Flow measurement is a crucial aspect of various industrial processes, ensuring accurate control and management of liquids. Among the different types of flow meters available, electromagnetic flow meters, or mag meters, stand out for their precision, reliability, and applicability in diverse settings. Since their invention in the 1950s, electromagnetic flow meters have become an industry standard for measuring the of conductive liquids. This technology’s non-intrusive nature, lack of moving parts, and broad compatibility with various liquid types make it a preferred choice in water treatment, chemical processing, food and beverage, and other industries.
If you’re also interested in vortex flow meter, here is a comprehensive guide for vortex flow meters.
Table of Contents
How Does the Magnetic Flow Meter Work
Working Principles of Electromagnetic Flow Meters
The operational principle of electromagnetic flow meters is rooted in Faraday’s Law of Electromagnetic Induction. The law states that when a conductive material passes through a magnetic field, an electric voltage is induced perpendicular to the field and flow direction. This voltage is directly proportional to the flow velocity of the liquid.
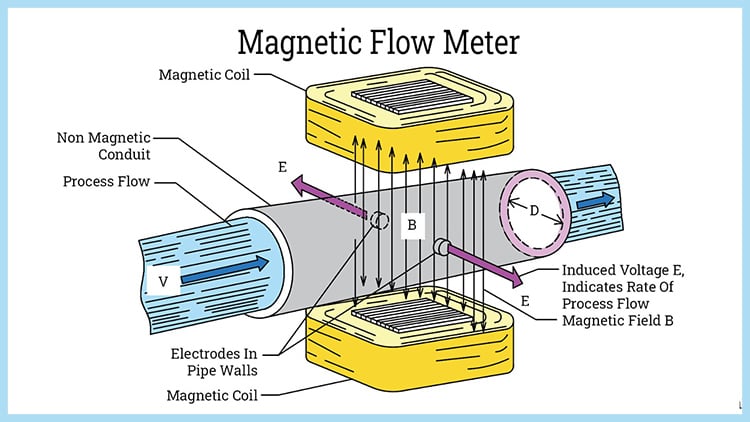
In a typical electromagnetic flow meter setup:
- 1. Structure: The flow meter consists of a non-magnetic, non-conductive pipe section (known as the flow tube), often made of stainless steel or other durable materials, lined with an insulating material like PTFE or rubber. Inside the pipe, there are two electrodes placed diametrically opposite to each other. These electrodes come into contact with the flowing liquid.
- 2. Magnetic Field Generation: Coils surrounding the flow tube generate a magnetic field perpendicular to the flow direction of the fluid. When the conductive liquid moves through this magnetic field, an electromagnetic force (emf) is induced between the electrodes.
- 3. Voltage Measurement: The induced voltage is picked up by the electrodes and sent to a transmitter, which converts this voltage signal into a flow rate using the equation derived from Faraday’s Law: E = k × B × D × V where E is the induced voltage, k is a constant, B is the magnetic field strength, D is the internal diameter of the pipe, and V is the velocity of the liquid. Since B and D are constants for a given flow meter, the voltage E is directly proportional to the fluid velocity V.
- 4. Flow Rate Calculation: The transmitter processes the voltage signal and provides a volumetric flow rate, which is then displayed on a digital interface or integrated into a control system.
- 5. Zero Stability: One of the key features of mag meters is their zero stability. If there is no flow, the induced voltage should ideally be zero. This feature makes mag meters exceptionally accurate, as any voltage signal under no-flow conditions is typically treated as noise and calibrated out.
Benefits of Electromagnetic Flow Meters
- 1. High Accuracy and Precision: Electromagnetic flow meters offer high accuracy levels, often around ±0.2% to ±0.5% of the reading, which can be critical in applications where precise measurements are essential, such as in chemical dosing or pharmaceutical manufacturing.
- 2. No Moving Parts: The absence of moving parts inside the flow tube minimizes the risk of mechanical wear and tear, resulting in lower maintenance costs and enhanced durability. This design also reduces the chances of pressure loss, making them highly efficient.
- 3. Wide Range of Applications: Mag meters are versatile and can be used for various types of conductive fluids, including slurries, dirty water, corrosive chemicals, and viscous fluids. This broad applicability makes them ideal for industries like wastewater treatment, mining, and food and beverage processing.
- 4. Bi-directional Measurement Capability: These meters can measure flow in both directions, which is valuable in applications where the flow direction can change or needs to be monitored from multiple directions.
- 5. Insensitive to Fluid Properties: Magnetic flow meters are unaffected by changes in fluid density, viscosity, temperature, or pressure. This advantage ensures consistent and reliable measurements, even under varying process conditions.
- 6. Easy to Maintain: With no mechanical components and minimal parts that come into contact with the liquid, maintenance is straightforward. Periodic calibration and electrode cleaning are often all that is required to keep mag meters operational.
Disadvantages of Electromagnetic Flow Meters
- 1. Limited to Conductive Fluids: One of the primary limitations of electromagnetic flow meters is their inability to measure the flow of non-conductive fluids, such as oils, hydrocarbons, and gases. The fluid must have a minimum conductivity (typically above 5 µS/cm) for the meter to work correctly.
- 2. Higher Initial Costs: Compared to some other flow measurement technologies, mag meters have higher upfront costs. The need for precise installation and quality materials contributes to this cost, which can be a barrier for smaller operations or applications with tight budgets.
- 3. Installation Requirements and Sensitivity to Surroundings: Magnetic flow meters require careful installation to avoid interference from external electromagnetic fields. Moreover, sufficient straight pipe runs upstream and downstream are necessary to maintain flow profile and measurement accuracy, which can be challenging in space-constrained environments.
- 4. Power Consumption: Electromagnetic meters rely on external power to create the magnetic field and operate the transmitter, which can lead to higher operating costs in some settings, especially where power efficiency is critical.
- 5. Sensitive to Air Bubbles and Conductive Solids: While mag meters handle slurries well, the presence of air bubbles or conductive solids can lead to signal noise and affect measurement accuracy. Therefore, care must be taken to ensure the flow remains free of large air pockets.
Common Types of Electromagnetic Flow Meters
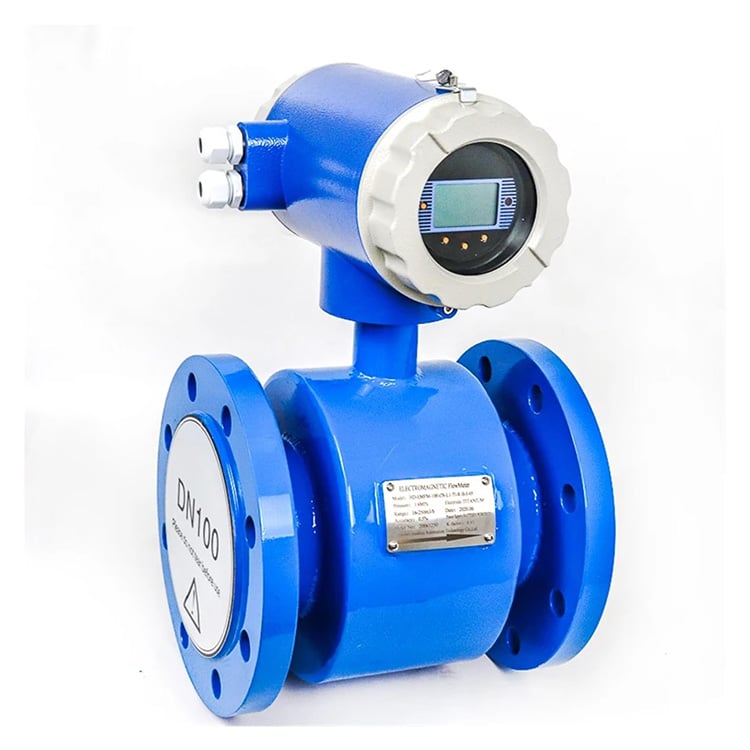
1. In-Line Electromagnetic Flow Meters: These are directly installed into the pipeline and offer the highest accuracy and reliability. They come in various sizes to match different pipe diameters and are commonly used in industries requiring precise flow measurements, such as water treatment plants and chemical processing facilities.
2. Insertion Electromagnetic Flow Meters: Ideal for larger pipes where in-line meters would be prohibitively expensive. Insertion meters have a probe that is inserted into the pipe and measures the flow velocity at a specific point. While they offer slightly lower accuracy than in-line meters, they are more cost-effective for large-diameter pipes and can be installed without shutting down the process.
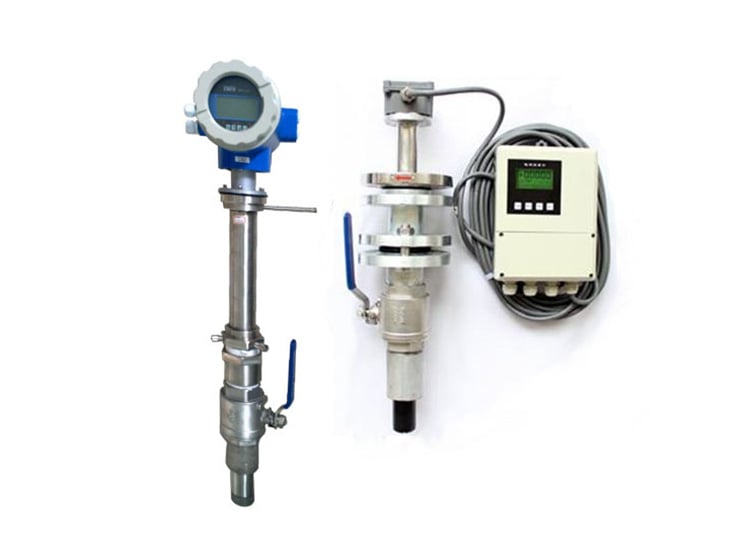
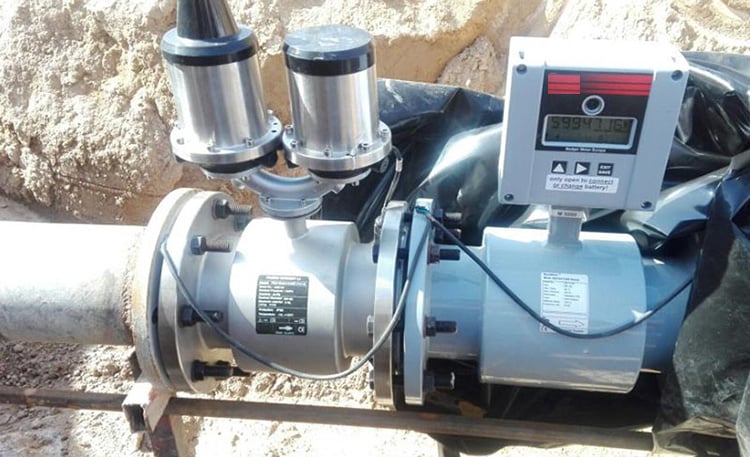
3. Battery-Powered Electromagnetic Flow Meters: Designed for applications where power availability is a concern, such as remote water distribution and irrigation systems. These mag meters offer portability and ease of installation but may have limitations in data logging and continuous operation.
4. Sanitary Electromagnetic Flow Meters: These meters are designed to meet the stringent hygiene requirements of the food, beverage, and pharmaceutical industries. They feature smooth surfaces, quick-release fittings, and materials that can withstand frequent cleaning, ensuring compliance with industry standards like 3A or EHEDG.
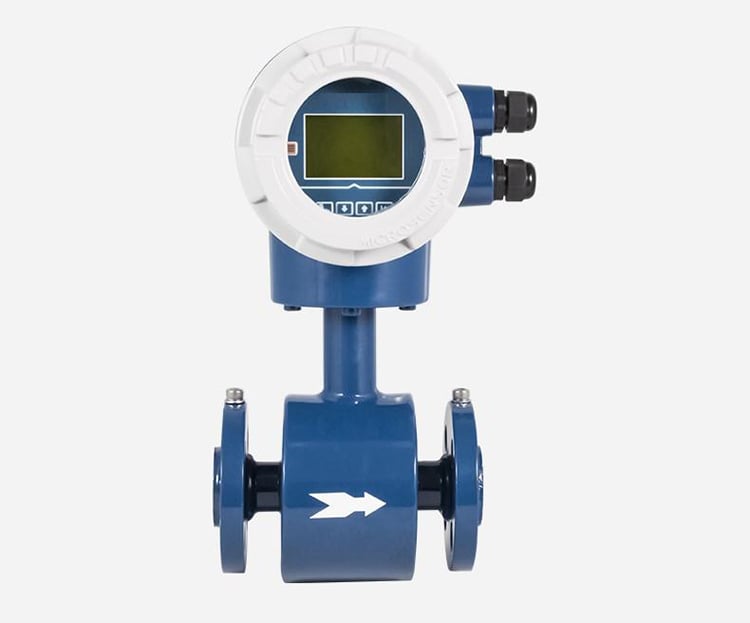
Applications of Electromagnetic Flow Meters
Electromagnetic flow meters are widely used in industries where measuring the flow of conductive liquids is crucial for process control, billing, or environmental monitoring. Some notable applications include:
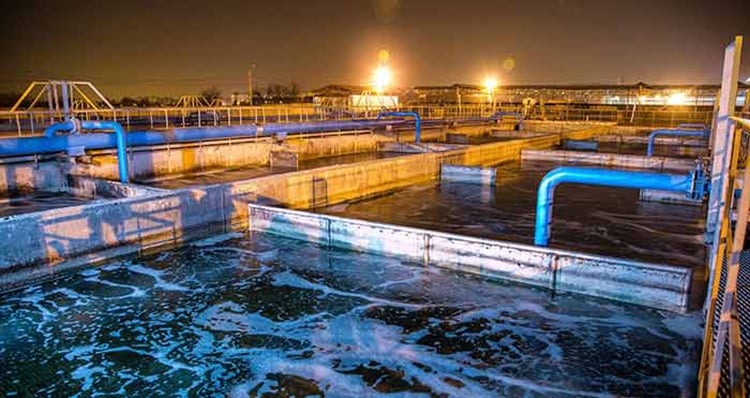
Water and Wastewater Treatment: In municipal and industrial water systems, mag meters are used for measuring raw water, treated water, sludge, and chemicals. Their resistance to abrasion from solids makes them ideal for wastewater applications.
– Agricultural and Irrigation Systems: Battery-operated mag meters are used in remote agricultural locations to measure water usage for efficient irrigation management.
Chemical and Petrochemical Industries: Mag meters measure aggressive chemicals, acids, bases, and corrosive liquids. Their non-intrusive measurement method ensures compatibility with corrosive and viscous substances.
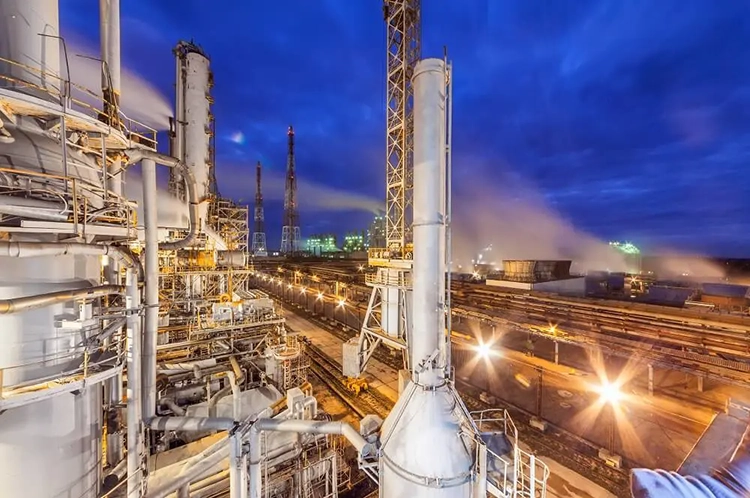
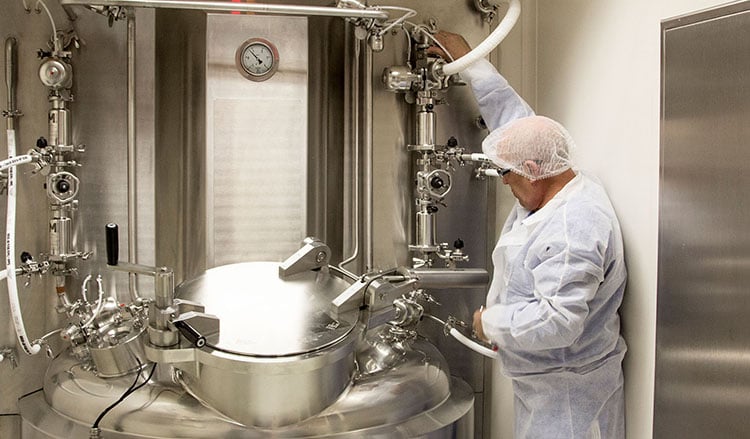
Pharmaceutical Industry: Accurate and sterile flow measurement is critical in pharmaceutical manufacturing, where mag meters provide reliability and precision for liquid handling and chemical addition processes.
– Mining and Pulp & Paper Industry: In mining, mag meters measure slurry flows with suspended particles, whereas in the pulp and paper industry, they monitor the flow of pulp, chemicals, and wastewater.
Food and Beverage Industry: Electromagnetic flow meters are used in the production of beverages, dairy products, and other consumables. The meters ensure precise dosing and quality control, adhering to hygiene standards with sanitary-grade models.
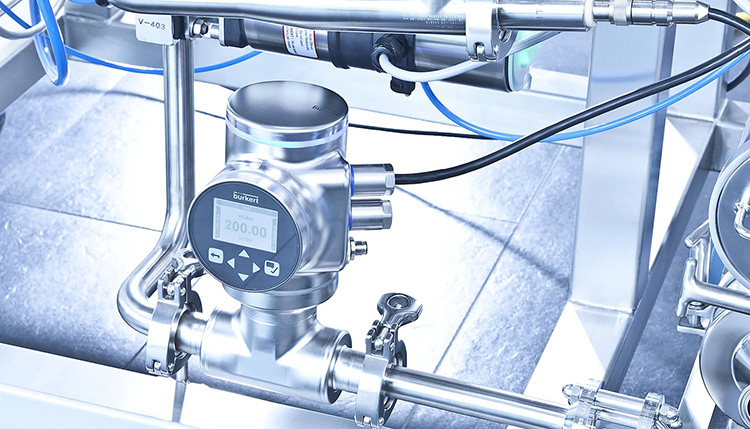
Electromagnetic flow meters are invaluable tools in modern industrial settings where the accurate measurement of conductive liquids is paramount. Their unique advantages, such as high accuracy, no moving parts, and broad application range, make them the preferred choice for many industries. However, their limitations, like the inability to measure non-conductive fluids and higher initial costs, must be considered when selecting the appropriate flow measurement technology. By understanding the working principles, advantages, disadvantages, applications, and types of electromagnetic flow meters, industries can make informed decisions that enhance process efficiency and reliability.
Leave a comment