Flow meters are essential instruments in various industries, used to measure the flow rate of liquids, gases, or slurries. The flow meter provides critical data that influences the efficiency, safety, and cost-effectiveness of processes in sectors such as oil and gas, water treatment, chemical manufacturing, food and beverage, and more. As industries evolve, the demand for precise and reliable flow measurement has grown, leading to the development of a wide range of flow meter technologies.
There’re more than 50 flow meter types available now and we’ve selected the 9 most commonly used flowmeters, with their principles, advantages and disadvantages. Understanding these aspects is crucial for selecting the most suitable flow meter for a given application, ensuring accurate measurement and optimal performance.
Table of Contents
Magnetic Flow Meters
Working Principle
Magnetic flow meters, also known as mag meters, operate based on Faraday’s Law of Electromagnetic Induction. According to this principle, when a conductive fluid flows through a magnetic field, it generates a voltage proportional to the flow velocity. The magnetic flow meter consists of a non-magnetic flow tube lined with a non-conductive material, with electrodes mounted on the tube walls.
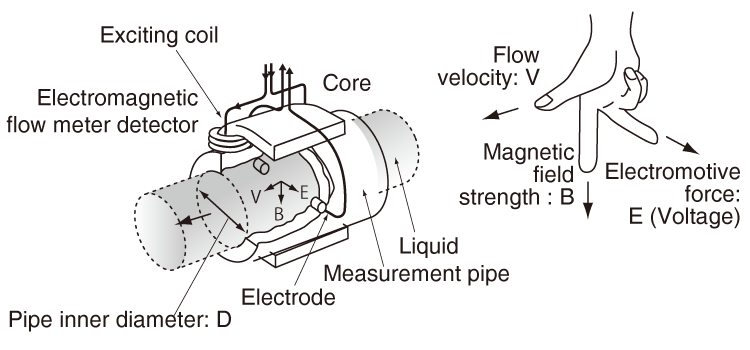
As the fluid flows through the magnetic field created by coils outside the tube, a voltage is induced between the electrodes. This voltage is directly proportional to the flow velocity, allowing the flow rate to be calculated.
Advantages
- Suitable for a variety of fluids: Electromagnetic meter is the best choice for conductive liquids, including liquid-solid two-phase fluids containing solid particles, such as pulp, mud, sewage, etc. Corrosive fluids can be used with the right lining.
- No Moving Parts: The absence of moving parts reduces maintenance needs and increases reliability.
- Wide range of flow rates calibers.
- No Pressure Drop: They do not cause a pressure drop, as there are no obstructions in the flow path.
Disadvantages
- Conductive Fluids Only: Magnetic flow meters only work with conductive fluids, such as water and slurries. Liquids with very low conductivity cannot be measured, such as petroleum and oil. Gas and steam cannot be measured.
- Liquids containing large bubbles cannot be measured.
Applications
Magnetic flow meters are widely used in water and wastewater treatment, chemical processing, food and beverage production, and pulp and paper industries. They are particularly well-suited for measuring the flow of dirty or abrasive fluids.
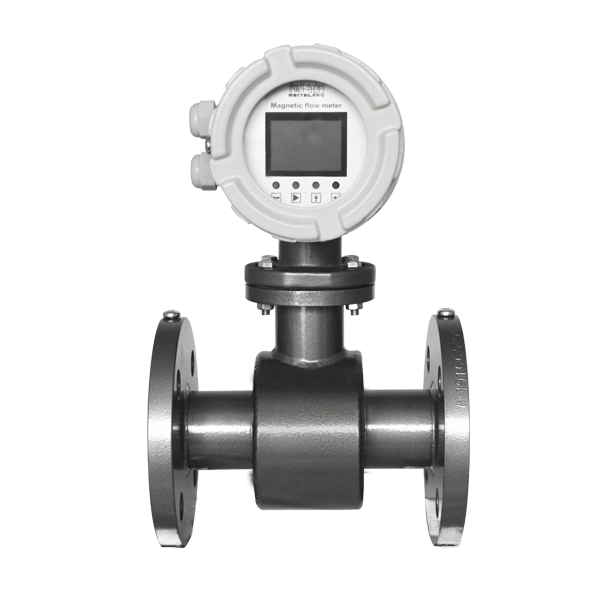
- Nominal Diameter Range: DN 15 to 3000 (½” to 120″)
- Accuracy: Standard: ±0.5 %, Optional: ±0.2 %
- Max. Process Pressure: 100 bar
- Medium Temperature Range: -40 to 356°F (-40 to 180°C)
- No moving parts, no wear, no pressure loss
- Wide range of liners and electrode materials
- Available with compact or remote version of transmitter
- Available with insertion type
Flanged Electromagnetic Flow Meter (MTF-F-100)
Ultrasonic Flow Meters
Working Principle
Ultrasonic flow meters measure the flow rate of a fluid by using ultrasonic beams. There are two main types: transit-time and Doppler flow meter. Transit-time ultrasonic flow meters work by sending ultrasonic pulses in the direction of flow and against it. The time difference between these pulses is used to calculate the flow rate. Doppler ultrasonic flow meters, on the other hand, measure the frequency shift of the ultrasonic signal as it reflects off particles or bubbles in the fluid.
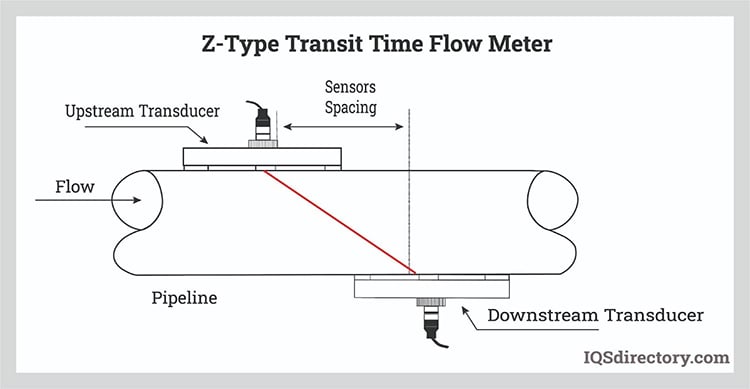
Ultrasonic meters can be either clamp-on or in-line. Clamp-on meters are non-intrusive and are installed outside the pipe, while in-line meters are inserted into the pipe.
Advantages
- Non-intrusive: Clamp-on ultrasonic flow meters do not require cutting the pipe or interrupting the flow, making installation easier and less expensive.
- Versatility: They can measure the flow of both liquids and gases, including liquids containing a certain amount of suspended particles and bubbles.
- Non-conductive liquids: Ultrasonic flow meters can also measure non-conductive fluids (pure water, condensate, hydrocarbons…), which is not possible with an electromagnetic meter.
- No Pressure Drop: Since there are no moving parts or obstructions, ultrasonic meters do not cause a pressure drop.
Disadvantages
- Limitations: They cannot measure liquids containing solid particles and pipes that are only partially filled.
- Dependence on Flow Profile: They require a well-developed flow profile, which may necessitate straight pipe runs before and after the meter.
Applications
Ultrasonic flow meters are good choice for high-pressure, high-flow applications, such as high-pressure natural gas pipelines. They’re widely used in water and wastewater treatment, oil and gas, and chemical processing, and also used in applications where the fluid is non-conductive or where the flow meter needs to be portable or non-intrusive.
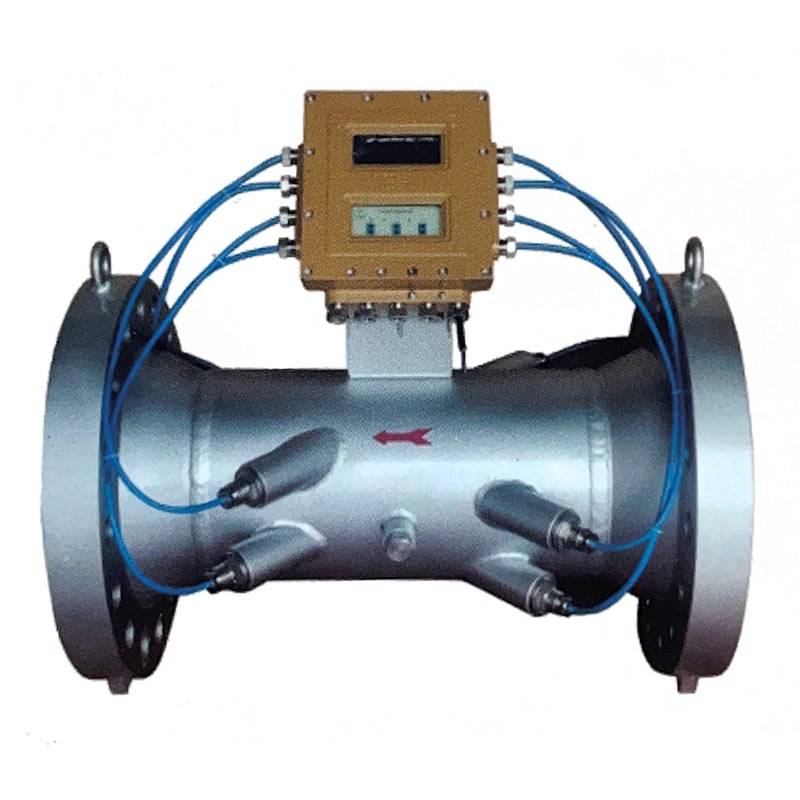
High Precision Ultrasonic Gas Flow Meter
- Nominal Diameter Range: DN 25 to 400 (1″ to 14″)
- Accuracy: ±0.5%; ±1%; ±1.5%
- Max. Process Pressure: 420 bar
- Medium Temperature Range: ≤65 °C (149 °F)
- No moving parts, no presure loss, no line obstructions
- No lubrication or periodic maintenance
- Measurement is not affected by gas properties
- Bi-directional capability
Vortex Flow Meters
Working Principle
Vortex flow meters measure the flow rate by detecting the vortices shed by a bluff body placed in the flow path. According to the Kármán vortex street phenomenon, as fluid flows past the bluff body, it creates alternating vortices downstream. The frequency of these vortices is proportional to the flow velocity.
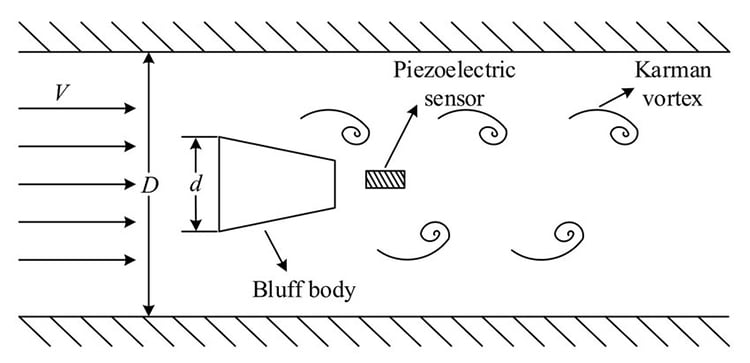
Vortex meters typically use sensors to detect these vortices, converting the frequency into an electrical signal that is used to calculate the flow rate. These meters are particularly effective for measuring the flow of gases and steam.
Advantages
- No Moving Parts: The lack of moving parts reduces maintenance and increases reliability.
- Versatility: Vortex meters can measure liquids, gases, and steam, making them highly versatile.
- Wide temperature and pressure range: Generally, vortex flow meters can adapt to the temperature range from -200°C to +400°C and the pressure range from vacuum to high pressure
Disadvantages
- Sensitivity to Vibration: External vibrations can affect the accuracy of vortex meters.
- Minimum Flow Requirement: They require a minimum flow velocity to generate vortices, which can be a limitation in low-flow applications.
- Not suitable for low Reynolds number medium.
Applications
A vortex flowmeter is ideal for accurately measuring a wide range of liquid media, including water, petroleum, chemical solutions, and more. Additionally, it is highly effective for measuring various gas media, such as air, natural gas, and nitrogen. Furthermore, vortex flowmeters are also well-suited for measuring steam flow, making them versatile instruments for diverse industrial applications.
Turbine Flow Meters
Working Principle
Turbine flow meters measure the flow rate by using a rotor that spins as fluid flows through it. The rotor is mounted on a shaft within the flow meter body, and as the fluid impinges on the rotor blades, it causes the rotor to spin. The rotational speed of the rotor is proportional to the flow velocity. Sensors detect the rotation and convert it into an electrical signal, which is then used to calculate the flow rate.
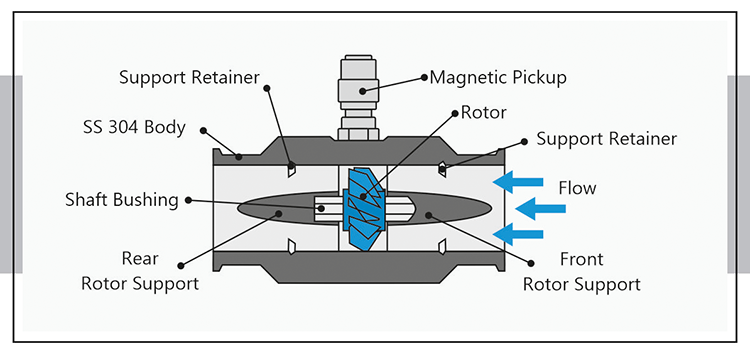
Advantages
- High Accuracy: Turbine meters offer good accuracy and repeatability, particularly for clean, low-viscosity fluids.
- Wide Range of Sizes: They are available in a wide range of sizes, making them suitable for various applications.
- Cost-effective: Turbine meters are generally less expensive than some other high-accuracy flow meters.
Disadvantages
- Sensitivity to Flow Profile: Turbine meters require a well-developed flow profile, necessitating straight pipe runs before and after the meter.
- Mechanical Wear: The moving parts are subject to wear and tear, which can affect long-term accuracy and reliability.
- Limited to Clean Fluids: They are best suited for clean, non-corrosive fluids, as particulates or corrosive substances can damage the rotor.
Applications
Turbine flow meters are commonly used in the oil and gas industry, water treatment, and in the measurement of fuel, chemicals, and pharmaceuticals. They are particularly useful in applications where a combination of accuracy, cost-effectiveness, and reliability is required.
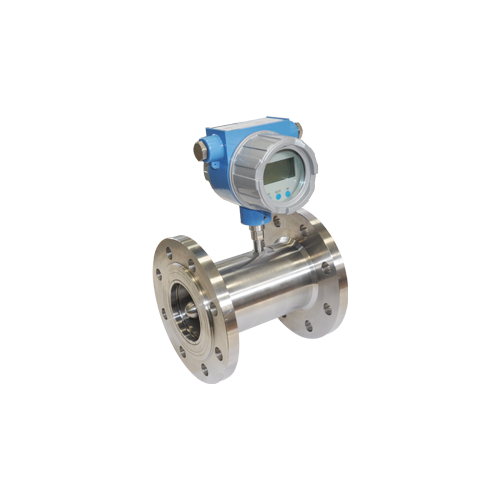
High Accuracy Turbine Flow Meter
- Nominal Diameter Range: DN 0.5 to 300
- Accuracy: ±0.2 %; ±0.5 %
- Max. Process Pressure: 350 bar
- Medium Temperature Range: -196 TO 180 °C (−320.8 to +356 °F)
- 1:20 turndown ratio
- Space-saving structure with DN0.5 minimum bore size
Coriolis Flow Meters
Working Principle
Coriolis flow meters utilize the Coriolis effect, where a moving fluid causes a vibration in the meter’s tube. These vibrations are measured and used to determine the mass flow rate of the fluid. The meter typically consists of one or two tubes that vibrate at their natural frequency. When fluid passes through, the vibration pattern changes due to the Coriolis forces acting on the fluid.
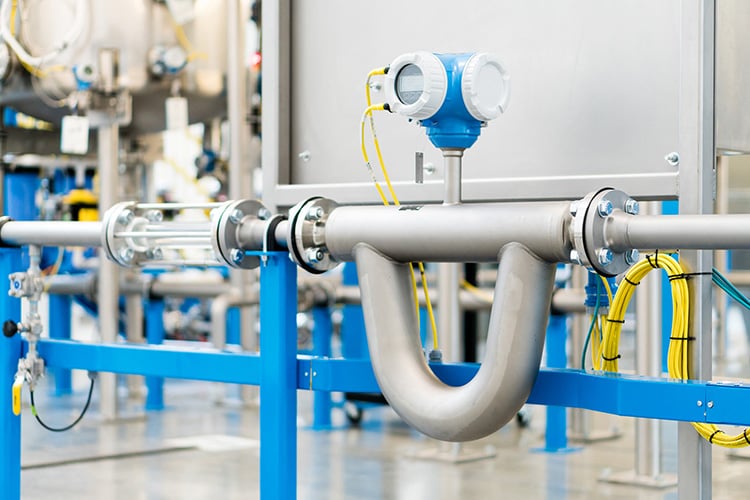
This change in vibration is directly proportional to the mass flow rate. In addition to mass flow, Coriolis meters can also measure the density and temperature of the fluid, providing a comprehensive flow profile.
Advantages
- High Accuracy: Coriolis meters offer exceptional accuracy and are considered one of the most precise flow measurement devices available.
- Versatility: They can measure mass flow, density, and temperature, making them highly versatile.
- A wide range of measurable fluids: Coriolis mass flow meters can measure various liquids including high viscosity liquids, slurries containing solids, liquids containing amounts of gas, and medium and high pressure gases with sufficient density.
- No requirements for straight pipe sections: Coriolis mass flow meter not sensitive to the upstream flow velocity distribution.
- It is insensitive to fluid viscosity, and changes in fluid density.
- Multi-parameter can be measured: For example, it can measure density and temperature, and from these, calculating the concentration of solutes in a solution.
Disadvantages
- High Cost: Coriolis meters are expensive compared to other flow meters, which can be a limiting factor for some applications.
- Complex Installation: They require careful installation to avoid vibrations and other external factors that can affect accuracy.
- Limited pipe diameters: Coriolis flow meter cannot be used for larger pipe diameters, currently limited to less than 200mm.
- Zero-point drift: The instability of the zero point in Coriolis mass flowmeters leads to zero-point drift, impacting the device’s accuracy. Consequently, many instrument models have to separate the total error into two categories: basic error and zero-point instability measurement.
Applications
Coriolis flow meters are used in industries where precise measurement is critical, such as in chemical processing, oil and gas, and food and beverage production. They are particularly useful for measuring the flow of high-viscosity fluids, slurries, and corrosive liquids.
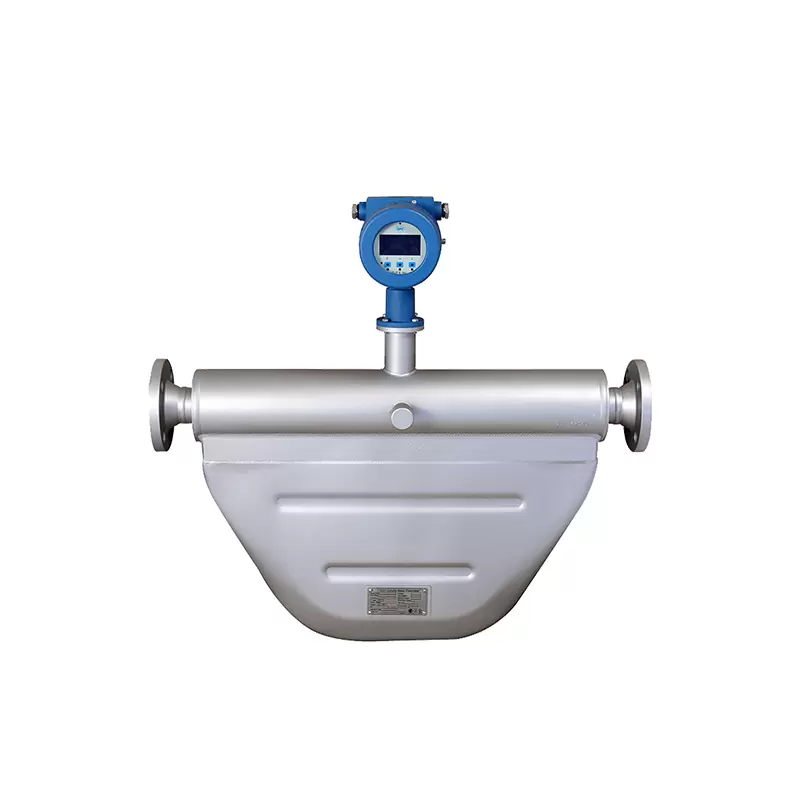
- Nominal Diameter Range: DN 8 to 250 (5/16″ to 10″)
- Accuracy: ±0.1 %; ±0.15 %; ±0.2 %; ±0.5 %
- Max. Process Pressure: 250 bar
- Medium Temperature Range: (-200~+350)℃
- Good zero-stability and anti-interference performance
- No moving parts, no maintenance required
Thermal Mass Flow Meters
Working Principle
Thermal mass flow meters measure the flow rate based on the principle of heat transfer. The meter typically consists of a heated element and temperature sensors placed in the flow stream. As fluid flows past the heated element, it absorbs heat, causing a change in temperature. This temperature difference is measured by the sensors and is proportional to the mass flow rate of the fluid.
There are two main types of thermal mass flow meters: capillary and immersible. Capillary thermal mass meters are used for low-flow applications, while immersible types are used for larger flow rates.
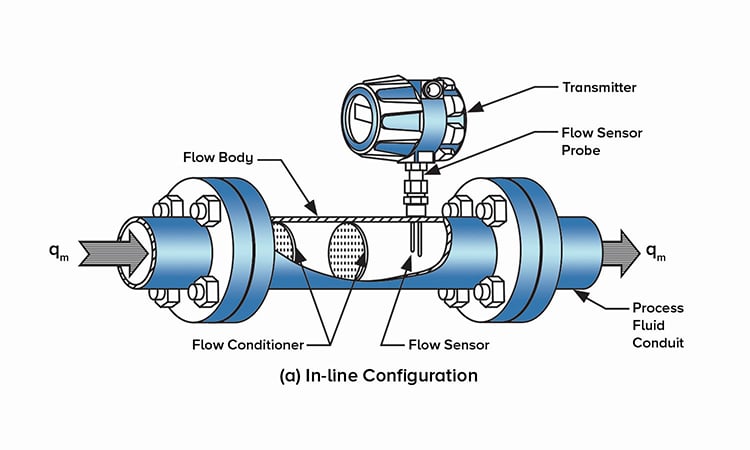
Advantages
- Direct Mass Flow Measurement: Thermal mass meters measure mass flow directly, eliminating the need for pressure and temperature compensation.
- No Moving Parts: The absence of moving parts reduces maintenance needs and improves reliability.
- Wide Range of Applications: They can measure the flow of gases and low-viscosity liquids, making them versatile.
Disadvantages
- Sensitive to Fluid Composition: Changes in fluid composition, such as humidity or gas mix, can affect accuracy.
- Limited to Clean Fluids: They are best suited for clean gases and liquids, as particulates can interfere with heat transfer.
- Installation Considerations: Proper installation is critical, as misalignment or improper placement can lead to inaccurate readings.
- The gas should be dry and free from contaminants: High humidity can alter the heat exchange on the sensor surface, leading to inaccurate output results. Additionally, particulate matter can negatively impact sensor performance.
- Not recommended for high viscosity gases: High viscosity gases may compromise the thermal gas mass flow meter’s performance, as the gas’s heat transfer properties are altered.
Applications
Thermal mass flow meters are widely used in applications where direct mass flow measurement is required, such as in the semiconductor, pharmaceutical, and HVAC industries. They are particularly useful for measuring the flow of air, natural gas, and other gases.
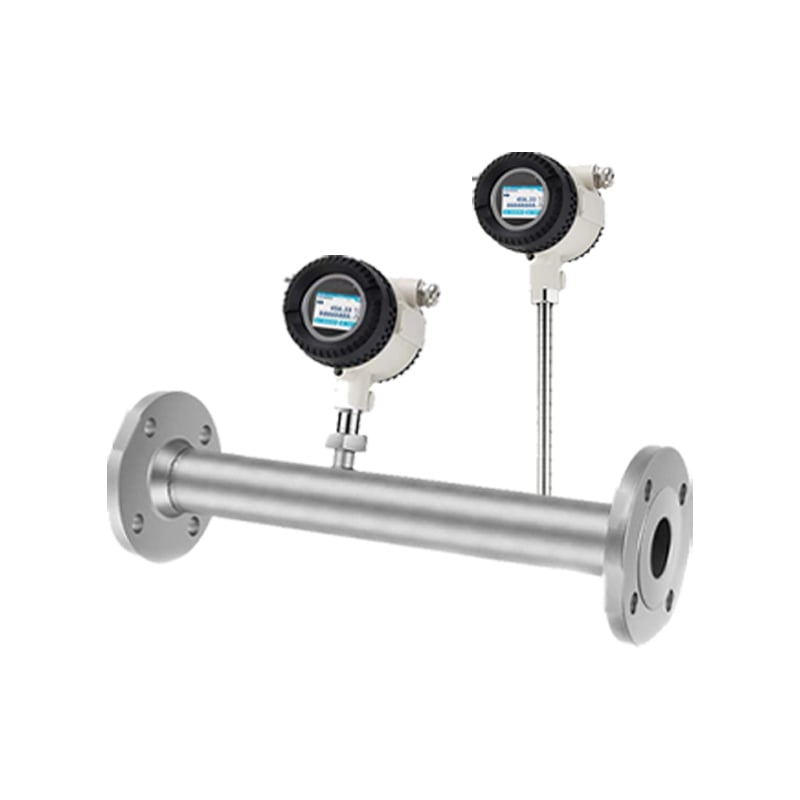
Explosion-proof Thermal Mass Flow Meters
- Nominal Diameter Range: DN 20 to 300 (3/4″ to 12″)
- Accuracy: Standard: ±(1.5% RD + 0.3% FS) , Optional: ±1% RD
- Max. Process Pressure: 63 bar
- Medium Temperature Range: -40 to 176°F (-40 to 80°C)
- Explosion-proof class: Ex db IIC T6 Gb / Ex tb IIIC T80°CDb.
- Ultra-wide 1:2500 turndown ratio, the measuring range is from 0.1 Nm/s to 250 Nm/s
- Full-digital signal processing, higher accuracy, long-term stability
Variable Area Flow Meters (Rotameters)
Working Principle
Variable area flow meters, commonly known as rotameters, operate based on the principle of a float rising and falling in a tapered tube as the flow rate changes. The float is lifted by the fluid flow, and the height at which the float stabilizes corresponds to a specific flow rate.
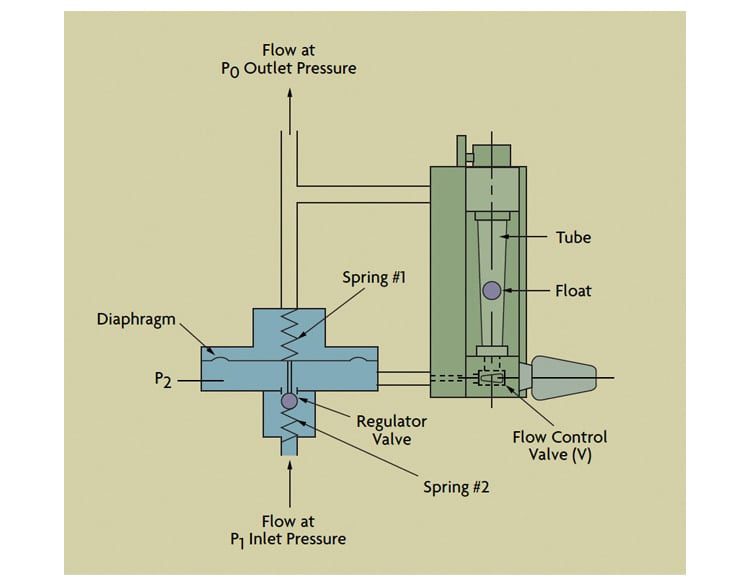
The tapered tube is wider at the top than at the bottom, so as the float rises, the area around it increases, allowing more fluid to pass. The flow rate is read directly from a scale on the tube, making rotameters simple and easy to use.
Advantages
- Simplicity: Rotameters are simple to install, operate, and maintain.
- No External Power Required: They operate purely on the mechanical movement of the float, requiring no external power source.
- Visual Indication: The flow rate can be easily read directly from the meter, providing a clear visual indication.
Disadvantages
- Limited Accuracy: Rotameters are less accurate than some other types of flow meters, particularly at low flow rates.
- Dependence on Fluid Properties: The accuracy can be affected by changes in fluid density, viscosity, and temperature.
- Pressure Drop: The float creates a pressure drop in the system, which can be significant in some applications.
Applications
Rotameters are widely used in laboratories, pilot plants, and in applications where a simple, visual indication of flow rate is sufficient. They are also used in water treatment, chemical dosing, and gas flow measurement.
Differential Pressure Flow Meters
Working Principle
Differential pressure (DP) flow meters operate based on Bernoulli’s principle, which states that the pressure drop across an obstruction in a flowing fluid is proportional to the flow rate. These meters typically consist of a primary element (such as an orifice plate, Venturi tube, or flow nozzle) and a secondary element (a differential pressure transmitter).
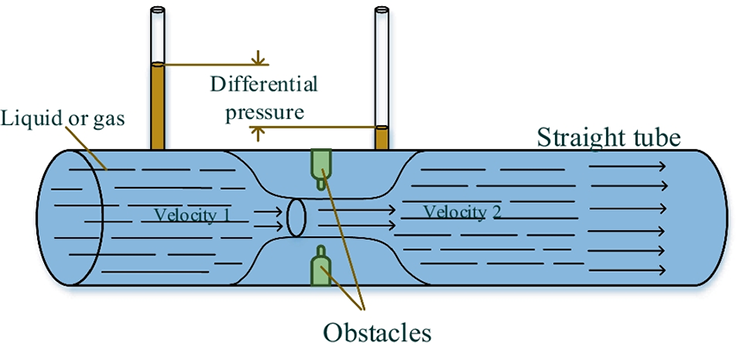
As fluid passes through the primary element, it creates a pressure drop. The secondary element measures this pressure difference, which is then used to calculate the flow rate. The relationship between the pressure drop and flow rate is often nonlinear, requiring the use of square root extraction for accurate flow measurement.
The most commonly used differential pressure flow meters are orifice meters and Venturi meters.
Advantages
- Versatility: DP flow meters can be used for a wide range of fluids, including gases, liquids, and steam, as well as wide pressure and temperature range, and pipe diameters.
- Simplicity: The design is relatively simple and well-understood, making it easy to maintain and troubleshoot.
- Cost-effective: Differential pressure flow meters are generally less expensive than some other types, particularly for large pipe sizes.
Disadvantages
- Pressure Loss: The primary elements create a permanent pressure loss in the system, which can be significant.
- Accuracy: The accuracy can be affected by wear and tear on the primary elements and requires careful calibration.
- Complex Installation: Proper installation is crucial for accurate measurement, and the process can be complex.
Applications
DP flow meters are widely used in industries such as oil and gas, chemical processing, and water treatment. They are suitable for measuring the flow of steam, natural gas, water, and other fluids where robust and versatile measurement is required.
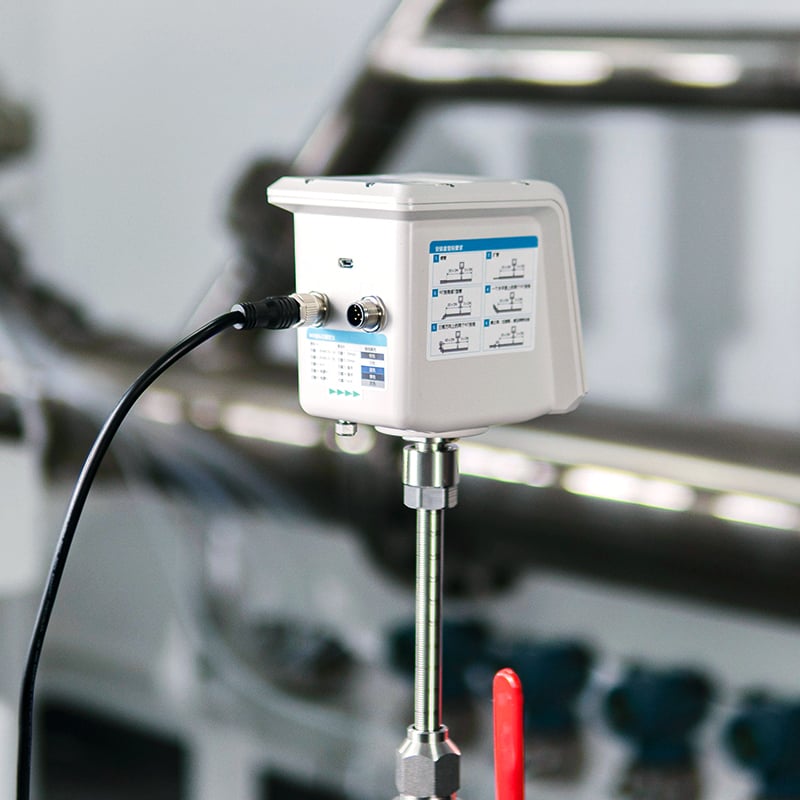
- Nominal Diameter Range: DN 25 to 1000 (1″ – 40″)
- Accuracy: ±1% RD; ±1.5% RD + 0.3% FS
- Max. Process Pressure: 17 bar
- Medium Temperature Range: -40 TO 150 °C (–40 to +302 °F)
- Applicable to the measurement of dirty and wet air
- Online auto-calibration reduces data drift
- high sensitivity, the lower limit is down to 5 Nm/s
- 1:60 wide turndown ratio
- Bidirectional flow measurement
Positive Displacement Flow Meters
Working Principle
Positive displacement (PD) flow meters measure flow by capturing a specific volume of fluid in a chamber and then passing it along. This process involves mechanical components that move or rotate with the fluid, such as gears, discs, or vanes. Each movement or rotation corresponds to a fixed volume of fluid, allowing the meter to measure the total flow directly.
Common types of PD meters include the nutating disc, rotary vane, and oval gear flow meters. The movement of the mechanical parts is often used to drive a counting mechanism, providing a direct reading of the flow rate.
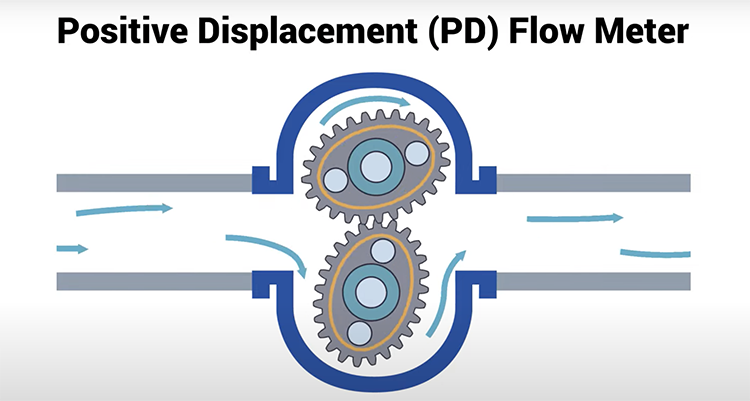
Advantages
- High Accuracy: PD meters are known for their high accuracy, especially at low flow rates.
- No Need for Flow Conditioning: These meters are less affected by flow profile changes and do not require straight pipe runs before or after the meter.
- Direct Measurement: They measure the actual volume passing through, which reduces the need for complex calculations.
Disadvantages
- Mechanical Wear: Moving parts are subject to wear and tear, which can lead to maintenance issues and decreased accuracy over time.
- Limited to Clean Fluids: PD meters are generally used for clean liquids since particulates can cause damage to the mechanical components.
- Pressure Drop: The mechanical nature of these meters can create a pressure drop in the system.
Applications
PD flow meters are commonly used in applications where high accuracy is required, such as in fuel measurement, oil and gas metering, and chemical dosing. They are also widely used in residential water and gas meters.

Bi-rotor Positive Displacement Flow Meter
- Nominal Diameter Range: DN 15 to 400 (½” to 16″)
- Accuracy: Standard: ±0.5 %, Optional: ±0.2 %; ±0.1 %
- Max. Process Pressure: 110 bar
- Medium Temperature Range: (-30~+70) ℃
- Stable in running with low voice
- Good anti-interference performance and long service life
- Strong applicability to viscosity changes
How to Choose Flow Meter Types
When comparing different flow meter types, several factors come into play, including accuracy, cost, maintenance requirements, and suitability for specific applications.
- Accuracy: Coriolis and magnetic flow meters generally offer the highest accuracy, making them suitable for critical applications. Differential pressure and turbine meters also provide good accuracy but may require more maintenance.
- Cost: Positive displacement and turbine meters are often more cost-effective, especially for larger pipe sizes. Ultrasonic and Coriolis meters tend to be more expensive due to their advanced technology.
- Maintenance: Flow meters with no moving parts, such as ultrasonic, Coriolis, and magnetic meters, typically require less maintenance. In contrast, mechanical meters like positive displacement and turbine meters may require more frequent servicing.
- Suitability: The choice of flow meter depends largely on the fluid being measured. For example, magnetic meters are ideal for conductive fluids, while thermal mass meters are best for gases. Vortex meters are suitable for steam and gas, and differential pressure meters are versatile across various fluid types.
Selecting the right flow meter for a specific application is critical for ensuring accurate and reliable flow measurement. Each type of flow meter has its own strengths and weaknesses, making it suitable for particular fluids, flow conditions, and industrial processes. Understanding the working principles, advantages, and disadvantages of each flow meter type helps in making an informed decision that meets the requirements of the application.
By considering factors such as fluid properties, accuracy needs, installation conditions, and budget, you can choose the flow meter that offers the best balance of performance and cost-effectiveness for your specific needs.
Leave a comment