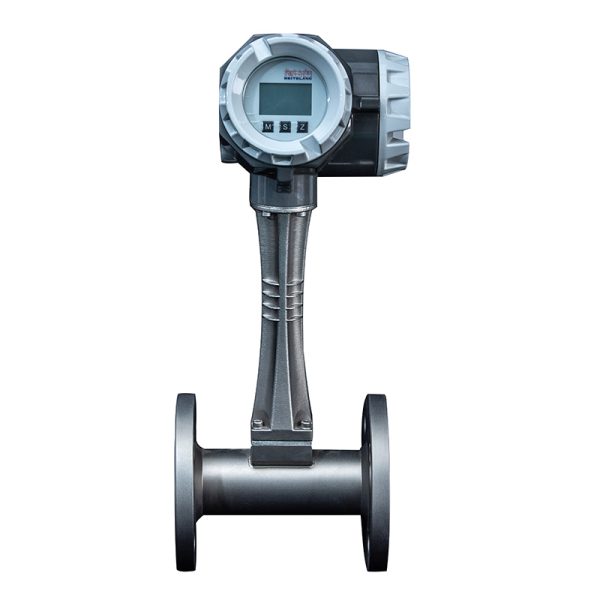
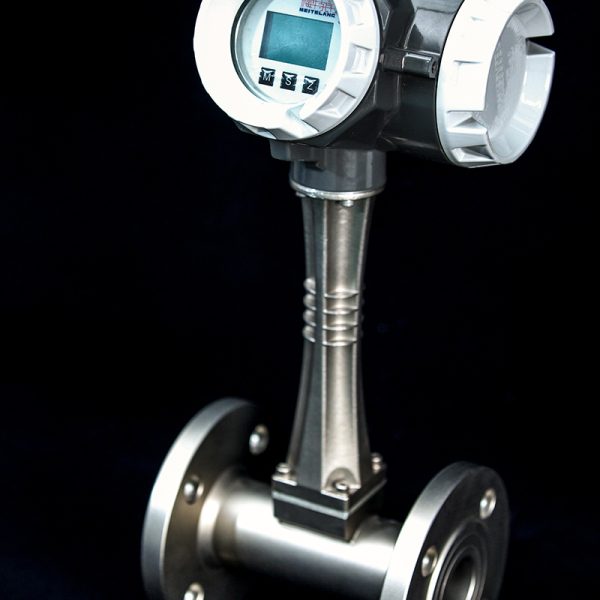
Vortex Flow Meter for High Pressure (LUGBMT-P)
Accuracy
Liquid/Gas/Steam: ±1 %
Measuring Range
Liquid: 0.8 to 3500 m³/h
Steam, gas: 5 to 18000 m³/h
Medium Temperature Range
Standard: –40 to +260 °C (–40 to +480 °F)
High/low temperature (option): –200 to +350 °C (–328 to +660 °F)
Max. Process Pressure
250 bar (3625.95 psi)
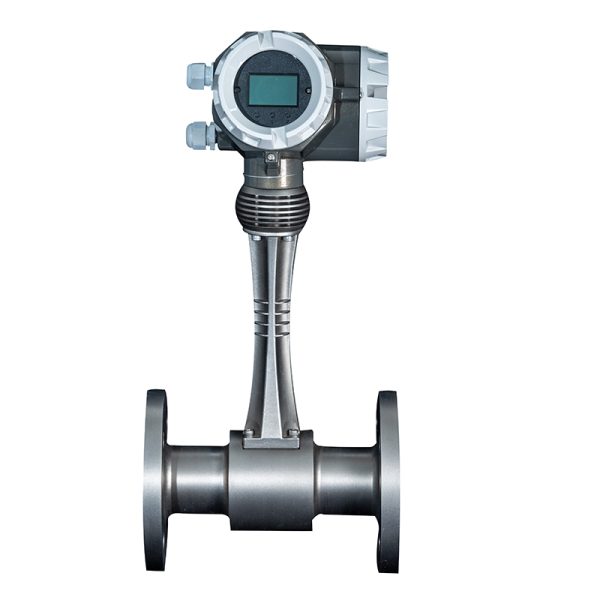
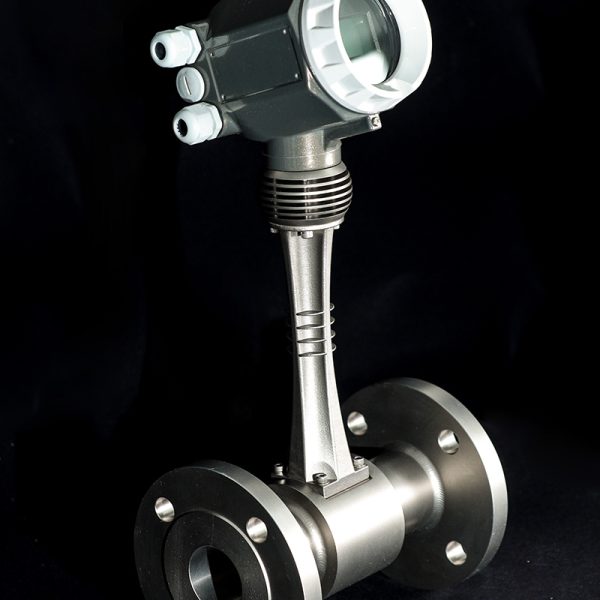
Vortex Flow Meter for High Temperature Medium (LUGBMT-H)
Accuracy
Liquid/Gas/Steam: ±1 %
Measuring Range
Liquid: 0.8 to 3500 m³/h
Steam, gas: 5 to 18000 m³/h
Medium Temperature Range
–200 to +400 °C (–328 to +750 °F)
Max Process Pressure
100 bar (1450.38 psi)
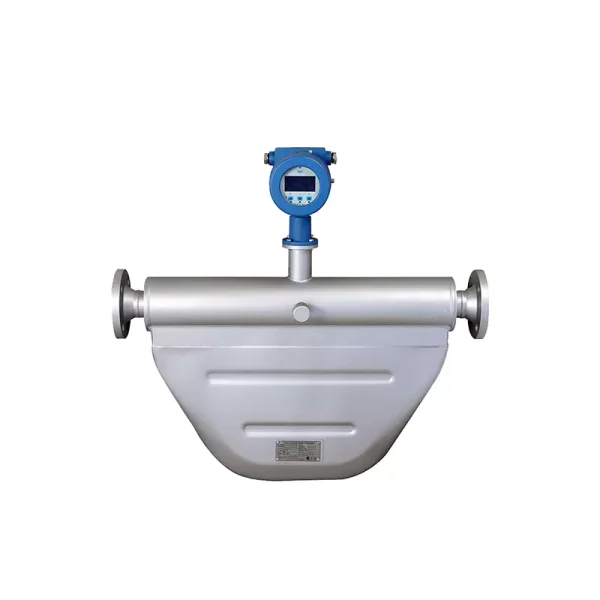
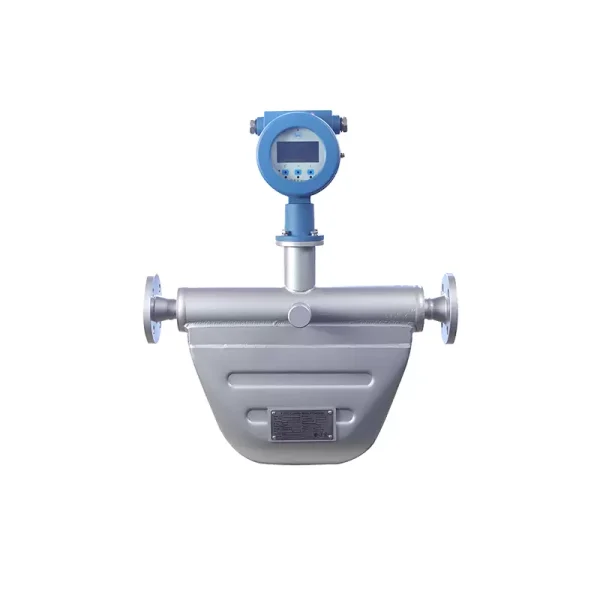
Coriolis Mass Flow Meter W Shape (MTD-ACMW)
Accuracy
±0.1 %; ±0.15 %; ±0.2 %; ±0.5 %
Measuring Range
8-1500000 kg/h (17 – 3306930 lb/h)
Medium Temperature Range
Integrate Type: (-50~+125)℃
Split Type: (-200~+350)℃
Max. Process Pressure
250 bar (3626 psi)
Measuring tube
Austenitic stainless steel (316/316L), and others on request
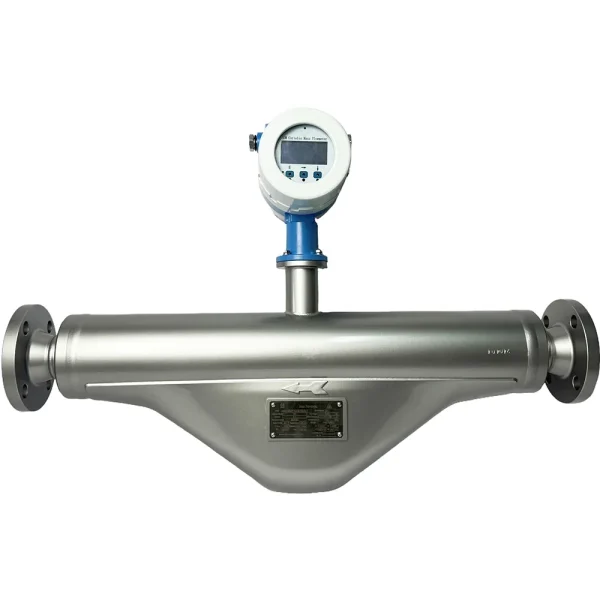
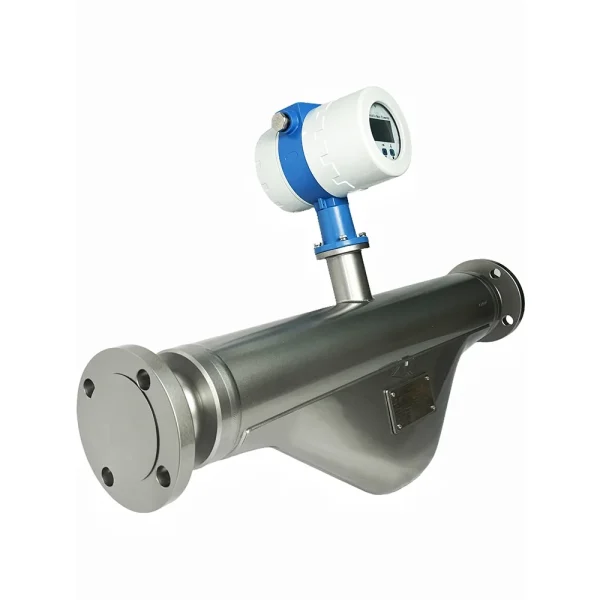
Coriolis Mass Flow Meter C Shape (MTD-ACMC)
Accuracy
±0.1 %; ±0.15 %; ±0.2 %; ±0.5 %
Measuring Range
500-200000 kg/h (1100-440900 lb/h)
Medium Temperature Range
Integrate Type: (-50~+125)℃
Split Type: (-200~+350)℃
Max. Process Pressure
250 bar (3626 psi)
Measuring tube
Austenitic stainless steel (316/316L), and others on request
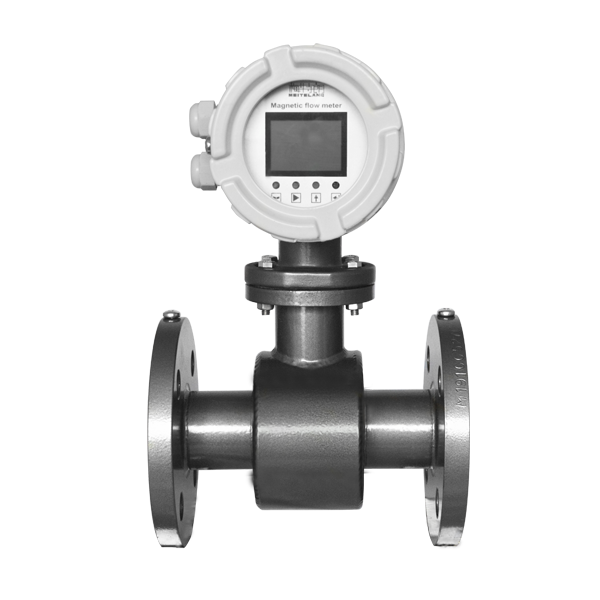
Electromagnetic Flowmeter for Low Conductivity Liquids (MTF-C)
Accuracy
Standard: ±1 %, Optional: ±0.5 %
Measuring Range
1 m³/h to 125000 m³/h
Medium Temperature Range
PU:0 to 140°F (-18 to 60°C)
Neoprene:-13°F to 176°F (-25°C to +80°C)
IR:-13°F to 176°F (-25°C to +80°C)
FEP:-13 to 300°F (-25 to 150°C)
PTFE:-13 to 300°F (-25 to 150°C)
ETFE:-40 to 356°F (-40 to 180°C)
PFA:-40 to 356°F (-40 to 180°C)
Max. Process Pressure
40 bar (580.15 psi)
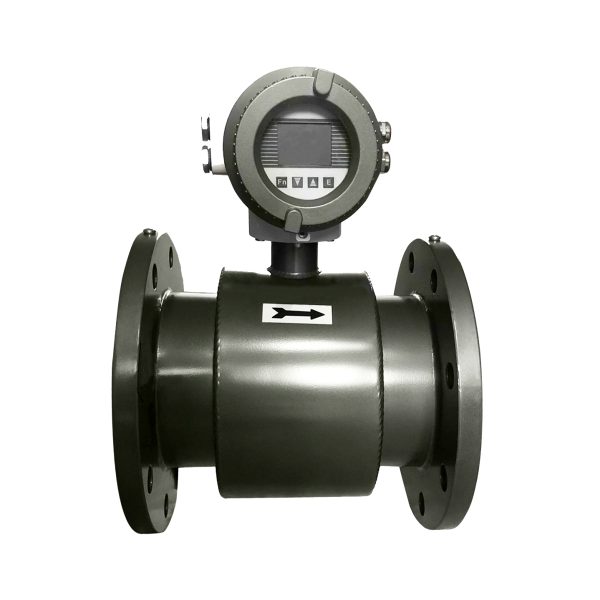
Electromagnetic Flow Meter for Slurry (MTF-S)
Accuracy
Standard: ±0.5 %, Optional: ±0.2 %
Measuring Range
9 m³/h to 11500 m³/h
Medium Temperature Range
PU:0 to 140°F (-18 to 60°C)
FEP:-13 to 300°F (-25 to 150°C)
ETFE:-40 to 356°F (-40 to 180°C)
PFA:-40 to 356°F (-40 to 180°C)
Max. Process Pressure
63 bar (913.74 psi)
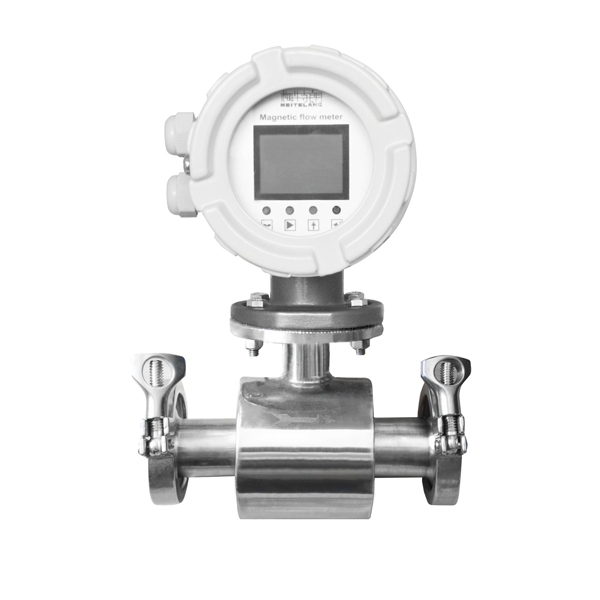
Sanitary Magnetic Flow Meters (MTF-A)
Accuracy
Standard: ±0.5 %, Optional: ±0.2 %
Measuring Range
0.3 m³/h to 300 m³/h
Medium Temperature Range
FEP:-13 to 300°F (-25 to 150°C)
PTFE:-13 to 300°F (-25 to 150°C)
PFA:-40 to 356°F (-40 to 180°C)
Max. Process Pressure
40 bar (580.15 psi)
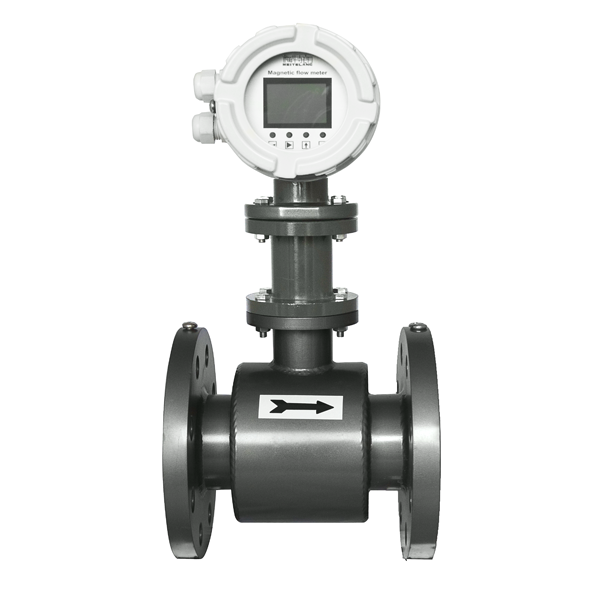
Magnetic Flow Meter for High Temperature Medium (MTF-H)
Accuracy
Standard: ±0.5 %, Optional: ±0.2 %
Measuring Range
0.3 m³/h to 5000 m³/h
Medium Temperature Range
FEP:-13 to 300°F (-25 to 150°C)
PTFE:-13 to 300°F (-25 to 150°C)
ETFE:-40 to 356°F (-40 to 180°C)
PFA:-40 to 356°F (-40 to 180°C)
Max. Process Pressure
40 bar (580.15 psi)
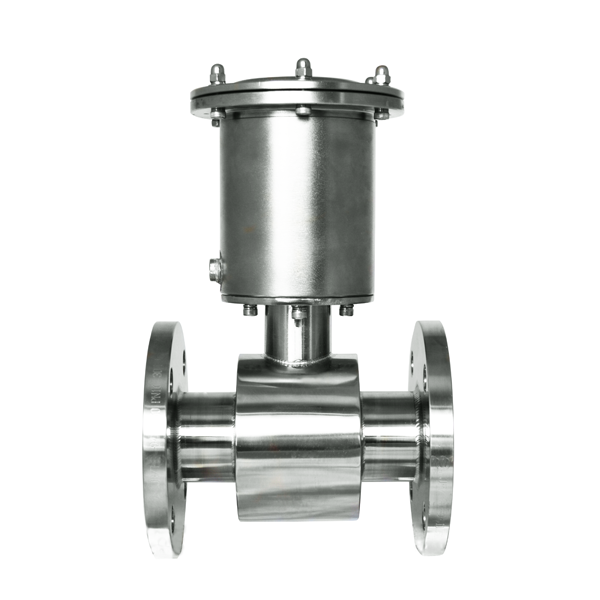
Battery Powered Magnetic Flowmeter (MTF-B)
Accuracy
Standard: ±0.5 %
Measuring Range
0.15 m³/h to 9000 m³/h
Medium Temperature Range
PU:0 to 140°F (-18 to 60°C)
Neoprene:-13°F to 176°F (-25°C to +80°C)
PTFE:-13 to 300°F (-25 to 150°C)
Max. Process Pressure
100 bar (1450.38 psi)
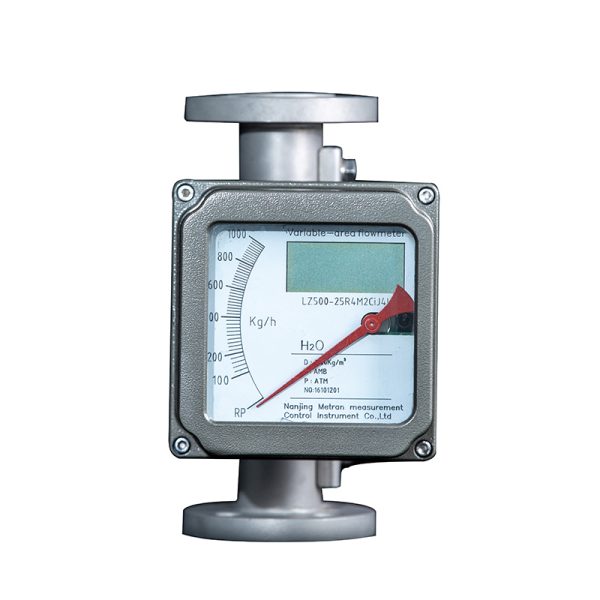
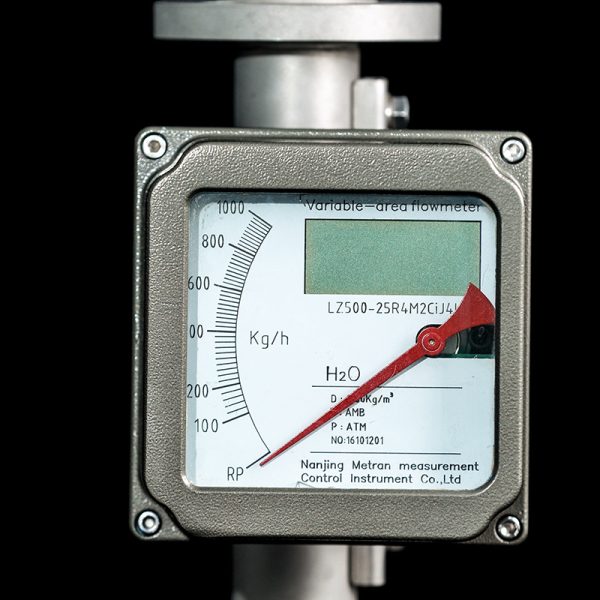
Rotameter Metal Variable Area Flow Meters (MTLZ-M)
Accuracy
Standard: ±2.5 %, Optional: ±1.5 %
Measuring Range
Liquid:1.0~150000l/h
Gas:0.05~3000m³/h
Medium Temperature Range
standard: -80 TO 350 °C (–112 to +662 °F)
Max. Process Pressure
DN15-50:200 bar (2900.76 psi)
DN80-100: 100 bar (1450.38 psi)
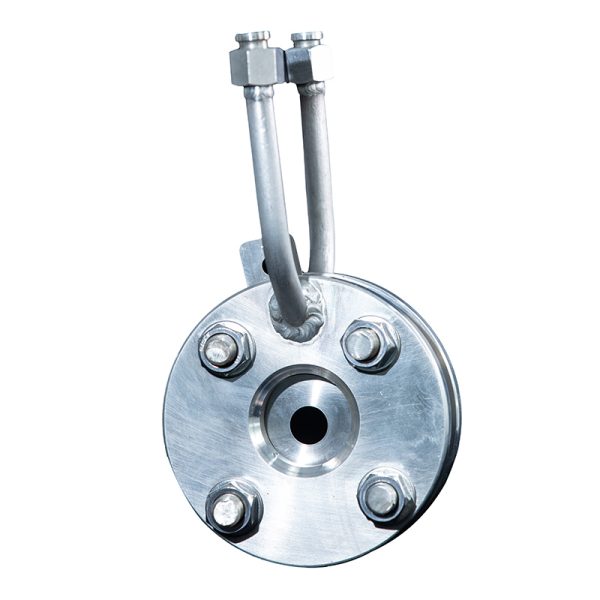
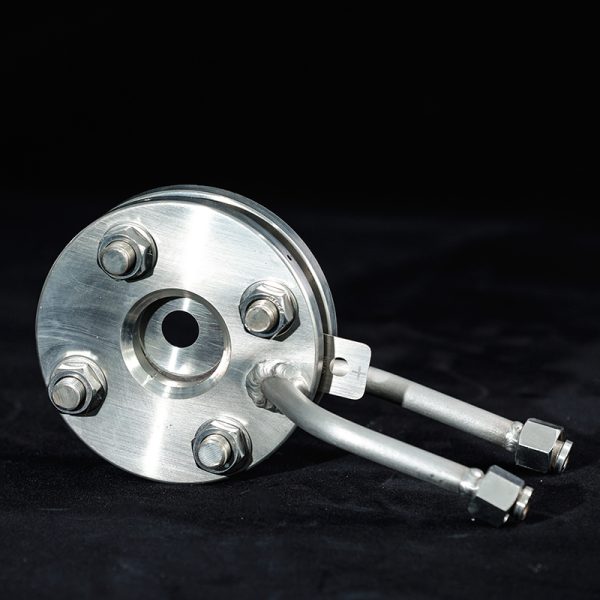
Orifice Plate Flowmeter (MTKB-O)
Accuracy
±0.075%
Medium Temperature Range
standard: -40 TO 850 °C (–40 to +1562 °F)
Max. Process Pressure
400 bar (5801.52 psi)
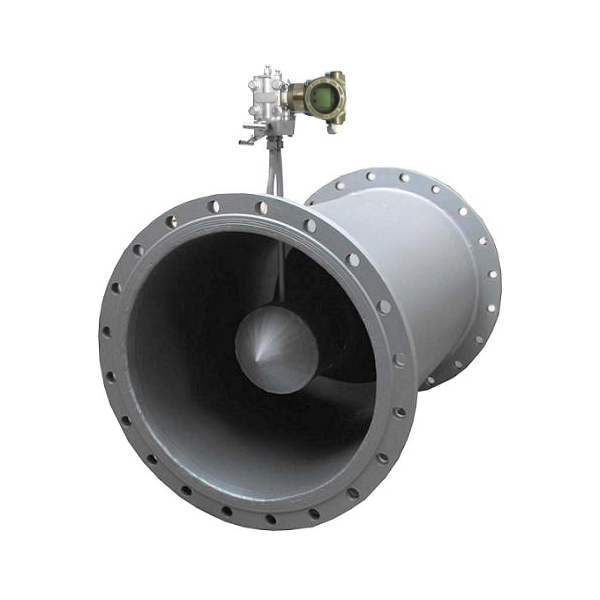
V Cone Different Pressure Flowmeter (MTKB-V)
Accuracy
±0.5%
Medium Temperature Range
standard: -40 TO 850 °C (–40 to +1562 °F)
Max. Process Pressure
420 bar (6091.6 psi)
Types of Liquids
-
Water
One of the most common liquids measured, water is generally easy to handle but can vary in temperature, pressure, and purity. It can be clean (potable water), contaminated (wastewater), or treated for specific uses. -
Viscous Liquids
Oils, syrups, and other thick liquids fall into this category. These liquids often flow more slowly and may require specialized meters to account for their high viscosity. -
Chemicals
Chemicals can vary widely in terms of viscosity, corrosiveness, and reactivity. Choosing the right meter for chemicals often requires selecting materials that can withstand the chemical’s corrosive properties. -
Slurries
A slurry is a mixture of liquids and solids, such as mud, concrete, or pulp. Slurries can be highly abrasive and may clog or damage certain flow meters. -
Hydrocarbons
Crude oil, refined petroleum products, and natural gas liquids are typically measured in the oil and gas industry. These liquids can have varying viscosities, densities, and flow rates. -
Food and Beverage Liquids
In the food and beverage industry, liquids include products like milk, beer, juices, syrups, and cooking oils. These liquids require flow meters that meet hygienic standards, are easy to clean, and can handle a range of viscosities without contaminating the product.
Factors to Consider When Choosing Liquid Flow Meters
Viscosity
Viscosity refers to the thickness of a liquid and its resistance to flow. High-viscosity liquids, such as oils and syrups, flow more slowly and require flow meters that can handle thick, slow-moving fluids. Positive displacement or Coriolis meters are typically better suited for high-viscosity liquids.Flow Rate
The required flow rate range is a critical factor in choosing the right meter. Some flow meters, like turbine meters, are ideal for high-flow conditions, while others, such as thermal mass meters, work better at lower flow rates. Ensuring the meter can accurately measure within your desired flow range is crucial.Conductivity
Some flow meters, like electromagnetic (mag) meters, only work with conductive liquids (i.e., liquids that can carry an electrical charge). For non-conductive liquids like hydrocarbons, a different type of flow meter, such as ultrasonic or positive displacement meters, is required.Corrosiveness
Some flow meters, like electromagnetic (mag) meters, only work with conductive liquids (i.e., liquids that can carry an electrical charge). For non-conductive liquids like hydrocarbons, a different type of flow meter, such as ultrasonic or positive displacement meters, is required.Particulate Content
Some liquids contain solid particles or sediments (e.g., slurries or wastewater). Flow meters designed for clean liquids may not function properly in these conditions, leading to clogging or inaccurate measurements. In such cases, mag meters, vortex meters, or ultrasonic meters are more appropriate, as they can handle particulate-laden fluids.Temperature & Pressure
Extreme temperature or pressure conditions can affect a flow meter’s performance. Some flow meters, like Coriolis or mag meters, are more suited to high-temperature and high-pressure environments, while others may degrade or lose accuracy.Accuracy and Precision Requirements
The required accuracy depends on the application. For example, applications involving billing, custody transfer, or regulatory compliance will require highly accurate meters, such as Coriolis or positive displacement meters. Other applications, like general monitoring, can tolerate lower accuracy levels.Hygienic Standards for Food and Beverage Applications
In food and beverage industries, flow meters must meet strict sanitary standards to prevent contamination. Flow meters should be made of food-grade materials such as stainless steel and be designed for easy cleaning (CIP/SIP). Non-intrusive or contactless meters are often preferred to avoid contamination and simplify cleaning processes.
Recommended Flow Meters for Different Types of Liquids
Electromagnetic (Magnetic) Flow Meters
Best for: Water, wastewater, slurries, and conductive liquids.How it Works: Electromagnetic flow meters (mag meters) work by generating a magnetic field and measuring the voltage produced as a conductive liquid passes through it. The voltage is proportional to the flow rate.Pros:- Highly accurate for conductive liquids.
- No moving parts, resulting in low maintenance.
- Suitable for dirty or contaminated liquids, including slurries and wastewater.
- Available in hygienic designs, meeting stringent sanitary requirements for food and beverage applications.
- Only works with conductive liquids, not suitable for hydrocarbons or non-conductive chemicals.
Why Recommended: Mag meters are highly reliable and versatile, making them ideal for measuring water, wastewater, and slurries. Their durability and ability to handle dirty or particulate-laden liquids without clogging make them well-suited for industrial and municipal water systems.Vortex Flow Meters
Best for: Clean, low-viscosity liquids, steam, and some chemicals.How it Works: Vortex meters work by placing a bluff body in the flow stream. As the liquid flows around the body, vortices are generated, and the frequency of these vortices is proportional to the flow rate.Pros:- No moving parts, resulting in low maintenance.
- Suitable for high-temperature and high-pressure applications.
- Can measure a wide range of fluids, including liquids, gases, and steam.
- Less accurate for low flow rates and viscous liquids.
- Can be affected by turbulence and vibration, leading to inaccurate measurements.
- Not ideal for high-viscosity liquids or slurries, as they can disrupt vortex formation.
Why Recommended: Vortex flow meters are particularly useful for clean, low-viscosity liquids and environments with high temperatures or pressures. They are commonly used in the food and beverage industry for applications where clean steam or low-viscosity liquids are used in the production process. Their hygienic design options make them suitable for applications like steam sterilization and temperature-controlled processes in food production.Turbine Flow Meters
Best for: Low-viscosity liquids like water, fuels, and low-viscosity oils, as well as certain food and beverage applications.How it Works: Turbine flow meters use a rotor that spins in proportion to the velocity of the liquid flowing through it. As the liquid flows through the meter, the rotational speed of the turbine blades is measured and converted into a flow rate.Pros:- Good accuracy for low-viscosity liquids and high flow rates.
- Cost-effective for applications where high precision isn’t required.
- Wide flow range, making it suitable for both low and high flow rates.
- Moving parts can wear over time, especially in dirty or viscous liquids, requiring regular maintenance.
- Less accurate for low flow rates or liquids with fluctuating flow conditions.
- Not suitable for high-viscosity liquids, as the rotor may not spin efficiently.
Why Recommended: Turbine flow meters are widely used in industries where clean, low-viscosity liquids like water, fuels, and hydraulic oils are measured. In food and beverage applications, sanitary turbine meters are used for measuring low-viscosity liquids like juice, beer, and dairy products. Their affordability and versatility make them a popular choice in both commercial and industrial settings.
How to Choose the Right Liquid Flow Meter
Understand your liquid
Analyze the properties of the liquid you need to measure, including its viscosity, conductivity, temperature, and pressure.Define your requirements
Determine the required accuracy, flow range, and any specific industry standards or regulations you need to meet.Consider your operating conditions
Take into account factors such as temperature, pressure, and the presence of particulates or air bubbles in the liquid.Evaluate installation constraints
Consider the available space, pipe configuration, and accessibility for maintenance when choosing a meter type.Assess long-term costs
Look beyond the initial purchase price and consider factors such as maintenance requirements, energy consumption, and expected lifespan of the meter.Consult with experts
Reach out to flow meter manufacturers or experienced professionals who can provide guidance based on your specific needs.Consider future needs
Choose a flow meter that can accommodate potential changes in your process or expansion of your operations.
Here’s a summary of the best flow meters for different types of liquids and applications:
- For water, wastewater, and slurries: Choose electromagnetic (mag) flow meters, which offer high accuracy and durability in harsh environments.
- For high-viscosity liquids like oils and syrups: Positive displacement flow meters provide high precision and are suitable for low-flow conditions.
- For critical applications requiring mass flow measurement: Opt for Coriolis flow meters, which offer extreme accuracy and are versatile across a range of liquid viscosities.
- For clean, low-viscosity liquids like water and fuels: Turbine flow meters and Vortex Flow Meters offer a cost-effective solution for measuring low-viscosity liquids at high flow rates.
- For non-intrusive installations or non-conductive liquids: Consider ultrasonic flow meters, especially when installation flexibility and maintenance-free operation are priorities.
- For food and beverage applications: Select flow meters designed to meet hygienic standards. Positive displacement, turbine, and Coriolis flow meters with sanitary designs are ideal for handling liquids like milk, juices, syrups, and beer.