In industries ranging from oil and gas to healthcare and environmental monitoring, gas flow meters or air flow meters play a crucial role in ensuring the accurate measurement and control of gas flow. These devices are designed to measure the flow rate of gases in pipelines or open systems, helping to optimize processes, ensure safety, and meet regulatory standards. In this comprehensive guide, we will explore what gas flow meters are, the types of gases they measure, the different types of gas flow meters, their applications, and the advantages and limitations of each type.
Table of Contents
What is a Gas Flow Meter?
A gas flow meter is an instrument used to measure the volume, mass, or velocity of a gas moving through a pipeline or an open system. Accurate gas flow measurement is essential in numerous industries to monitor and control processes, detect leaks, reduce waste, and ensure compliance with environmental and safety standards.
Gas flow meters operate based on different measurement principles, such as differential pressure, thermal conductivity, ultrasonic waves, or vortex shedding. The choice of a gas flow meter depends on factors such as the type of gas, flow rate, pressure, temperature, and required accuracy.
Common Types of Gases Measured in Different Industries
Gas flow meters are versatile instruments used to measure a wide variety of gases across industries. Some common examples include:
- Natural Gas:
- Industry: Energy, utilities.
- Purpose: Distribution, billing, and combustion monitoring in power plants.
- Compressed Air:
- Industry: Manufacturing, automotive.
- Purpose: Monitoring air tools, pneumatic systems, and compressors.
- Oxygen (O₂):
- Industry: Healthcare, industrial welding.
- Purpose: Medical oxygen delivery, process control in welding.
- Carbon Dioxide (CO₂):
- Industry: Beverage, agriculture, environmental.
- Purpose: Carbonation in beverages, greenhouse monitoring, emissions measurement.
- Steam:
- Industry: Power generation, food processing.
- Purpose: Energy transfer, sterilization, and cooking.
- Hydrogen (H₂):
- Industry: Fuel cells, chemical production.
- Purpose: Energy applications, production of ammonia and methanol.
- Nitrogen (N₂):
- Industry: Food packaging, electronics manufacturing.
- Purpose: Inert gas for preservation and protective environments.
- Biogas:
- Industry: Waste management, renewable energy.
- Purpose: Monitoring production in anaerobic digesters and fuel applications.
Types of Gas Flow Meters
Different types of gas flow meters are available, each with unique advantages and limitations. Below are the most commonly used types:
1. Thermal Mass Flow Meters
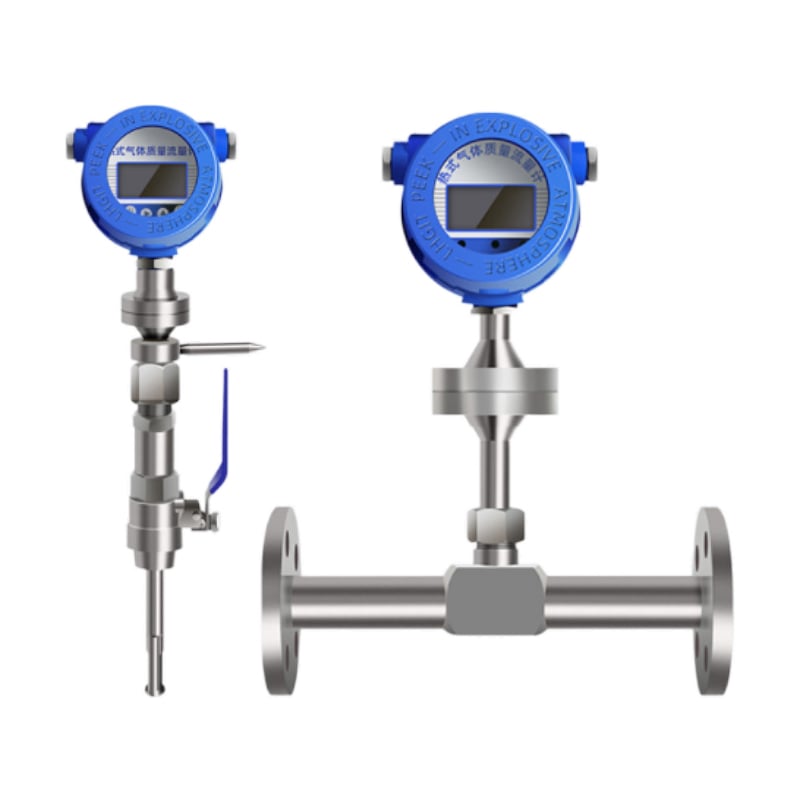
Advantages:
- Direct measurement of mass flow.
- Highly accurate for low-flow applications.
- Suitable for various gases, including air, nitrogen, and natural gas.
Limitations:
- Limited to clean, dry gases (moisture or particulates can affect accuracy).v
- Sensitive to changes in gas composition.
How They Work:
- Measure heat transfer between a heated sensor and the gas flow, correlating to mass flow rate.
Applications:
- HVAC systems, environmental emissions monitoring, and process control.
2. Coriolis Mass Flow Meters
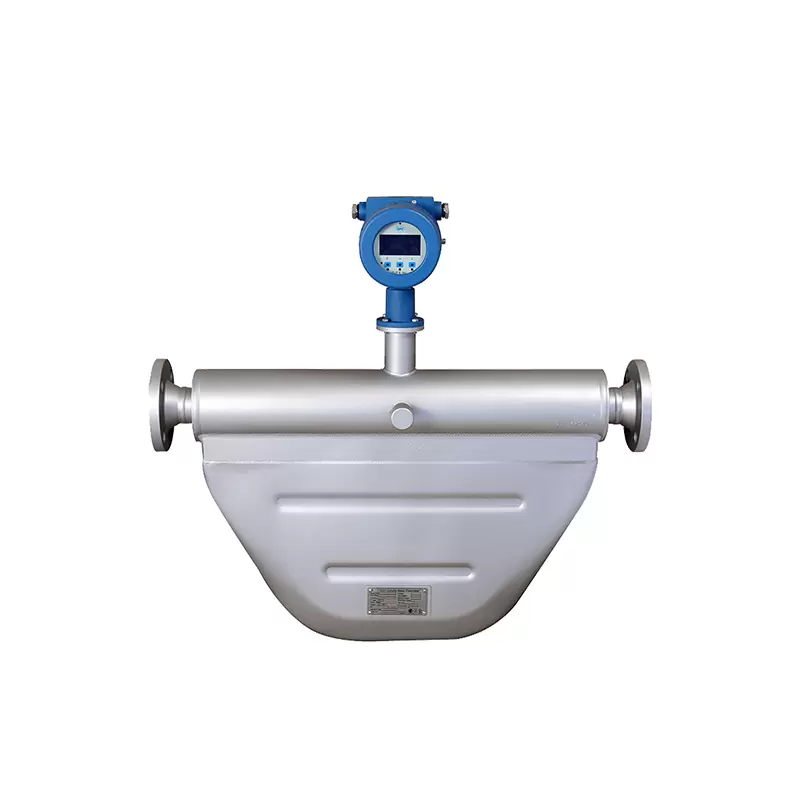
Advantages:
- Extremely accurate and reliable.
- Measure mass flow directly.
- Suitable for both low and high flow rates.
Limitations:
- Pressure drop in high-flow applications.
- High initial cost.
How They Work:
- Use Coriolis forces to measure the mass flow rate of gases.
Applications:
- High-value gas measurement, hydrogen fuel systems, and medical oxygen.
3. Differential Pressure Flow Meters
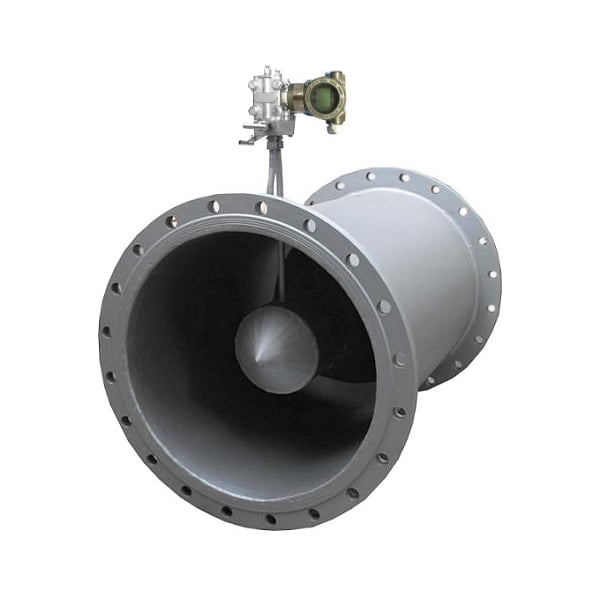
Advantages:
- Suitable for a wide range of gases.
- Cost-effective for high-pressure and high-temperature applications.
- Simple design and easy to install.
Limitations:
- Regular maintenance required to prevent clogging.
- Pressure drop can reduce efficiency.
- Limited accuracy compared to advanced meters.
How They Work:
- Measure the pressure drop across a restriction (e.g., orifice plate, venturi tube) in the flow path.
Applications:
- Natural gas distribution, steam flow measurement, and compressed air systems.
4. Vortex Flow Meters
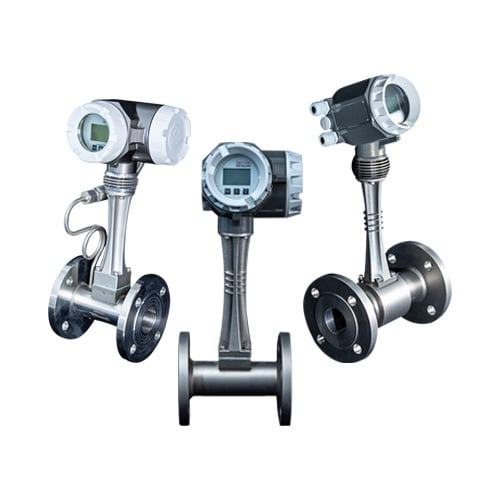
Advantages:
- No moving parts, reducing maintenance needs.
- Suitable for a wide range of temperatures and pressures.
- Accurate for medium to high flow rates.
Limitations:
- Sensitive to vibration and noise interference.
- Not ideal for low flow rates or gases with large particulates.
How They Work:
- Measure the frequency of vortices created by a bluff body placed in the gas flow.
Applications:
- Steam measurement, industrial gas flow monitoring, and HVAC systems.
5. Ultrasonic Flow Meters
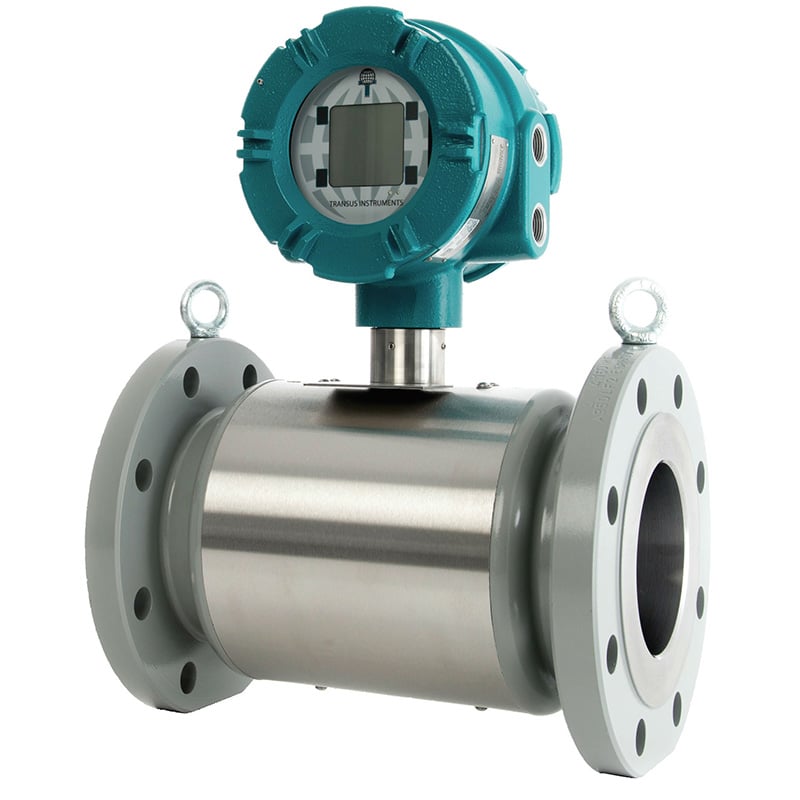
Advantages:
- Non-intrusive (clamp-on models available).
- Highly accurate and suitable for large pipelines.
- No moving parts, minimizing maintenance.
Limitations:
- Sensitive to temperature and pressure changes.
- Expensive compared to other types.
How They Work:
- Use sound waves to measure gas velocity. Transit-time meters measure the time difference of sound waves traveling with and against the flow, while Doppler meters measure frequency shifts caused by gas particles.
Applications:
- Natural gas pipelines, biogas monitoring, and industrial gases.
6. Rotameters (Variable Area Flow Meters)
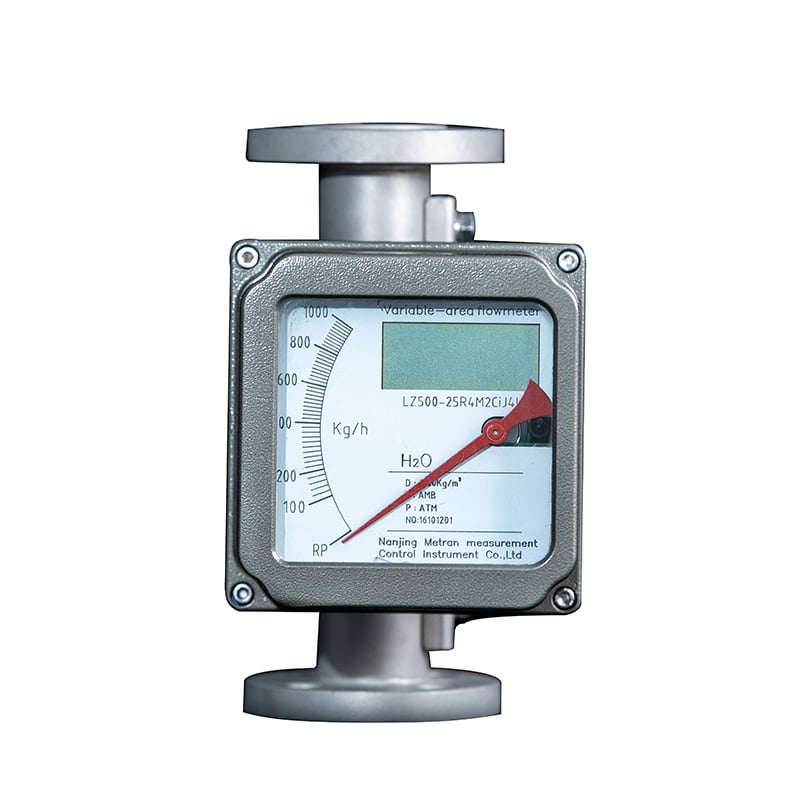
Advantages:
- Simple design and cost-effective.
- Easy to install and use.
- No power source required.
Limitations:
- Must be installed vertically.
- Limited accuracy and range.
How They Work:
- Measure flow rate based on the vertical position of a float inside a tapered tube.
Applications:
- Laboratory gas measurements and flow monitoring in medical applications.
Applications of Gas Flow Meters
Gas flow meters are essential in numerous industries for various applications:
1. Energy and Utilities
- Monitoring natural gas flow in distribution networks.
- Measuring steam flow in power plants for energy efficiency.
2. Manufacturing and Industry
- Managing compressed air systems in factories.
- Monitoring gas flow in chemical processes.
3. Healthcare
- Regulating oxygen flow for patients in hospitals.
- Controlling medical gas mixtures in anesthesia equipment.
4. Environmental Monitoring
- Measuring emissions of CO₂ and other gases to ensure regulatory compliance.
- Monitoring methane or biogas in waste treatment facilities.
5. Food and Beverage
- Carbonation of beverages using CO₂.
- Ensuring inert gas flow (e.g., nitrogen) in packaging processes.
6. Renewable Energy
- Measuring hydrogen flow in fuel cell systems.
- Monitoring biogas production in anaerobic digesters.
How to Choose the Right Gas Flow Meter
Choosing the right gas flow meter depends on several factors:
- Type of Gas: Determine whether the gas is clean, corrosive, or contains particulates.
- Flow Rate Range: Ensure the flow meter can handle the expected flow range.
- Accuracy Requirements: Select a flow meter that meets the precision needed for the application.
- Operating Conditions: Consider temperature, pressure, and environmental factors.
- Installation Constraints: Decide whether a non-intrusive or inline meter is more practical.
- Budget: Balance cost with performance and maintenance requirements.
Gas flow meters are indispensable tools for accurately measuring and controlling the flow of gases in a wide range of industries. From simple rotameters to advanced Coriolis mass flow meters, each type has its unique strengths and limitations. Understanding the specific requirements of your application—such as the type of gas, flow conditions, and accuracy needs—will help you select the most suitable gas flow meter for your operations.
Whether you’re managing a natural gas pipeline, monitoring emissions, or ensuring patient safety in healthcare, gas flow meters provide the precision and reliability needed to optimize processes and maintain compliance. By choosing the right technology, you can ensure efficiency, reduce costs, and achieve your operational goals.
Related Post: How to Choose LPG Flow Meter
Leave a comment