Differential Pressure Flow Meters
Working Principles of Different Pressure Flow Meters
Differential pressure flow meters measure the flow rate of fluids by detecting the pressure drop across a constriction or primary element in the flow path. This constriction can be in the form of an orifice plate, Venturi tube, flow nozzle, pitot tube, or a V-cone. The working principle of differential pressure flow meters is based on Bernoulli’s equation, which states that the sum of the static pressure, velocity pressure, and elevation head of a flowing fluid is constant. When a fluid flows through a pipe and encounters a restriction (like an orifice plate, Venturi tube, or V-cone), its velocity increases, and the static pressure decreases. The reduction in pressure is directly proportional to the square of the fluid velocity.
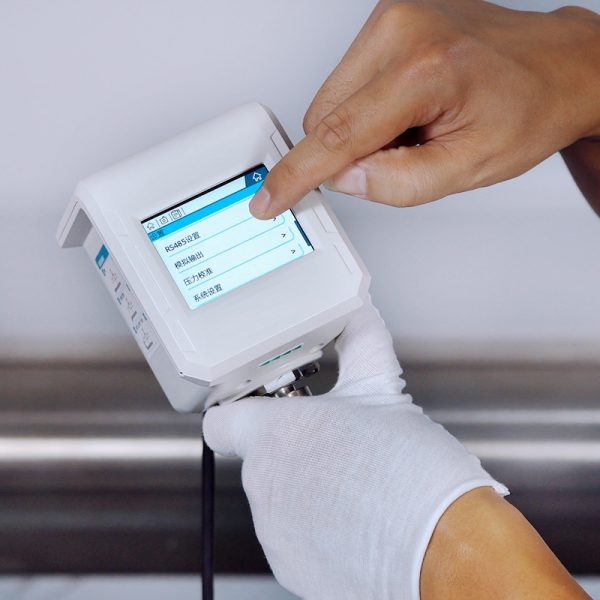
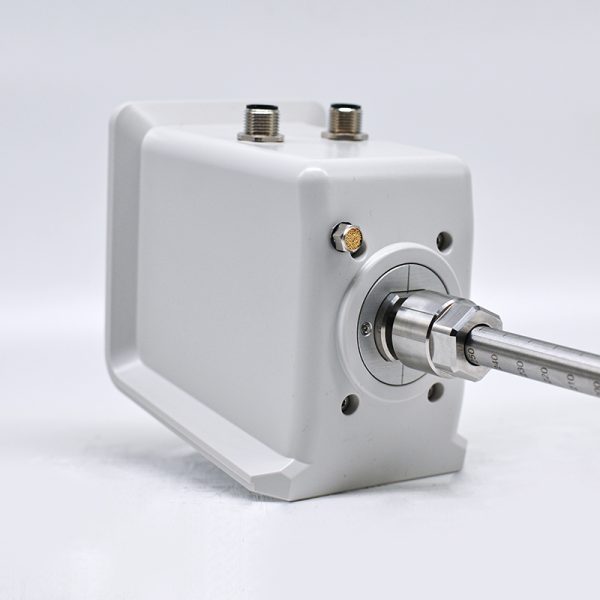
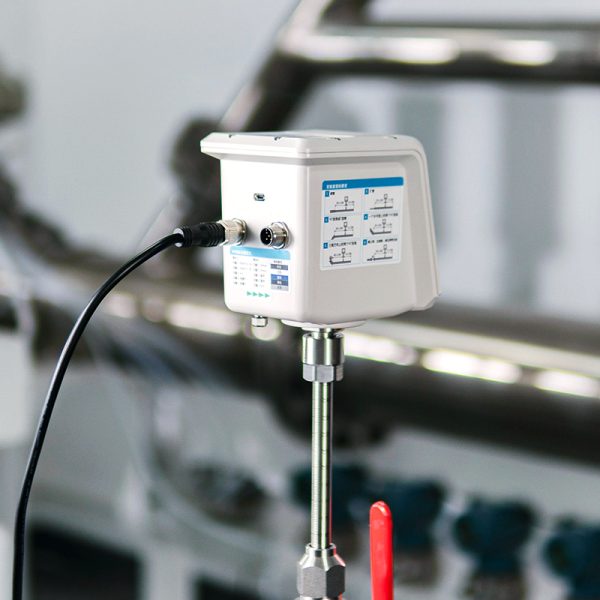
Pitot Tube Gas Flow Meter MTKB-201x
SKUMTKB-201x
Accuracy
±1% RD; ±1.5% RD + 0.3% FS
Medium Temperature Range
standard: -40 TO 150 °C (–40 to +302 °F)
Max. Process Pressure
17 bar (246.56 psi)
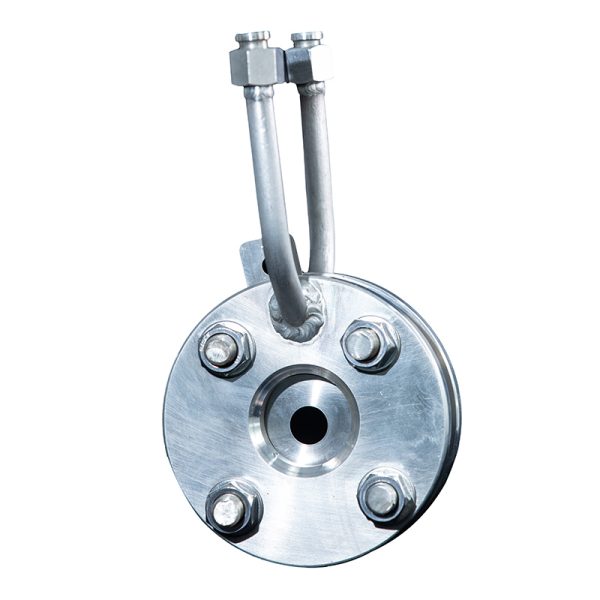
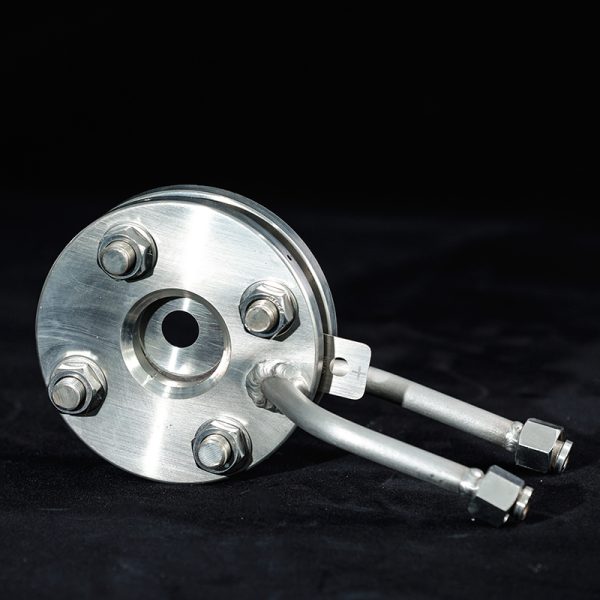
Orifice Plate Flowmeter (MTKB-O)
SKUMTKB-O
Accuracy
±0.075%
Medium Temperature Range
standard: -40 TO 850 °C (–40 to +1562 °F)
Max. Process Pressure
400 bar (5801.52 psi)
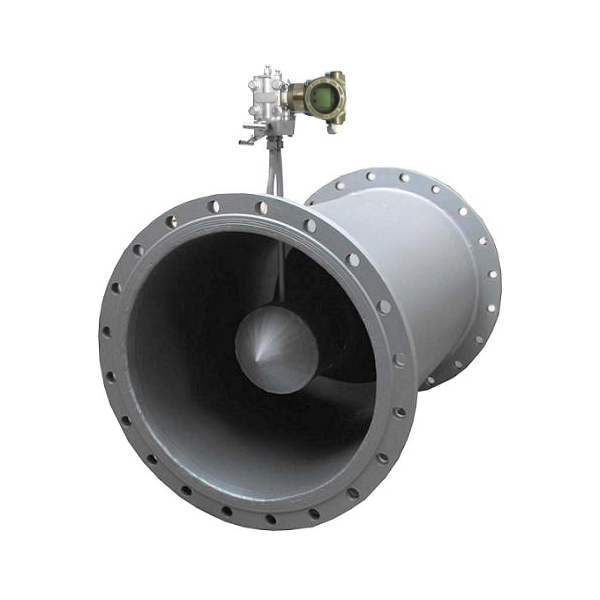
V Cone Different Pressure Flowmeter (MTKB-V)
SKUMTKB-V
Accuracy
±0.5%
Medium Temperature Range
standard: -40 TO 850 °C (–40 to +1562 °F)
Max. Process Pressure
420 bar (6091.6 psi)
Common Types of Differential Pressure Flow Meters
Several types of differential pressure flow meters exist, each designed for specific applications and operating conditions. Below are the most common types:
Orifice Flow Meters:
- Principle: An orifice plate flow meter consists of a flat plate with a sharp-edged hole in the middle. When fluid flows through the orifice, the flow constricts, and the velocity increases, creating a drop in pressure. The difference in pressure upstream and downstream of the orifice plate is measured to calculate the flow rate.
- Advantages: Simple design, low cost, and easy to install and replace.
- Disadvantages: High permanent pressure loss due to flow constriction; requires regular maintenance to ensure accuracy, especially in dirty or corrosive applications.
Venturi Flow Meters:
- Principle: A Venturi tube has a gradually narrowing throat followed by a gradually expanding section. As the fluid flows through the constriction, its velocity increases, causing a drop in pressure that is proportional to the flow rate.
- Advantages: Low pressure loss, high accuracy, and suitable for measuring viscous fluids.
- Disadvantages: Larger size and higher cost compared to orifice plates; difficult to install in small spaces.
Flow Nozzle Flow Meters:
- Principle: Similar to the Venturi tube but with a simpler design, the flow nozzle has a smooth, converging section that leads to a throat where the pressure differential is measured.
- Advantages: High accuracy, good for high-velocity flows, and less susceptible to wear.
- Disadvantages: Moderate pressure loss, less rangeability compared to Venturi tubes.
Pitot Tubes:
- Principle: Pitot tubes measure fluid flow velocity by converting kinetic energy in the fluid into potential energy. The difference between the static pressure and the total (stagnation) pressure is used to calculate the flow velocity.
- Advantages: Simple design, low cost, minimal pressure loss, and easy to install.
- Disadvantages: Less accurate for turbulent flows; sensitive to alignment and requires frequent cleaning.
V-Cone Flow Meters:
- Principle: The V-cone flow meter is a unique type of differential pressure meter that uses a cone-shaped obstruction in the center of the pipe. The cone reshapes the velocity profile and stabilizes the fluid flow, creating a differential pressure that can be measured to determine the flow rate.
- Advantages: High accuracy and repeatability; low permanent pressure loss; less sensitivity to flow disturbances; requires minimal straight-run piping.
- Disadvantages: Higher initial cost compared to traditional orifice plates; installation may require specialized training.
Differential Pressure Piping, Installation, and Maintenance
The performance and accuracy of differential pressure flow meters heavily depend on proper installation, piping configuration, and regular maintenance.
- Piping Requirements: DP flow meters require straight runs of pipe upstream (typically 10 diameters) and downstream (5 diameters) from the flow element to ensure a fully developed flow profile. Inadequate straight piping can lead to inaccurate readings.
- Installation Considerations: Differential pressure flow meters should be installed in a location that minimizes flow disturbances. They should be positioned away from bends, elbows, valves, and other flow-disturbing fittings. The pressure taps must be clean, properly aligned, and free from blockages.
- Maintenance Practices: Regular inspection, calibration, and maintenance are essential to keep DP flow meters accurate. Orifice plates, nozzles, and other primary elements should be checked for wear, corrosion, or debris buildup. Calibration should be performed periodically to ensure that the measurement is within the specified accuracy range.
Applications of Differential Pressure Flow Meters
Due to their versatility and reliability, differential pressure flow meters are used across various industries, including:
- Oil and Gas: For measuring the flow of crude oil, natural gas, steam, and other process fluids in pipelines and refineries. Orifice plates and V-cone meters are particularly popular in these applications due to their high-pressure capability.
- Water and Wastewater Treatment: Used for measuring the flow of water, chemicals, and sludge in treatment plants and distribution networks. Venturi tubes and flow nozzles are common choices in these settings due to their low-pressure loss and high reliability.
- Power Generation: Used for measuring steam flow in boilers, feedwater in turbines, and other fluids critical to power plant operation. The Venturi tube and orifice plate meters are commonly employed in these applications.
- Chemical and Petrochemical Industries: Used to measure the flow of corrosive and toxic chemicals, high-temperature fluids, and other process streams. The V-cone flow meter is particularly advantageous in these settings due to its robust design and low-maintenance requirements.
- HVAC Systems: Used for measuring the flow of water and air in heating, ventilation, and cooling systems. Pitot tubes and annubar flow meters are often used due to their low-pressure drop and ease of installation.
- Food and Beverage: Used for measuring the flow of water, milk, syrups, and other ingredients in processing plants. Annubar and Venturi meters are often selected for their sanitary design and accurate flow measurement capabilities