In the realm of industrial automation and process control, accurate gas flow measurement is critical for efficiency, safety, and regulatory compliance. Among the advanced technologies available, ultrasonic gas flow meters have emerged as a game-changer, offering non-invasive, high-precision solutions for diverse industries. These meters leverage sound waves to measure flow rates, making them ideal for applications where traditional mechanical meters fall short.
Table of Contents
What is an Ultrasonic Gas Flow Meter?
An ultrasonic gas flow meter is a device that measures the flow rate of gases using ultrasonic waves. Unlike mechanical flow meters (e.g., turbine or diaphragm meters), ultrasonic meters have no moving parts, reducing wear and maintenance. They operate by transmitting ultrasonic pulses through the gas stream and analyzing how the flow affects these pulses.
How Do Ultrasonic Gas Flow Meters Work?
There are two primary methods used in ultrasonic flow measurement:
- Transit-Time (Time-of-Flight) Method:
- Two ultrasonic sensors are mounted on opposite sides of the pipe.
- Pulses are sent both with and against the gas flow.
- The difference in transit time between the two directions is proportional to the flow velocity.
- Doppler Effect Method:
- Ultrasonic waves are reflected off particles or bubbles in the gas.
- The frequency shift (Doppler effect) caused by moving particles is used to calculate flow velocity.
Note: Transit-time meters are more common for clean gases, while Doppler meters suit gases with particulates.
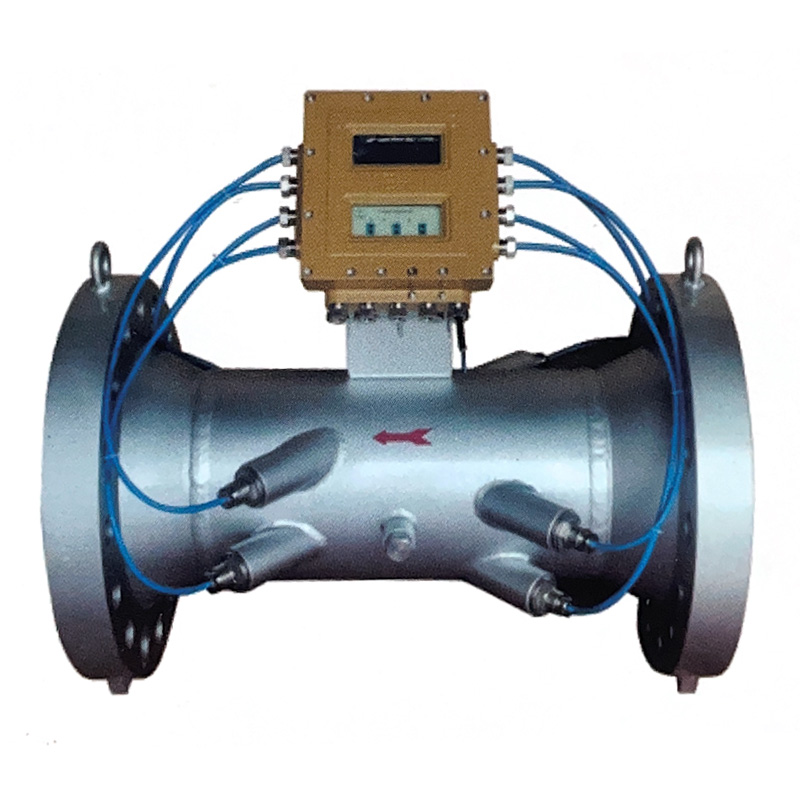
Features:
- High accuracy for gas up to ±0.5%
- No moving parts, no presure loss, no line obstructions
- No lubrication or periodic maintenance
- Measurement is not affected by gas properties
- Wide turndown ratio
- Bi-directional capability
Advantages of Ultrasonic Gas Flow Meters
Ultrasonic gas flow meters offer unique benefits that make them a preferred choice in many scenarios:
- Non-Intrusive Design:
- Clamp-on models can be installed externally without cutting pipes, minimizing downtime.
- Inline models have no obstructions, ensuring zero pressure drop.
- High Accuracy and Repeatability:
- Modern ultrasonic meters achieve accuracies of ±1% or better, ideal for custody transfer and billing.
- Bidirectional Flow Measurement:
- Capable of measuring flow in both directions, useful in complex pipeline systems.
- Wide Turndown Ratio:
- Accurately measure flow rates from very low to high velocities (e.g., 100:1 turndown).
- Low Maintenance:
- No moving parts reduce wear and calibration needs.
- Compatibility with Large Pipes:
- Suitable for pipes ranging from 2 cm to several meters in diameter.
- Resistance to Harsh Conditions:
- Perform well in extreme temperatures, pressures, and corrosive environments (with proper sensor materials).
Limitations of Ultrasonic Gas Flow Meters
Despite their strengths, ultrasonic flow meters have limitations:
- Sensitivity to Gas Composition:
- Requires a consistent gas composition for accurate readings.
- Performance degrades with entrained liquids, heavy particulates, or foam.
- Temperature and Pressure Dependencies:
- Extreme variations may require compensation algorithms.
- Higher Initial Cost:
- More expensive than basic mechanical meters, though offset by long-term savings.
- Limited Effectiveness in Small Pipes:
- Clamp-on models struggle with pipes under 2 cm diameter due to signal attenuation.
- Calibration Requirements:
- May need periodic recalibration, especially for mixed gases.
Which Gases Are Best Suited for Ultrasonic Gas Flow Meters?
Ultrasonic meters excel with gases that meet specific criteria:
Ideal Gases
- Clean, Dry Gases:
- Natural gas, compressed air, nitrogen, oxygen, argon.
- Minimal particulates or moisture ensure reliable transit-time measurements.
- Corrosive Gases:
- Chlorine, ammonia, or hydrogen sulfide (with corrosion-resistant sensors).
- High-Purity Gases:
- Used in semiconductor manufacturing or pharmaceuticals.
- Biogas and Flue Gases:
- Methane, CO₂, and other combustion byproducts (Doppler method for particulates).
Unsuitable Gases
- Heavily Contaminated Gases: Excessive dust, droplets, or bubbles disrupt ultrasonic signals.
- Non-Homogeneous Mixtures: Inconsistent density or acoustic properties cause errors.
Applications and Industries for Ultrasonic Gas Flow Meters
Ultrasonic gas flow meters are versatile tools across industries requiring precise gas monitoring:
1. Oil & Gas
- Custody Transfer: Accurate billing for natural gas pipelines.
- Emission Monitoring: Tracking methane leaks or flare gas.
2. HVAC and Energy Management
- Compressed Air Systems: Optimizing energy use in manufacturing.
- Combustion Control: Regulating air-to-fuel ratios in boilers.
3. Wastewater Treatment
- Biogas Measurement: Monitoring methane production in digesters.
4. Chemical and Petrochemical
- Process Gas Control: Ensuring precise dosing of reactive gases.
5. Power Generation
- Flue Gas Analysis: Measuring CO₂ and SO₂ emissions.
6. Pharmaceutical and Food Industries
- Sterile Gas Supply: Controlling nitrogen or CO₂ in packaging lines.
7. Environmental Monitoring
- Stack Testing: Compliance with air quality regulations.
How to Choose the Right Ultrasonic Gas Flow Meter
Selecting the best meter involves evaluating:
- Gas Properties: Cleanliness, humidity, and corrosiveness.
- Pipe Size and Material: Clamp-on vs. inline installation.
- Accuracy Needs: Custody transfer vs. general monitoring.
- Environmental Conditions: Temperature, pressure, and hazardous area certifications (e.g., ATEX).
- Budget: Balancing upfront costs with long-term savings.
Ultrasonic gas flow meters are revolutionizing gas measurement with their non-invasive design, high accuracy, and adaptability. While they may not suit every application (e.g., heavily contaminated gases), their advantages in clean, high-precision environments make them indispensable for industries like oil and gas, HVAC, and environmental monitoring.