Flow meters are critical instruments in industrial automation and process control, used for measuring the flow of liquids, gases, and steam. Among the many types available, vortex flow meters and turbine flow meters are two of the most widely used.
Although both rely on principles of fluid dynamics, their working principles, suitable applications, accuracy, and maintenance needs differ significantly.
In this article, we’ll compare vortex vs. turbine flow meters in detail to help you choose the right technology for your specific flow measurement needs.
What is a Vortex Flow Meter?
A vortex flow meter operates based on the vortex shedding principle. As a fluid passes a bluff body inside the flow meter, it creates alternating vortices downstream. The frequency of these vortices is directly proportional to the flow velocity.
Vortex Flow Meter Equation
f = K × v
- f = vortex frequency
- v = flow velocity
- K = calibration constant
This frequency is detected by sensors and converted into flow rate data.
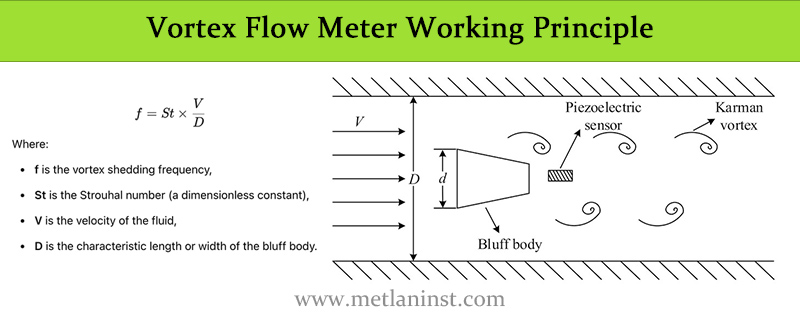
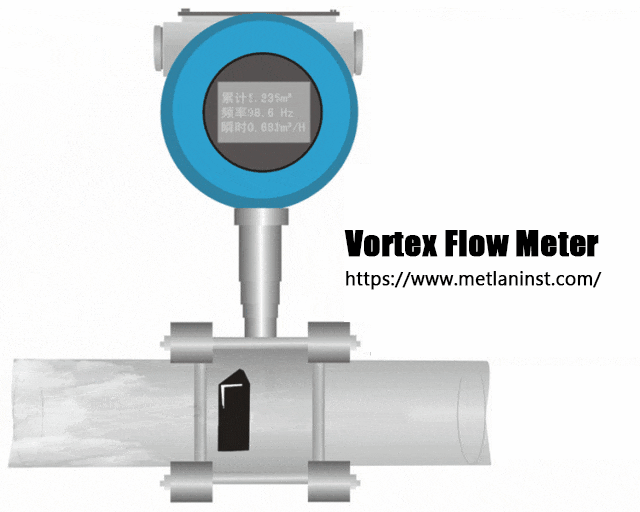
What is a Turbine Flow Meter?
A turbine flow meter uses a spinning rotor placed in the flow stream. The fluid forces the turbine to rotate, and the rotation speed corresponds to the fluid velocity. The number of rotations is measured to calculate the flow rate.
Turbine Flow Meter Equation
Q = K × N
- Q = flow rate
- N = turbine rotor speed
- K = calibration constant
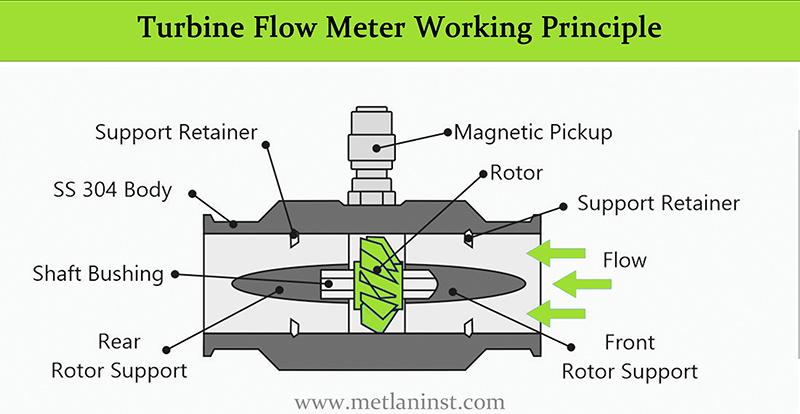
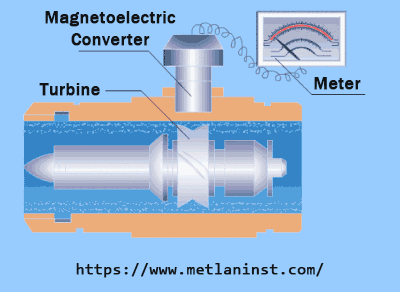
Key Differences Between Vortex and Turbine Flow Meters
1. Measurement Principle
- Vortex: Based on vortex shedding frequency.
- Turbine: Based on rotor spin speed driven by fluid flow.
2. Suitable Fluids
- Vortex flow meters: Ideal for liquids, gases, and steam, including high-temperature, high-pressure media. Also tolerates some suspended solids or impurities.
- Turbine flow meters: Best for clean, low-viscosity liquids such as water, fuel, and light oils. Not suitable for dirty or mixed-phase fluids.
3. Accuracy and Response Time
- Vortex meters offer consistent performance for gases and steam. Calibration may be needed in vibration-prone environments.
- Turbine meters provide high accuracy and fast response, but are sensitive to fluid viscosity, temperature, and pressure changes.
4. Installation & Maintenance
- Vortex meters are easy to install and maintain due to no moving parts. Low wear and long service life.
- Turbine meters require more careful installation and regular maintenance due to moving parts (turbine rotor). Clean fluids are essential.
5. Cost and Use Cases
- Vortex flow meters cost more initially but provide longer life and broader application. Common in power plants, steam pipelines, HVAC, and chemical plants.
- Turbine flow meters are more affordable, ideal for petroleum, pharmaceutical, and food & beverage industries where clean fluids are standard.
Conclusion
Both vortex flow meters and turbine flow meters play important roles in flow measurement systems. Your choice depends on:
- The type of medium
- Required accuracy
- Maintenance capabilities
- Budget and installation conditions
By understanding the differences between vortex and turbine flow meters, you can make the best choice for your industrial application, improving accuracy, reliability, and efficiency.