Turbine Flow Meters
Working Principle of Turbine Flow Meters
Turbine flow meters operate by detecting the velocity of fluid passing through a pipe, which causes a turbine or rotor within the flow tube to spin. The speed of the rotor’s rotation, which is directly proportional to the fluid’s flow rate, is measured by sensors (magnetic or optical) placed outside the tube. These sensors generate electrical pulses corresponding to the rotor’s revolutions, which are then converted into a readable flow rate by a flow transmitter, displaying the measurement in units such as liters per minute (LPM) or gallons per minute (GPM).
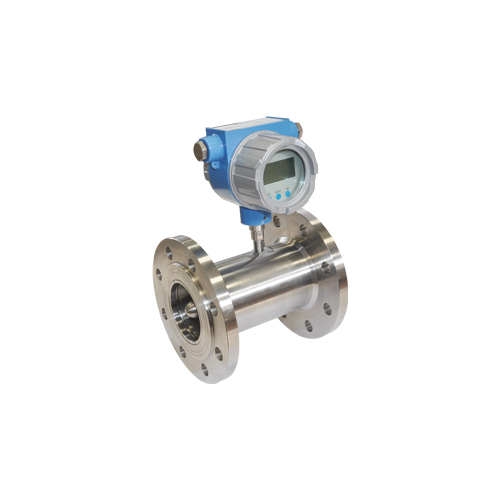
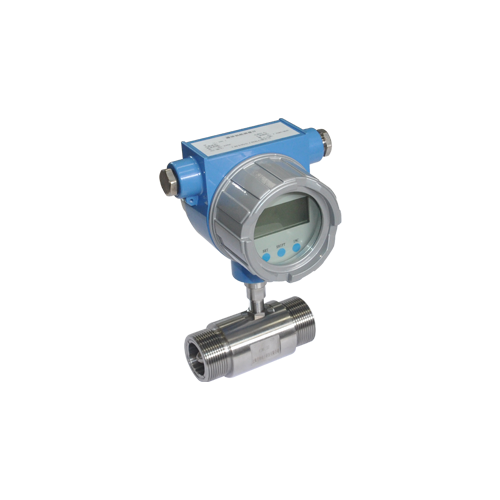
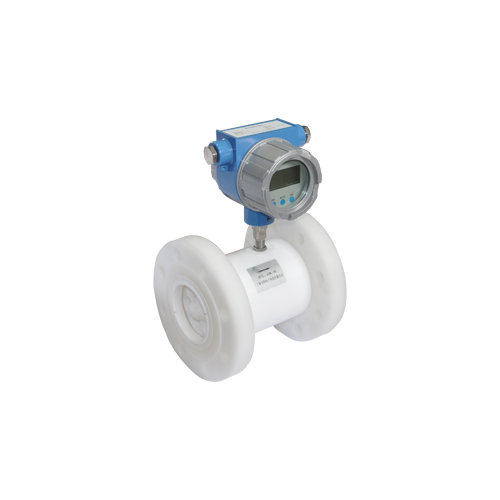
High Accuracy Liquid Turbine Flow Meter (LWGYMT-AJWL)
Accuracy
±0.2 %; ±0.5 %
Measuring Range
0.004 to 1800 m³/h
Medium Temperature Range
standard: -196 TO 180 °C (−320.8 to +356 °F)
Max. Process Pressure
350 bar
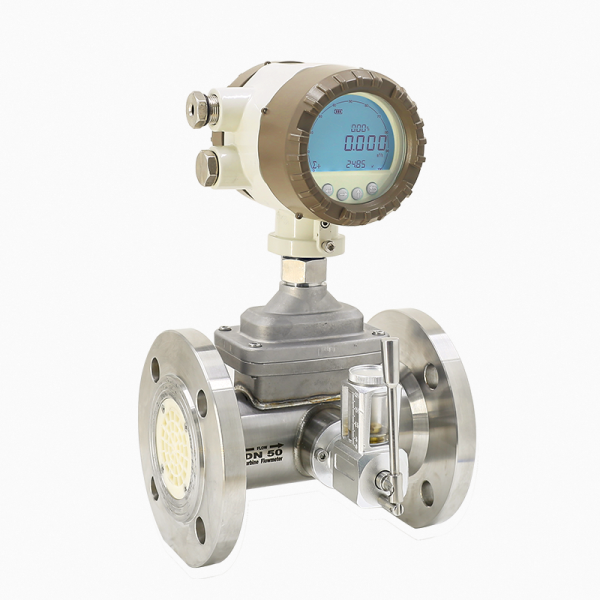
High Accuracy Turbine Gas Flow Meters (LWGYMT-ES)
Accuracy
±1.0%; ±1.5%
Measuring Range
4 to 13000 m³/h
Medium Temperature Range
standard: -25°C~+55°C (–13 to +131 °F)
Max. Process Pressure
63 bar (913.74 psi)
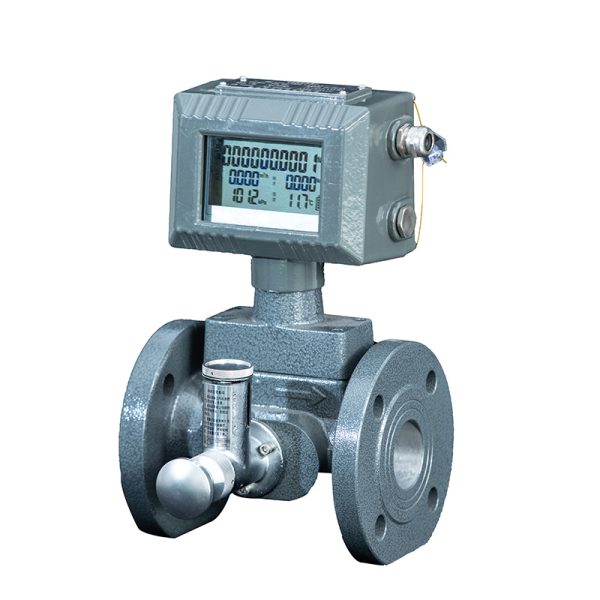
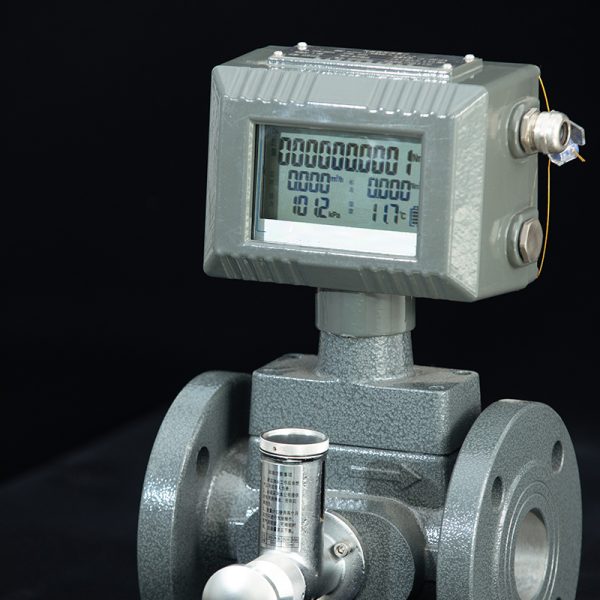
Gas Turbine Flow Meters\ (LWGYMT-G)
Accuracy
±1.5 %
Measuring Range
2 to 1000 m³/h
Medium Temperature Range
standard: -20 TO 120 °C (–4 to +248 °F)
Max. Process Pressure
63 bar (913.74 psi)
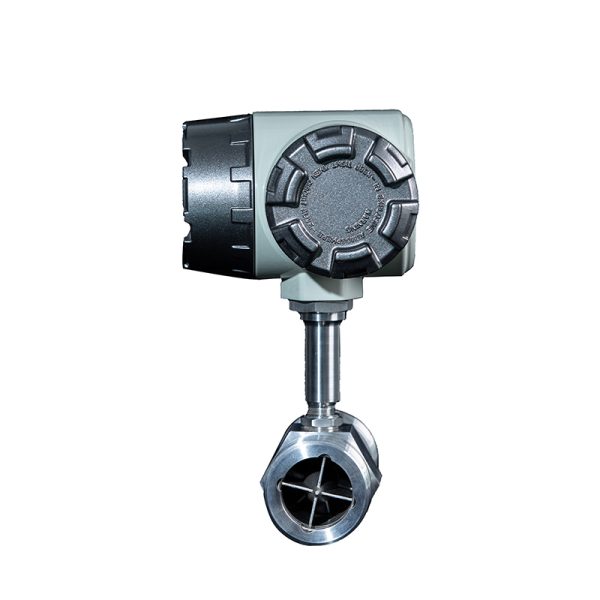
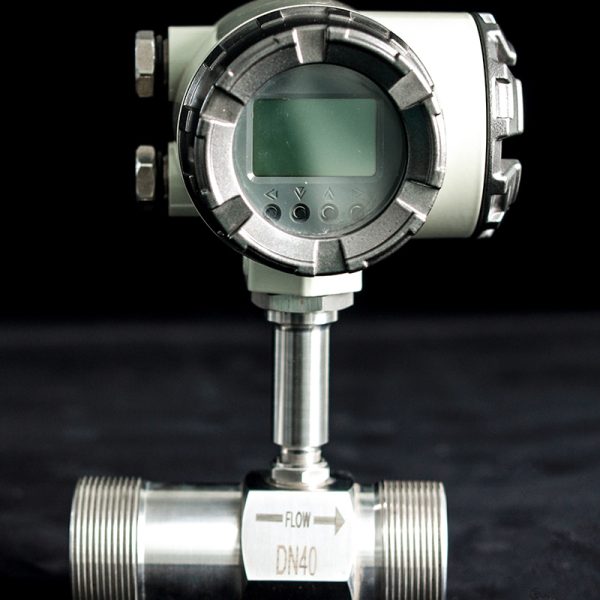
Liquid Turbine Flow Meter (LWGYMT-100)
Accuracy
Standard: ±1 %, Optional: ±0.5 %
Measuring Range
0.04 to 800 m³/h
Medium Temperature Range
standard: -20 TO 120 °C (–4 to +248 °F)
Max. Process Pressure
250 bar (3625.95 psi)
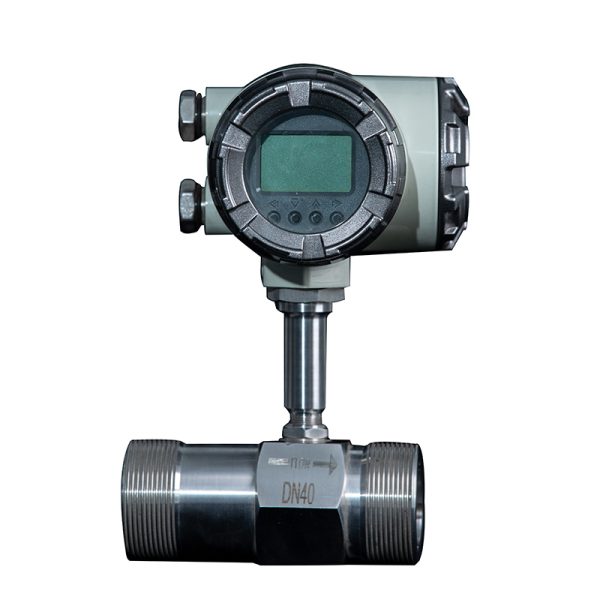
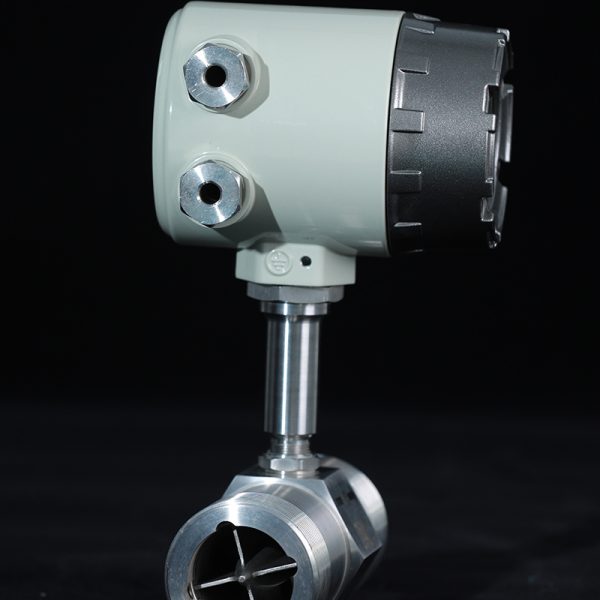
Low Flow Liquid Turbine Flow Meter (LWGYMT-F)
Accuracy
Standard: ±1 %, Optional: ±0.5 %
Measuring Range
0.04 to 200 m³/h
Medium Temperature Range
standard: -20 TO 120 °C (–4 to +248 °F)
Max. Process Pressure
160 bar (2320.6 psi)
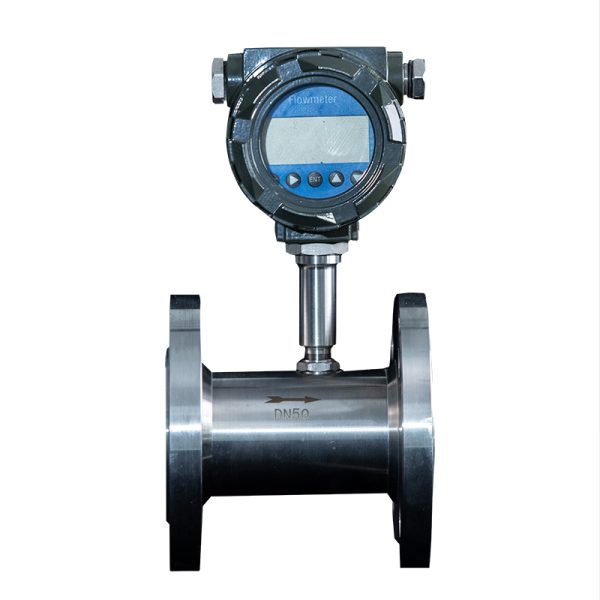
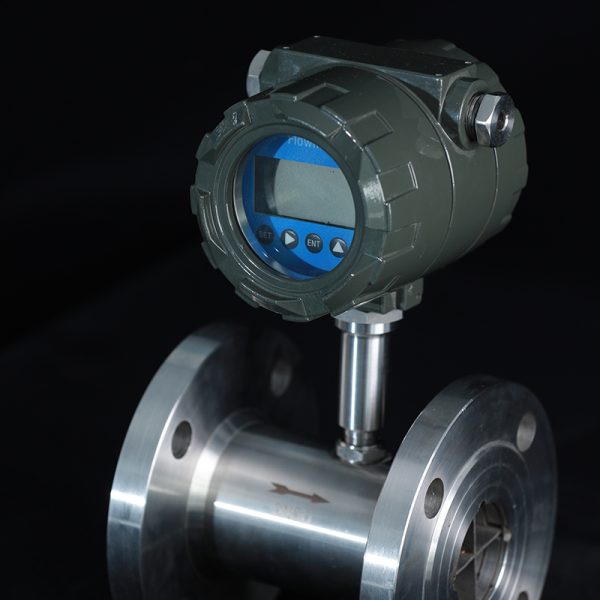
High Pressure Liquid Turbine Flow Meter (LWGYMT-P)
Accuracy
Standard: ±1 %, Optional: ±0.5 %
Measuring Range
0.4 to 800 m³/h
Medium Temperature Range
standard: -20 TO 120 °C (–4 to +248 °F)
Max. Process Pressure
250 bar (3625.95 psi)
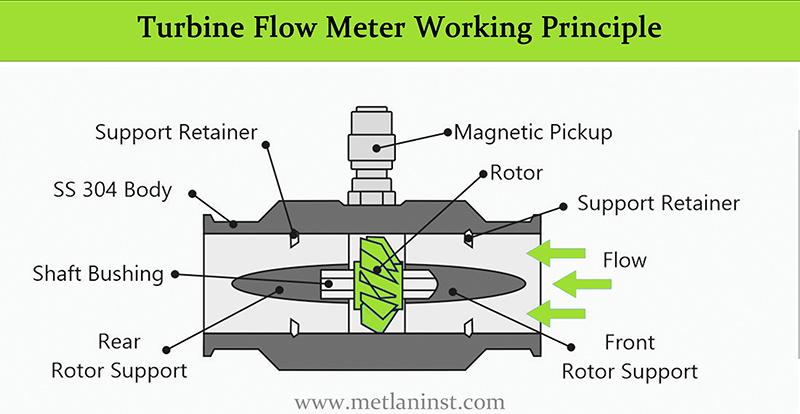
Advantages and Disadvantages of Turbine Flow Meters
Advantages
- High accuracy at an economic price
- Fast Response Time
- Easy to install and maintain
- Low pressure-drop
- Can measure low flow rates
Disadvantages
- Clean and low viscosity fluids only
- Pipes must be consistently full for accuracy
- Straight piping requirements to reduce flow turbulence
- Ferrous and magnetic particles should be filtered out upstream for some models
Connection Types of Turbine Flow Meters
Flange Connection
Flange connections are the most common type used for turbine flow meters, especially in industrial settings. The meter is attached to the pipeline using flanges bolted together, ensuring a secure and leak-proof connection. This type of connection is highly reliable and suitable for high-pressure and high-temperature applications. Flange connections are typically used in larger pipelines where durability and a strong seal are required.Threaded Connection
Threaded connections involve screwing the turbine flow meter directly into the pipeline using threaded ends. This type is more commonly used for smaller pipelines and low to medium-pressure applications. Threaded connections are easier to install and remove, making them a cost-effective option for smaller systems or applications where the meter needs to be frequently removed or replaced.Clamp-On Connection
Clamp-on connections use clamps to attach the turbine flow meter to the outside of a pipeline, allowing for non-intrusive installation. This type does not require cutting into the pipe or interrupting the flow, making it ideal for applications where the pipe must remain intact or when measuring corrosive or hazardous fluids. Clamp-on connections are easy to install, maintain, and relocate but may provide slightly lower accuracy compared to flange or threaded connections due to the indirect measurement approach.
Available Media of Turbine Flow Meters
Turbine flow meters are versatile and can measure various fluids, including:- Liquids: Water, light oils, fuels, alcohols, solvents, and other low-viscosity liquids.
- Gases: Natural gas, compressed air, nitrogen, and other clean gases.
Applications of Turbine Flow Meters
- Oil and Gas Industry
- Water and Wastewater Management
- Chemical and Petrochemical Industries
- Pharmaceutical Industry
- Food and Beverage Industry
- HVAC Systems
- Aerospace and Automotive Industries