What is Oil Flow Meters?
Oil flow meters are devices used to measure the flow rate of oil within a pipe or other conduit, often in industrial applications. It helps determine the volumetric flow or mass flow of oil, providing critical data to ensure the smooth operation of various processes, such as oil refining, fuel distribution, hydraulic systems, and lubrication systems.
Oil flow meters are designed to handle different oil types, ranging from low-viscosity oils like diesel or gasoline to high-viscosity oils like heavy fuel oil or lubricants. The accurate measurement of oil flow is crucial in industries such as oil and gas, energy, chemical processing, and automotive sectors, where flow data is essential for process control, inventory management, billing, and regulatory compliance.
If you’re also interested in the flow meters for air, please check blog post Guide to Choose the Right Air Flow Meters
Table of Contents
Factors to Consider When Choosing Oil Flow Meters
When selecting oil flow meters, it’s crucial to assess several factors. These will ensure you choose the most suitable meter for your specific industrial application:
1. Viscosity of the Oil
Oil comes in various viscosities, from light crude oil to heavy fuel oil. Some flow meters are better suited for low-viscosity oils, while others are designed to handle high-viscosity fluids. Understanding the oil’s viscosity range is essential for choosing a flow meter that will provide accurate readings.
2. Flow Rate Range
Flow rate can vary significantly depending on the type of oil being measured and the application. Some meters perform better at high flow rates, while others are optimized for lower flow rates. Accurately determining the expected flow rate is essential for ensuring the meter works effectively within its operating range.
3. Pressure and Temperature
In industrial settings, oil is often subject to high pressures and temperatures. Flow meters need to be able to withstand these conditions without compromising accuracy or longevity. Ensure the meter you select is compatible with the temperature and pressure levels of your process.
4. Accuracy and Calibration
Depending on the application, the required level of accuracy may vary. For example, fiscal metering for oil trading requires highly accurate meters, while general process monitoring may allow for more flexibility. Consider the accuracy ratings of each meter and any required calibration procedures to maintain long-term reliability.
5. Maintenance and Durability
Some flow meters are more prone to wear and tear, especially when measuring oils with high viscosity or in challenging environments. It’s important to consider the maintenance requirements and long-term durability of the flow meter, particularly in industrial settings where downtime can be costly.
6. Installation Requirements
The installation environment can also dictate the type of meter you choose. Some flow meters require in-line installation with straight pipe runs to ensure accurate measurement, while others, like ultrasonic meters, offer non-intrusive installation options. Make sure the meter fits into your system’s layout with minimal disruption.
7. Budget
Flow meters can vary greatly in price, depending on their accuracy, technology, and durability. Higher-end meters typically offer more features and better long-term performance, but they come with a higher upfront cost. Consider the total cost of ownership, including maintenance, calibration, and lifespan.
Recommended Types of Oil Flow Meters
Now that we’ve covered the key factors to consider, let’s dive into the most commonly recommended flow meter types for measuring oil. Each of these types has distinct advantages and disadvantages depending on the specific industrial application.
Flow Meter Types | Best for | Pros. | Cons. |
Positive Displacement Flow Meters | High-viscosity oils, accurate measurement at low flow rates | 1. Highly accurate, especially for high-viscosity oils and low flow rates. 2. Insensitive to changes in fluid properties, such as viscosity or temperature, as long as the flow rate is steady. 3. Can handle thick oils effectively without sacrificing accuracy. | 1. Mechanical components require regular maintenance due to wear and tear. 2. Not suitable for high flow rates in large pipelines. 3. Can be sensitive to particulates in the oil, which may cause clogging or damage the internal components. |
Coriolis Flow Meters | High-precision measurements, varying flow conditions | 1. Extremely accurate, making it ideal for custody transfer and critical applications. 2. Measures mass flow rate directly, so it is not affected by changes in temperature, pressure, or fluid density. 3. Can handle a wide range of oil viscosities and flow conditions. 4. No moving parts, resulting in lower maintenance and longer lifespan. | 1. Expensive compared to other flow meter types due to advanced technology. 2. Requires special installation conditions to ensure accuracy. 3. Not ideal for high-viscosity oils at very low flow rates. |
Turbine Flow Meters | Low-viscosity oils, high flow rates | 1. Good accuracy for low-viscosity oils and steady flow conditions. 2. Cost-effective compared to more advanced meters like Coriolis or ultrasonic meters. 3. Wide flow range: works well in high-flow applications. | 1. Mechanical components are subject to wear, particularly in high-viscosity or dirty oil environments. 2. Less accurate at very low flow rates or with fluctuating flow. 3. Not suitable for high-viscosity oils, as the rotor may slow down or stop in thick fluids. |
Electromagnetic (Magnetic) Flow Meters | Conductive oils, large pipelines | 1. Highly accurate for conductive liquids, including some oils that have slight conductivity. 2. No moving parts, meaning less maintenance and longer service life. 3. Can handle large pipelines and high flow rates with ease. | Only works with conductive liquids, so it’s not suitable for non-conductive oils like most refined petroleum products. |
Ultrasonic Flow Meters | Clean, non-conductive oils, non-intrusive installations | 1. Non-intrusive installation options, such as clamp-on designs, mean no need to cut pipes or disrupt flow. 2. No moving parts, resulting in low maintenance needs. 3. Suitable for a wide range of pipe sizes and flow rates. | 1. Less accurate with oils containing air bubbles or particulates, as this can disrupt the sound waves. 2. Can be expensive, especially for larger pipe installations. 3. Requires clean oil for optimal performance. |
1. Positive Displacement Flow Meters
How it Works: Positive displacement (PD) flow meters work by trapping a specific volume of fluid between rotating or reciprocating components and then counting the number of times the compartments fill and empty to determine the flow rate.
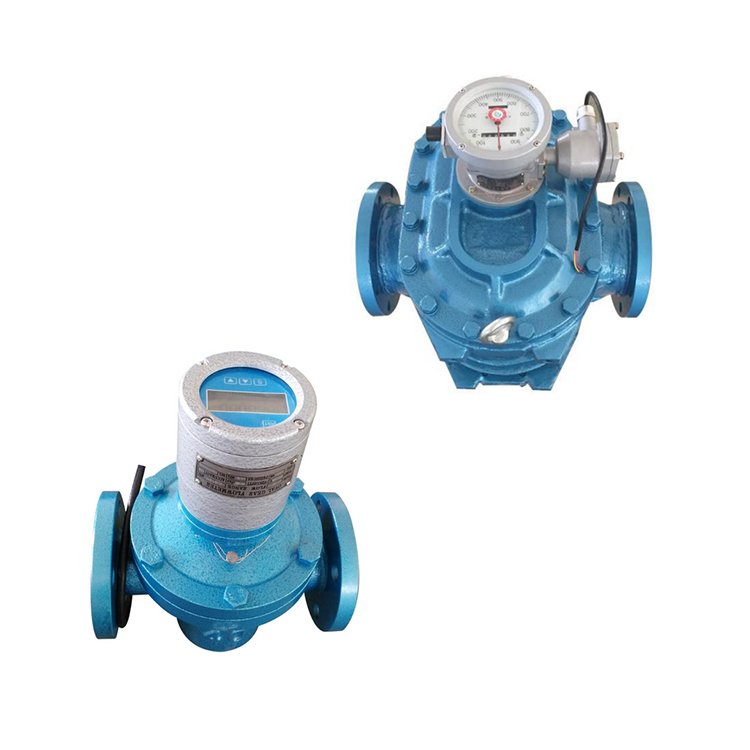
Why Recommended: Positive displacement meters are widely used in the oil industry for their high accuracy and reliability, especially in applications involving high-viscosity oils like lubricants and fuel oils. They are often used in custody transfer and billing applications where precise measurement is essential.
2. Coriolis Flow Meters
How it Works: Coriolis flow meters measure mass flow rate by detecting the Coriolis effect, which occurs when the fluid passes through vibrating tubes. The meter measures the phase shift caused by the fluid’s mass flow rate, providing an accurate and direct measurement.
Why Recommended: Coriolis oil flow meters are recommended for applications where precision is critical, such as in oil refining, process monitoring, and custody transfer. Their ability to measure mass flow directly and accurately makes them a versatile option across a variety of oil types and conditions.
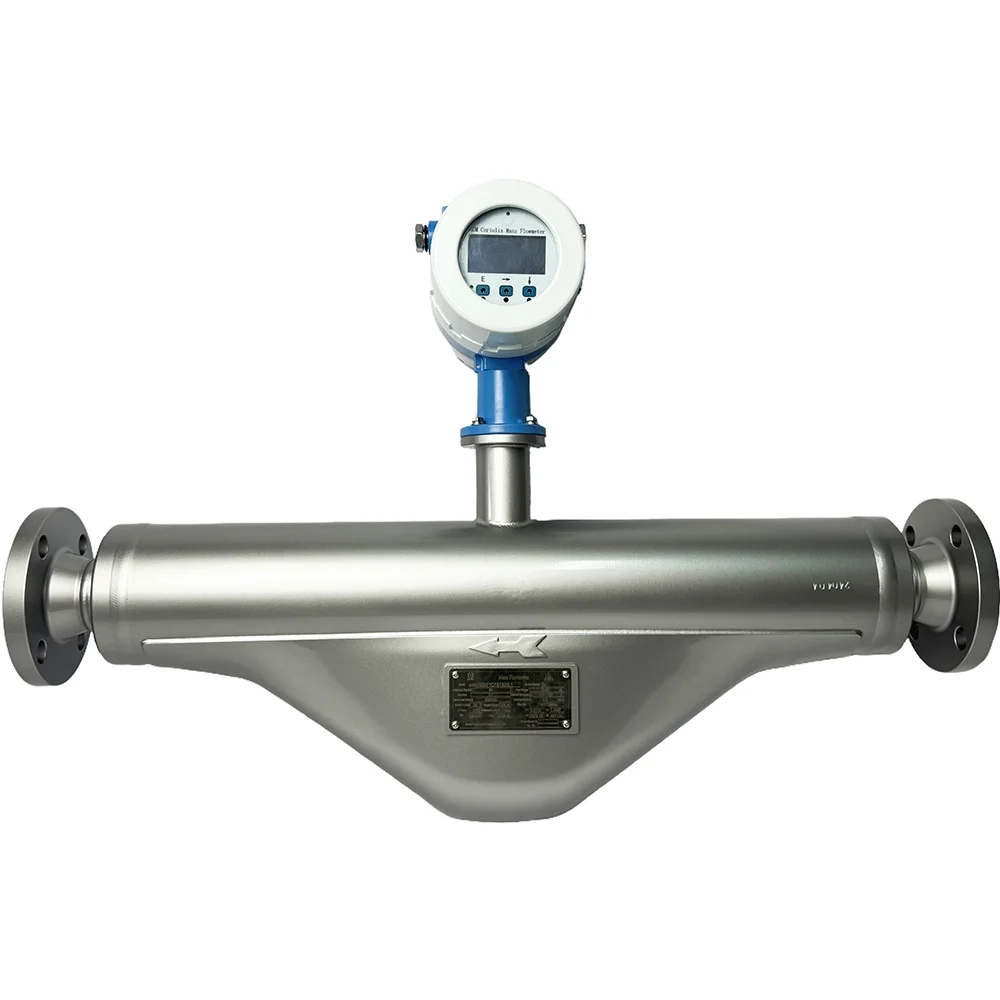
3. Turbine Flow Meters
How it Works: Turbine oil flow meters measure flow by using a rotor that spins in proportion to the velocity of the oil passing through it. The rotation speed is then converted to a flow rate measurement.
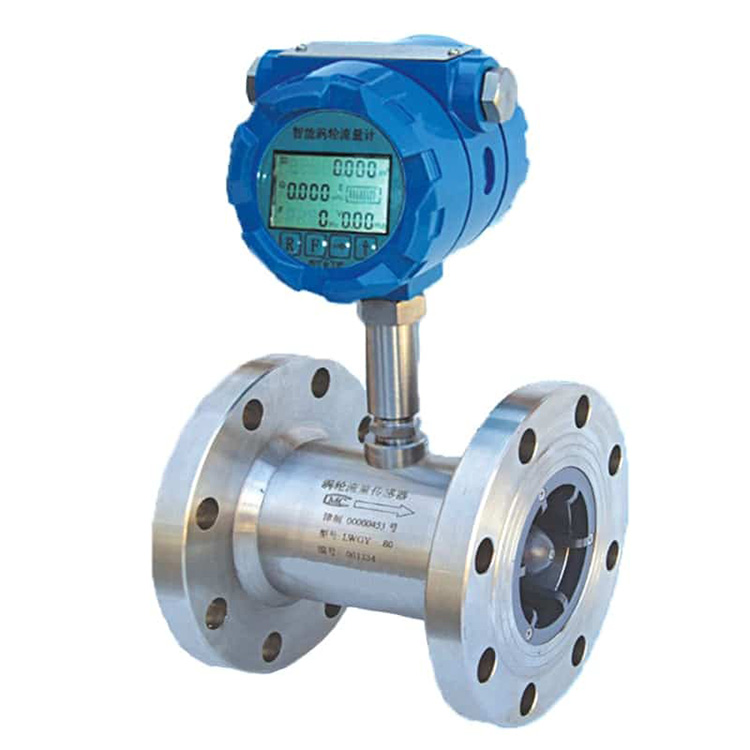
Why Recommended: Turbine flow meters are widely used in industrial applications where low-viscosity oils are measured at high flow rates. Their relatively low cost and good accuracy make them a popular choice for applications like fuel measurement or hydraulic oil monitoring.
4. Electromagnetic (Magnetic) Flow Meters
How it Works: Electromagnetic flow meters (magmeters) work by generating a magnetic field and measuring the voltage created as a conductive fluid passes through it. This voltage is directly proportional to the flow rate.
Why Recommended: Magmeters are ideal for measuring conductive oils in large industrial pipelines, particularly in refining or process industries. Their high accuracy and low maintenance requirements make them a good choice for continuous flow measurement in critical applications.
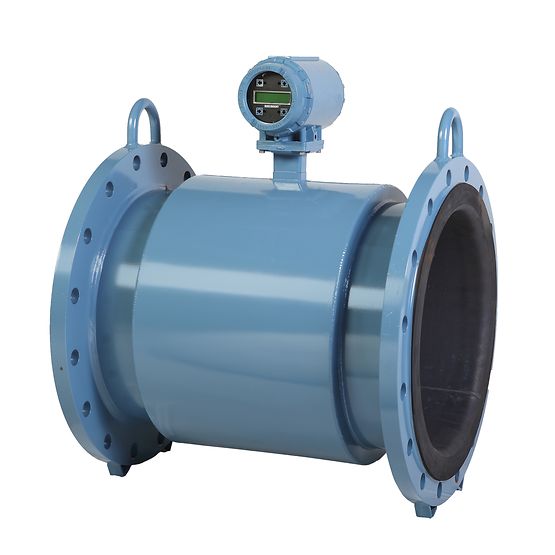
5. Ultrasonic Flow Meters
How it Works: Ultrasonic flow meters use sound waves to measure flow. In a transit-time ultrasonic flow meter, sound waves are sent both upstream and downstream, and the time difference between the two is used to calculate flow rate.
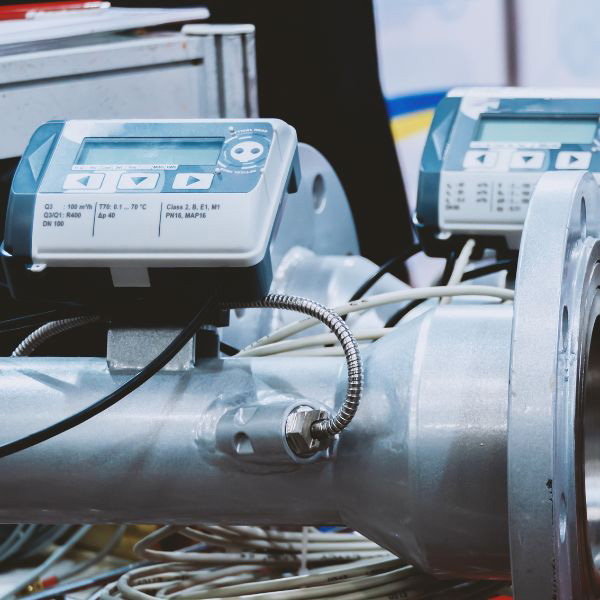
Why Recommended: Ultrasonic flow meters are ideal for non-conductive oils and situations where installation flexibility is important. They’re widely used in oil pipelines where downtime is costly, and non-intrusive measurement is preferred.
Choosing the Right Oil Flow Meter for Your Application
Here’s a quick summary to help you decide which flow meter is best for your specific oil application:
- For high-viscosity oils or low flow rates: Choose positive displacement flow meters for their accuracy and reliability in handling thick oils.
- For high-precision applications: Use Coriolis flow meters, especially when mass flow measurement and varying conditions are important.
- For low-viscosity oils at high flow rates: Turbine flow meters are a cost-effective and accurate solution.
- For conductive oils in large pipelines: Magnetic flow meters provide high accuracy with minimal maintenance.
- For non-intrusive measurements of clean oils: Ultrasonic flow meters are ideal, especially for large pipelines or systems where installation flexibility is needed.
Selecting the right industrial oil flow meter involves understanding your specific application’s needs, including viscosity, flow rate, accuracy requirements, and installation conditions. Each type of flow meter—whether it’s a positive displacement, Coriolis, turbine, magnetic, or ultrasonic meter—has distinct advantages and drawbacks. By carefully considering these factors, you can ensure that your chosen flow meter will provide accurate measurements, improve process efficiency, and reduce long-term maintenance costs.
Leave a comment