Flow measurement is an essential part of industrial and scientific processes. Among the various flow measurement devices, Rotameters stand out for their simplicity, reliability, and versatility. They are widely used in laboratories, industrial processes, and medical equipment to measure the flow rate of liquids and gases. This blog post will cover everything you need to know about Rotameters, including their construction, working principles, characteristics, types, advantages, limitations, and applications.
Table of Contents
What is a Rotameter?
A Rotameter is a type of variable area flow meter that measures the flow rate of fluids (liquids or gases) in a vertical tube. The device operates based on gravity and the fluid’s dynamic forces. The term “Rotameter” is derived from the rotation of the float, which is used to indicate the flow rate.
Rotameters are commonly used because they are simple, cost-effective, and require no external power source. They provide a direct visual indication of the flow rate, making them easy to use and maintain.
Construction of Rotameters
A Rotameter consists of the following primary components:
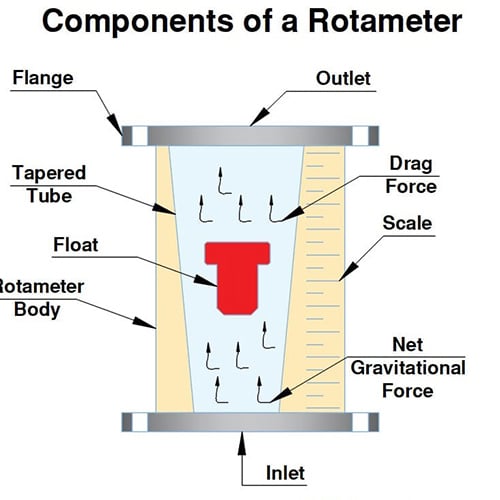
- Tapered Tube:
- Made of transparent material like glass or plastic (for visible flow) or metal (for durability in high-pressure or opaque conditions).
- The tube is vertically aligned, with the diameter increasing from bottom to top.
- Float:
- A solid object (usually metal, plastic, or ceramic) inside the tube.
- The float moves freely up and down in response to the fluid flow rate.
- The shape of the float varies depending on the application (e.g., spherical, ellipsoidal, or conical).
- Scale or Markings:
- Graduations or markings on the tube indicate the flow rate.
- Calibration is specific to the fluid being measured (considering viscosity, density, and pressure).
- Inlet and Outlet Connections:
- The tube has an inlet at the bottom and an outlet at the top, allowing the fluid to flow vertically upward.
- Flow Control Valve (Optional):
- Some Rotameters are equipped with a valve to regulate the flow rate.
Working Principles of Rotameters
The working of a Rotameter is based on the principles of gravity and fluid dynamics:
- The fluid enters the Rotameter through the bottom inlet and flows upward through the tapered tube.
- The float inside the tube is lifted by the force of the fluid flow.
- As the float rises, the increasing cross-sectional area of the tube reduces the velocity of the fluid and increases the flow area.
- The float reaches a position where the upward force exerted by the fluid equals the downward gravitational force acting on the float.
- The position of the float is proportional to the flow rate and is read against the calibrated scale on the tube.
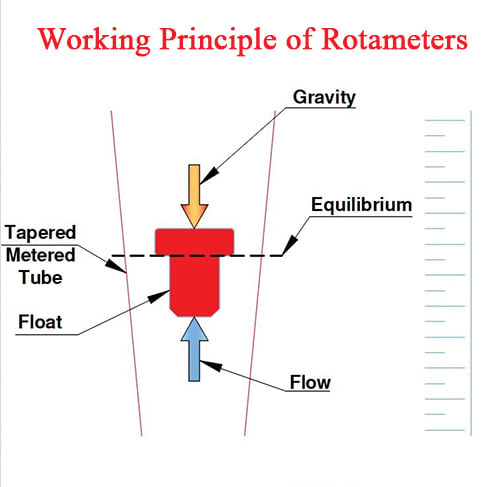
Key forces involved:
- Buoyancy: The upward force exerted by the fluid.
- Gravitational Force: The weight of the float pulling it downward.
- Drag Force: The resistance created by the flow around the float.
Characteristics of Rotameters
- Flow Proportionality: The float’s position is directly proportional to the flow rate.
- Linear Scale: Rotameters provide a linear relationship between float position and flow rate, making them easy to read.
- Gravity Dependency: Rotameters must be installed vertically for accurate measurement.
- Pressure and Temperature Sensitivity: Performance can vary with changes in fluid pressure and temperature.
- Fluid Compatibility: Rotameters are compatible with a wide range of liquids and gases, provided the material of construction suits the fluid properties.
Different Types of Rotameters
Rotameters come in various designs tailored to specific applications. Here are the main types:
1. Glass Tube Rotameters
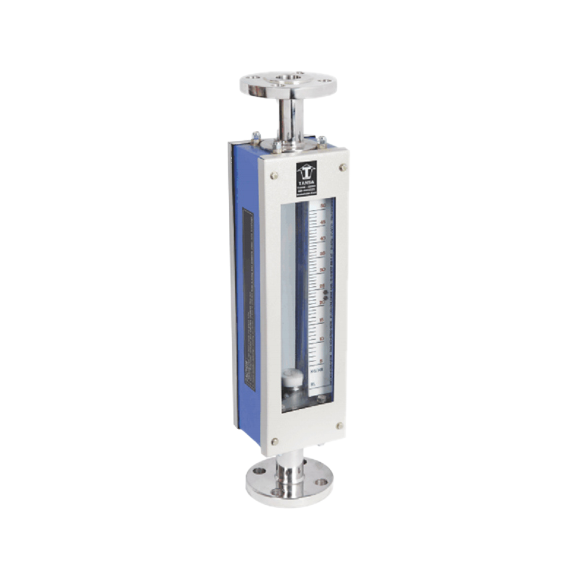
- Description: The tube is made of transparent glass for direct visibility of the float.
- Applications: Used in laboratories and medical equipment for clean and transparent fluids.
- Advantages: Clear visual indication of flow, simple construction.
- Limitations: Fragile and unsuitable for high-pressure applications.
2. Metal Tube Rotameters
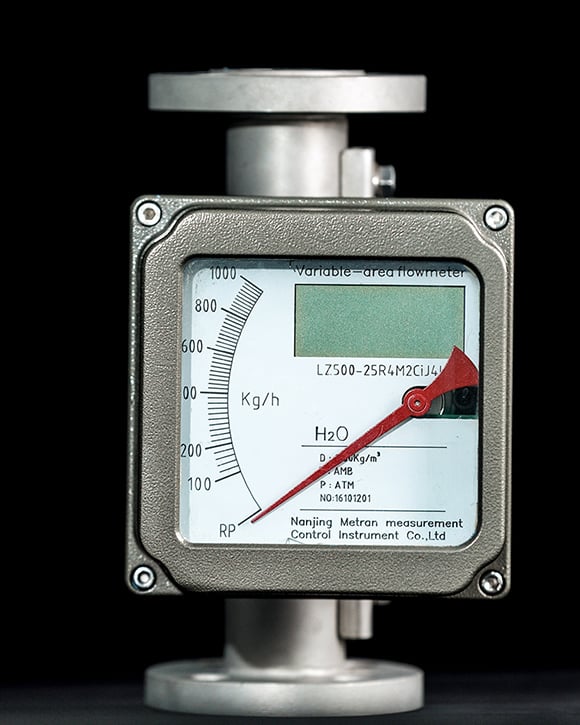
- Description: The tube is made of metal, often with an external magnetic or electronic indicator.
- Applications: Industrial processes with high pressure or opaque fluids.
- Advantages: Durable, pressure-resistant, and suitable for harsh environments.
- Limitations: Less visibility of the float; requires external indicators.
3. Plastic Tube Rotameters
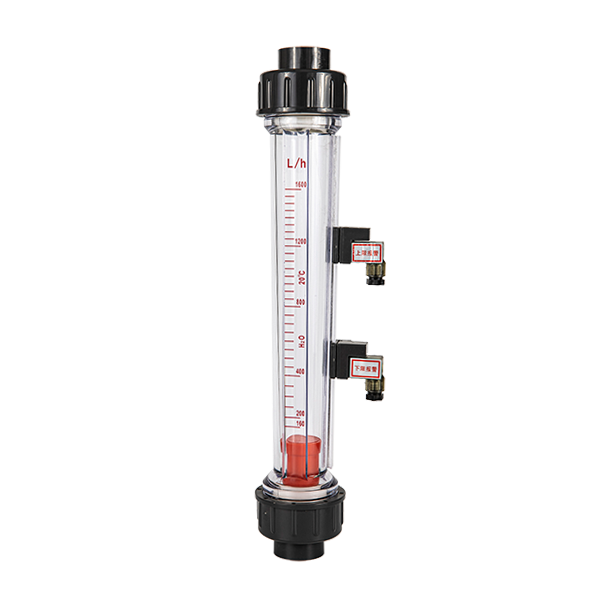
- Description: Made of lightweight and corrosion-resistant plastic.
- Applications: Chemical and water treatment plants where corrosion resistance is critical.
- Advantages: Affordable, lightweight, resistant to corrosive fluids.
- Limitations: Limited pressure and temperature resistance.
4. Armored Rotameters
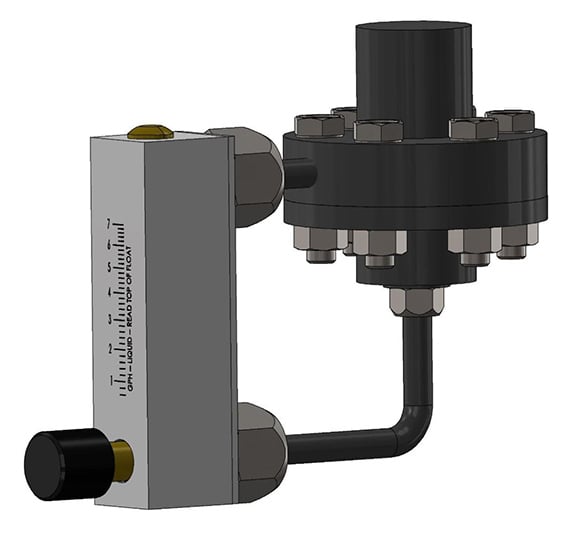
- Description: Designed for extreme conditions with armored protection for the tube.
- Applications: High-pressure and high-temperature industrial settings.
- Advantages: High durability and safety.
- Limitations: Costlier than standard Rotameters.
5. Purge Rotameters
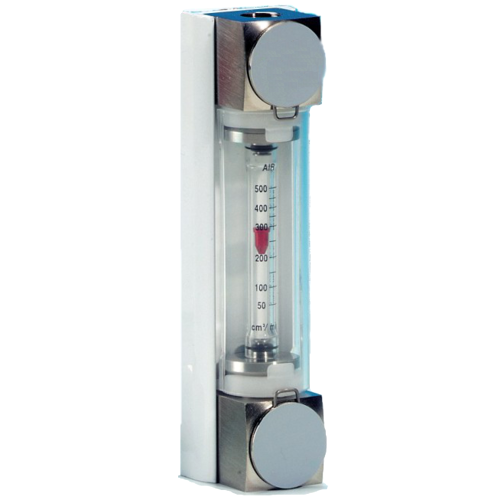
- Description: Small-scale Rotameters designed for low flow rates.
- Applications: Gas flow measurement in analytical instruments.
- Advantages: Accurate for very low flow rates.
- Limitations: Limited to low-flow applications.
Advantages of Rotameters
- Simple Design:
- Easy to install, operate, and maintain.
- Requires no external power supply.
- Cost-Effective:
- Economical compared to other flow measurement devices.
- Direct Visual Indication:
- Provides an immediate and intuitive reading of the flow rate.
- Versatile:
- Suitable for a wide range of fluids, including liquids and gases.
- Durability:
- Metal and armored Rotameters are designed to withstand harsh industrial conditions.
Limitations of Rotameters
- Orientation Dependency:
- Must be installed vertically to ensure accurate readings.
- Limited Accuracy:
- Not as precise as advanced electronic flow meters.
- Pressure and Temperature Constraints:
- Glass and plastic Rotameters are unsuitable for high-pressure or high-temperature applications.
- Fragility:
- Glass Rotameters are prone to breakage in industrial environments.
- No Data Logging:
- Rotameters do not offer electronic data output or logging capabilities.
Applications of Rotameters
Rotameters are used in a wide variety of industries and applications due to their versatility and simplicity:
1. Industrial Processes
- Examples: Chemical processing, oil and gas, and water treatment plants.
- Purpose: Measure and monitor fluid flow in pipelines.
2. Medical Equipment
- Examples: Oxygen flow meters in anesthesia machines.
- Purpose: Ensure precise control of medical gases.
3. Laboratories
- Examples: Flow measurement in research and development projects.
- Purpose: Measure flow rates of experimental fluids.
4. HVAC Systems
- Examples: Airflow measurement in heating and cooling systems.
- Purpose: Monitor and control air circulation.
5. Food and Beverage Industry
- Examples: Flow monitoring in beverage production lines.
- Purpose: Ensure consistent ingredient flow rates.
6. Analytical Instruments
- Examples: Gas chromatography and spectroscopy.
- Purpose: Measure low flow rates of carrier gases.
Rotameters remain one of the simplest and most reliable flow measurement devices in use today. Their versatility, ease of use, and cost-effectiveness make them a popular choice across various industries. While they do have limitations—such as sensitivity to orientation and limited accuracy—they are well-suited for applications that require a straightforward and affordable solution.
By understanding their construction, working principles, and applications, you can effectively select the right type of Rotameter for your specific needs. Whether you’re working in an industrial plant, a medical facility, or a laboratory, Rotameters provide a practical solution for measuring fluid flow with minimal complexity.
Leave a comment