1. Gas Retention in the Pipeline
There are two common causes of gas retention in the pipeline:
- Failure to purge air from the pipeline before commissioning: If the air in the pipeline is not adequately removed before the system is activated, gas will accumulate at the high points of the pipeline. When fluid flows, the gas is carried along and exits in the form of bubbles.
- Small bubbles carried in the liquid accumulating at high points: Small bubbles in the liquid gradually accumulate in the pipeline, leading to gas retention at high points.
The fault typically manifests as a discrepancy between the measured flow rate and the actual flow rate, as well as unstable or fluctuating output signals.
Case Study:
A petrochemical plant in Nanjing used DN1000mm pipelines to draw water from the Yangtze River, with a pipeline length of 10km, passing through small hills. A DN700mm electromagnetic flow meter was installed at the high point of the pipeline. After commissioning, the flow meter failed to function properly. Upon site inspection, unusual water flow sounds were detected near the flow meter. Preliminary analysis indicated that the pipeline had not been purged of air, and the system design did not include a vent valve at the high point, preventing the gas from being expelled. The electrode signal measured up to 4mV, most of which was interference voltage. Since the water flow could not be stopped for further inspection, the issue remained unresolved. Several months later, after a follow-up by the manufacturer’s maintenance team, the sound of water flow was no longer heard. This was because the remaining air was carried away by the flowing water. After recalibration, the flow meter resumed normal operation.
2. Continuous Gas Ingestion
Continuous gas ingestion can also cause flow meter issues, especially in water tanks or similar installations, where insufficient water levels lead to the ingestion of air bubbles, affecting the measurement.
Case Study:
At a water plant in Guangxi, a clear water tank was set up on a hill in the suburb, utilizing the potential energy of the tank’s height to send water. Operators reported that the DN700mm electromagnetic flow meter sometimes displayed unstable flow rates, with errors as large as 20%. Site inspection revealed an issue with the installation position of the flow meter. When the water level was insufficient, air bubbles were sucked in, and at times, the flow meter’s measurement pipe was not fully filled. Specifically, when the water level dropped below Line A, although the intake remained above the water surface, the low water level would still cause a vortex at Point C, pulling in air from the water surface and forming bubbles, leading to unstable readings. If the water level fell to Line B, the measurement pipe would become empty. To resolve this, we recommended installing a bend as shown in the dotted line, expanding the effective capacity of the water tank to reduce the chance of air ingestion, and compensating for the shortcomings of the original design.
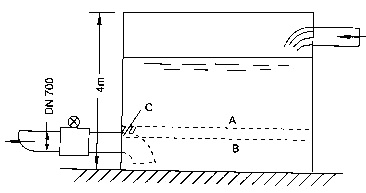
Summary
These cases demonstrate that gas-related issues—whether from gas retention or continuous ingestion—can significantly affect the operation of electromagnetic flow meters. To ensure accurate and stable readings, it is crucial to design pipelines with effective air purging measures and ensure the measurement pipes are fully filled with liquid. In practical applications, problems like these can be addressed by adjusting pipeline structures and expanding tank capacities to prevent the formation and accumulation of air bubbles, thus improving flow meter measurement accuracy.
More Case Studies of Mag Meters:
- Case Study: Biopharmaceutical Production Line for Erythromycin
- Application of Flow Meters in the Pyrrolidone Series Product Production Project
- District Heating Station Project Solution
- Wine Filling Process Flow Monitoring and Control
Leave a comment