Electromagnetic flow meters are widely used in various industries for accurate flow measurement, but like any technical instrument, they are sensitive to environmental factors. Understanding these factors is crucial for ensuring optimal performance and preventing potential malfunctions. In this blog, we will explore the main environmental factors that can cause electromagnetic flow meter failures, common causes, and practical troubleshooting tips.
Table of Contents
Main Environmental Factors Leading to Electromagnetic Flow Meter Failures
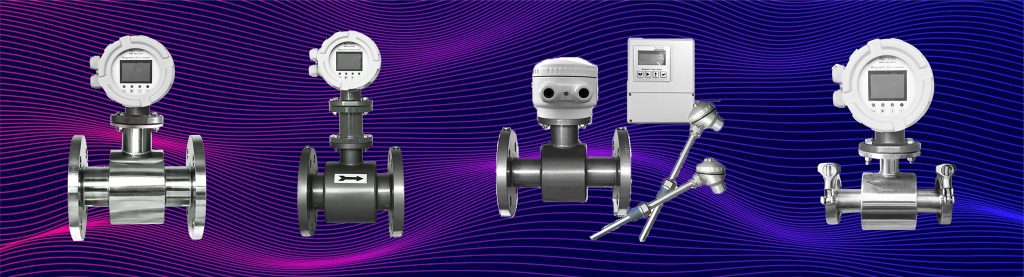
1. Strong Magnetic Fields
The ability of electromagnetic flow meters to resist magnetic fields depends on the structural design of the sensor. For example, if the sensor’s excitation coil housing is made of non-magnetic materials (such as aluminum or plastic), its ability to resist magnetic field interference is weaker. If it is made of steel, it is stronger. In practice, strong magnetic field interference is rare, as installations usually take care to avoid placing the meter near strong magnetic fields.
2. Strong Electromagnetic Waves
Electromagnetic flow meters should comply with electromagnetic compatibility requirements, meaning they should work normally in the specified radiated electromagnetic field environment without causing a deterioration in the instrument’s performance or causing it to malfunction. We have encountered cases of interference from strong radio waves.
Case Study
At a water plant in Fujian, several electromagnetic flow meters were installed, and one of them showed significant output fluctuations. On-site inspection revealed that the installation was in accordance with requirements, with the flow sensor and converter spaced 50 meters apart and connected by a shielded cable inside a metal conduit. The instrument itself was also functioning normally. However, common-mode interference was measured at 1.7V. The initial solution was to electrically insulate the flow sensor, which reduced the common-mode signal to 0.6V, but the output fluctuation did not improve significantly.
Further analysis revealed that a strong radio transmission tower was located very close to the flow meter. To confirm whether the interference source was due to this, the converter was temporarily moved to a position 3 meters away from the flow sensor, and the common-mode interference signal was reduced to less than 0.1mV. While still somewhat high, the instrument's operation became normal. The root cause of the fault was that even with multiple layers of shielded signal cables, electromagnetic waves were still introduced into the instrument.
This example shows that when there is significant common-mode interference near the installation of a split-type electromagnetic flow meter, strong radio waves should be considered as a potential source of interference during fault analysis. This was a rare fault during the commissioning stage.
3. Pipeline Stray Currents
When electromagnetic flow meters are properly grounded, they can avoid most stray currents in the pipeline. However, sometimes even when a thick wire is used to bridge the flow sensor and proper grounding is achieved, stray currents may still affect the flow meter, requiring additional measures.
Case Study 1
At an aluminum smelting plant in Shandong, a DN80 electromagnetic meter was used to measure alkaline slurry. The flow sensor had grounding rings installed at both ends, and the sensor was properly grounded. However, the instrument still did not function correctly until it was moved 2 meters away, and a second grounding point was installed to isolate the stray current.
After the meter had been in operation for some time, output signal fluctuations reappeared. After eliminating the possibility of flow fluctuations and confirming that the meter itself was in good condition, it was initially thought that the meter was malfunctioning. After observing the situation for several days, it was found that the output fluctuations only occurred during the day shift. This clue led to the discovery that the fault was caused by electric welding performed on the same pipeline, far from the electromagnetic flow sensor.
Case Study 2
At a water utility in Zhejiang, two DN900 electromagnetic flow meters were installed. One operated normally, while the other experienced fluctuations of up to 50% FS every 1-2 hours. The user believed that both meters had similar operating conditions and that the fault was caused by the meter itself. On-site inspections revealed that two 0.5-meter sections of steel pipe, well-grounded and unlined, were installed immediately upstream and downstream of the flow sensor, followed by cement-lined steel pipes. The electrical connections and grounding were all correct, and pipeline flow pulsation was ruled out.
The converter and sensor were about 10 meters apart. Nearby was a three-phase transformer with a rating of several hundred kVA, located 2 meters from the converter and 8 meters from the sensor.
The fault was analyzed with two possibilities: (1) interference from the magnetic field of the high-power transformer, and (2) interference from stray currents in the pipeline. To verify if the problem was due to magnetic field interference, the transformer was turned off, but due to the complexity of shutting down the transformer, a two-step approach was adopted. The first step was to check for stray current interference in the pipeline. Without applying excitation current, the potential between the two electrodes was measured and found to be a distorted AC voltage with a peak-to-peak value of 1V. This confirmed that the meter was affected by stray currents, even though the grounding was in place.
The solution was to electrically isolate the electromagnetic flow sensor, along with the two short steel pipe sections, from the pipeline, ensuring that the flow sensor was at the same electrical potential as the liquid. After this modification, the meter began to operate normally, eliminating the impact of the transformer’s magnetic field. The interference current was measured at 60mAAC, with the current flowing upstream from the flow sensor.
This solution can also be applied to pipelines with cathodic protection currents, serving as a method for eliminating pipeline current interference.
4. Ground Potential Changes
Ground potential changes can affect flow measurements. For example, voltage drops on grounding lines due to other equipment can cause changes in the ground potential of the electromagnetic flow meter, which can interfere with measurements, especially when there is significant common-mode interference.
5. Moisture Ingress
Electromagnetic flow meters used in water supply and drainage industries are often installed in meter pits below ground level, which can be submerged in rainwater that has not been drained or even left submerged for long periods. Even when the enclosure has an IP67 (dust-tight and short-term immersion) or IP68 (dust-tight and continuous immersion) protection rating, moisture can often enter due to improperly sealed terminal box gaskets, improperly installed sealing rings, or mismatched cable outer diameters.
For flow sensors installed on the ground, if the terminal box cover is not sealed correctly, moisture can be drawn in through temperature changes, leading to condensation. If the terminal box cable entry is not properly sealed, water and moisture can easily enter. These kinds of issues are common.
In construction, cables are sometimes accidentally cut and then reconnected using tape. This issue might not cause a fault during the initial operation, but over time, as the tape deteriorates, moisture can be drawn in, reducing the insulation of the cables.
Water and moisture ingress into the terminal box can reduce insulation strength and insulation resistance, causing the flow signal loop to output no flow signal, and the excitation coil loop may experience zero-point drift or instability. In such cases, silicone or other sealing materials can be used to seal the connection points.
Non-air-tight excitation coil protective housings can also draw in moisture due to the breathing effect. If the liquid temperature is lower than room temperature, condensation can form on the outer wall of the measuring tube, and frost can form if the temperature is below 0°C, causing a short circuit in the flow signal loop and rendering it ineffective.
Case Study
At a water plant in Kaifeng, one DN200 electromagnetic flow meter measured water from the Yellow River, while another DN900 meter measured groundwater. Two DN1000 flow meters were connected in parallel to measure the finished water. After two years of normal operation, it was discovered that the finished water outflow was 10%-15% higher than the inflow. Upon inspection, no abnormalities were observed in the meter's operation. A comparison test was conducted with a portable ultrasonic flow meter, and it was found that the output signal from the two finished water flow meters was higher than expected. When the zero points were checked, they showed significant deviation. Based on experience, it was judged that the fault was likely due to water ingress into the terminal box or moisture affecting the excitation coil, leading to reduced insulation.
After wiping off the moisture and using a hairdryer to dry the terminal box, the ground resistance of the excitation coil loop was restored from 5-6 MW to several tens of MW, and the zero-point deviation returned to normal.
The cause of the fault was that the reduced insulation of the excitation coil loop created a large insulation resistance and signal internal resistance, which caused significant common-mode interference. The converter’s front-end amplifier was unable to suppress this, which led to a shift in the converter’s zero point.
Conclusion
Electromagnetic flow meters, while highly reliable in a variety of industrial applications, can be susceptible to environmental factors that affect their performance. Key issues such as strong magnetic fields, electromagnetic interference, pipeline stray currents, ground potential changes, and moisture ingress can lead to malfunction or inaccurate measurements if not properly managed.
Effective installation practices, such as ensuring proper grounding, using shielding for electromagnetic waves, and sealing connectors against moisture, are critical to maintaining the meter’s accuracy and longevity. By understanding and mitigating these environmental influences, users can significantly reduce the likelihood of operational failures and ensure consistent, reliable flow measurements in challenging conditions.
Leave a comment