Mass flow meters are vital instruments in a wide variety of industries. They measure the mass of a fluid that flows through a pipe or duct over a specified period of time. Unlike volumetric flow meters, which measure the volume of fluid passing through, mass flow meters provide more accurate readings for specific applications where density variations or changes in temperature can affect the fluid’s behavior.
Table of Contents
What Is a Mass Flow Meter?
A mass flow meter is a device used to measure the flow of fluids—either liquids or gases—based on their mass rather than their volume. The primary difference between mass flow meters and other types of flow meters (such as volumetric flow meters) is that mass flow meters account for the changes in density that can occur with variations in temperature, pressure, or the fluid’s composition. This makes them ideal for applications where precise control of fluid flow and consistency in measurements are critical.
Mass flow meters are commonly used to monitor processes, ensure compliance with regulations, and optimize system efficiency. These meters can be found in industries such as chemical processing, food and beverage, oil and gas, pharmaceuticals, and environmental monitoring.
The History of Mass Flow Measurement
The evolution of mass flow measurement began with the need for more accurate and reliable ways to measure fluid flow, especially in industries where controlling the mass of a fluid was more critical than its volume.
Early Developments:
In the late 19th century, the first rudimentary mass flow meters were developed. These early devices were based on mechanical principles and were limited in scope and accuracy. They relied on physical displacement or mechanical counting, where the mass flow was inferred based on the volume of liquid passing through.
Coriolis Mass Flow Meters:
The breakthrough in mass flow measurement came in the early 20th century with the development of the Coriolis effect. The Coriolis effect, named after French scientist Gaspard-Gustave Coriolis, refers to the apparent deflection of moving fluids within a rotating system. By exploiting this effect, scientists and engineers developed the Coriolis mass flow meter in the 1950s and 1960s. These meters provided the first accurate and direct measurement of mass flow, as they directly measured the twisting of tubes caused by the moving fluid.
The Coriolis flow meter remains one of the most accurate and widely used mass flow meters in modern applications.
Thermal Mass Flow Meters:
In the 1980s, thermal mass flow meters became popular, especially for gases. These meters rely on the heat transfer properties of fluids and are particularly well-suited for gases due to their ability to measure low flow rates with high accuracy.
How Does a Mass Flow Meter Work?
The working principle of a mass flow meter depends on its specific design. However, most mass flow meters operate by detecting the physical properties of the fluid—such as its density, velocity, or the forces exerted by the moving fluid—and converting these measurements into mass flow readings.
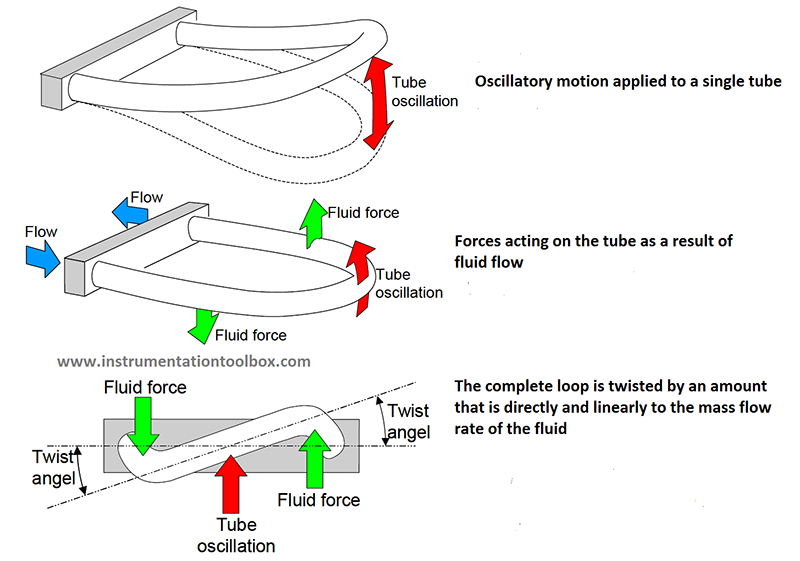
Coriolis Mass Flow Meter Principle: Coriolis mass flow meters measure the flow of mass by detecting changes in the vibration of a flow tube. When the fluid flows through the tube, it causes the tube to twist. The amount of twist is directly proportional to the mass flow rate. This type of flow meter can measure mass flow, density, and temperature simultaneously, offering highly accurate readings.
More about Coriolis Flow Meters
Thermal Mass Flow Meter Principle: Thermal mass flow meters operate by measuring the heat dissipated by the flowing fluid. They typically use a heated sensor and a reference sensor placed upstream and downstream of the measurement point. As fluid flows past, it carries heat away from the heated sensor, and the temperature difference is used to calculate the mass flow rate.
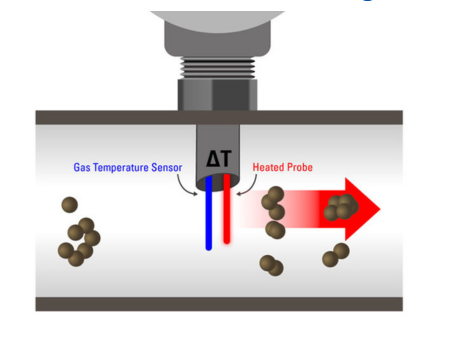
Advantages and Limitations of Mass Flow Meters
Advantages:
- High Accuracy: Mass flow meters, especially Coriolis meters, provide highly accurate measurements, even in challenging conditions.
- No Need for Calibration with Density: Unlike volumetric flow meters, mass flow meters don’t require calibration based on fluid density variations, making them ideal for applications where fluid properties can change.
- Versatility: They can measure a wide range of fluids, including liquids, gases, and slurries.
- Simultaneous Measurement of Mass and Density: Some mass flow meters can measure both mass flow and fluid density, which is invaluable for process control.
Limitations:
- High Initial Cost: Mass flow meters, particularly Coriolis meters, can be expensive, which may be a drawback for some businesses.
- Size and Complexity: Some types of mass flow meters, such as Coriolis, are large and may require complex installation.
- Susceptibility to Vibration: In some cases, external vibrations can affect the accuracy of the measurements, especially with Coriolis meters.
Applications of Mass Flow Meters
Mass flow meters are used in numerous industries where precise control and measurement of fluid flow are critical. Some of the key applications include:
1. Oil and Gas Industry
Mass flow meters are essential in the oil and gas industry for measuring the flow of crude oil, natural gas, and refined products. Accurate measurement is crucial for custody transfer and ensuring accurate billing in production and distribution systems.
2. Chemical Processing
In chemical plants, precise measurement of mass flow helps ensure that reactions proceed as planned. Mass flow meters are used to monitor and control the flow of reactants and products in processes such as polymer production, chemical synthesis, and blending.
3. Food and Beverage Industry
The food and beverage industry uses mass flow meters to monitor the precise amount of ingredients being used in production. For example, mass flow meters are used to ensure the correct dosing of ingredients in manufacturing soft drinks, sauces, and other liquid products.
4. Pharmaceuticals
In the pharmaceutical industry, mass flow meters are used in the production of vaccines, antibiotics, and other products requiring precise formulations. These meters help maintain product quality and compliance with strict regulations.
5. HVAC Systems
Thermal mass flow meters are widely used in HVAC systems to measure the flow of air and gases. Accurate measurement of air flow is critical for maintaining optimal building conditions and energy efficiency.
Mass flow meters are indispensable tools in industries where precision in fluid flow measurement is essential. They offer unparalleled accuracy and versatility, making them suitable for a wide range of applications, from chemical processing to pharmaceuticals and HVAC systems. By understanding the different types of mass flow meters, their working principles, advantages, limitations, and appropriate applications, businesses can select the right technology to optimize their processes and ensure operational efficiency.
Leave a comment