Turbine flow meters are widely used in various industries for measuring the volumetric flow rate of liquids and gases. They are known for their accuracy, simplicity, and reliability. These flow meters are a type of volumetric flow measurement device that calculates the flow of a fluid passing through a pipe by detecting the velocity of the fluid. The velocity is determined by measuring the speed of a turbine or rotor that spins within the fluid flow.
Table of Contents
Related Posts: Differences between vortex and turbine flow meters
How Does Turbine Flow Meter Work?
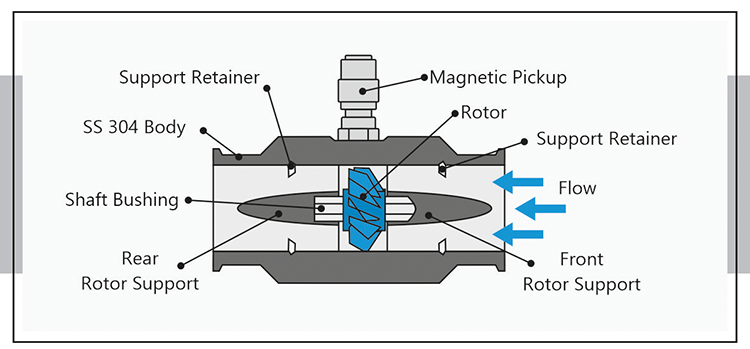
The operation of a turbine flow meter is based on the mechanical motion of a turbine wheel. As the fluid passes through the meter body, it strikes the turbine blades, causing the rotor to spin. The speed of rotation is directly proportional to the flow rate of the fluid. Here’s a more detailed breakdown of how they work:
- Structure and Components: A typical turbine flow meter consists of a rotor with multiple blades, a shaft, and bearings housed inside a flow tube. The flow tube is connected to the piping system, allowing fluid to pass through. Magnets or sensors are placed outside the flow tube to detect the rotational speed of the turbine.
- Rotation of the Turbine: As the fluid flows through the meter, it impacts the turbine blades. The kinetic energy from the fluid flow causes the rotor to spin at a rate proportional to the velocity of the fluid. The number of revolutions of the rotor is directly related to the volume of fluid passing through the meter.
- Signal Detection and Conversion: Sensors, usually magnetic or optical, detect the rotational speed of the turbine. The sensors generate electrical pulses for each revolution of the rotor. These pulses are transmitted to a flow transmitter, which processes the signal and converts it into a readable flow rate, typically displayed in units such as liters per minute (LPM) or gallons per minute (GPM).
Accuracy and Installation Considerations
Accuracy of turbine flow meters is influenced by several factors, including the quality of the meter, fluid properties, flow profile, and installation. Typically, turbine flow meters provide an accuracy of ±0.5% to ±1.5% of the reading, making them suitable for applications where precise measurements are essential.
Key Factors Affecting Accuracy:
- Fluid Properties: The viscosity, density, and temperature of the fluid can affect the turbine’s performance. Turbine flow meters work best with low-viscosity fluids where the flow is steady and free from pulsations.
- Flow Profile: A stable flow profile is essential for maintaining accuracy. Turbulent or swirling flows can cause uneven rotation of the turbine, leading to inaccurate readings. To ensure a steady flow, sufficient straight pipe runs (typically 10 times the pipe diameter upstream and 5 times downstream) are recommended before and after the flow meter.
- Installation Position: Turbine flow meters should be installed horizontally for optimal performance. The straight pipe requirements are usually 10 to 15 times upstream and downstream.
- Calibration and Maintenance: Regular calibration and maintenance, including cleaning and checking for wear and tear, are crucial for maintaining accuracy. Bearings, in particular, are prone to wear and must be monitored regularly.
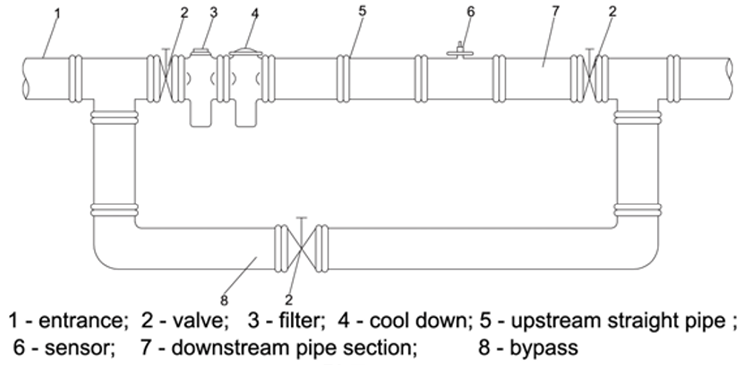
Advantages and disadvantages of Turbine Flow Meters
Advantages | Disadvantages |
1. High accuracy at an economic price 2. Fast Response Time 3. Easy to install and maintain 4. Low pressure-drop 5. Can measure low flow rates | 1. Clean and low viscosity fluids only 2. Pipes must be consistently full for accuracy 3. Straight piping requirements to reduce flow turbulence 4. Ferrous and magnetic particles should be filtered out upstream for some models |
Available Fluids and Applications
Turbine flow meters are versatile and can measure various fluids, including:
- Liquids: Water, light oils, fuels, alcohols, solvents, and other low-viscosity liquids.
- Gases: Natural gas, compressed air, nitrogen, and other clean gases.
Key Applications of Turbine Flow Meters:
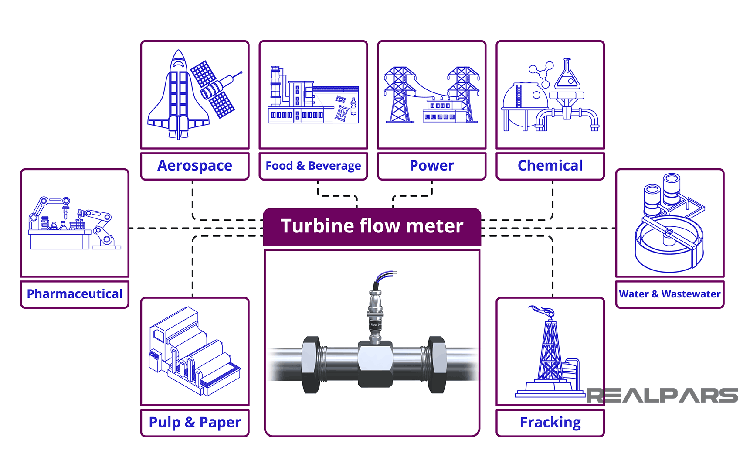
- Oil and Gas Industry: Used for measuring the flow of fuels, oils, and natural gas. Their high accuracy and reliability make them ideal for custody transfer applications.
- Water and Wastewater Management: Widely used in water treatment plants for measuring clean water flow, chemical dosing, and monitoring effluents.
- Chemical and Petrochemical Industries: Employed for measuring the flow of various chemicals, solvents, and other low-viscosity fluids where precise dosing and mixing are required.
- Pharmaceutical Industry: Utilized for measuring the flow of pure water, alcohols, and other fluids critical for drug formulation and production.
- Food and Beverage Industry: Used to measure liquid ingredients like water, oils, syrups, and flavorings in production lines.
- HVAC Systems: Employed to measure the flow of water and other heat transfer fluids in heating, ventilation, and air conditioning systems.
- Aerospace and Automotive Industries: Used for testing fuel and hydraulic systems, ensuring accurate measurements and control in critical applications.
Turbine flow meters are a reliable and cost-effective solution for measuring the flow of low-viscosity fluids and gases in various industries. Their high accuracy, simplicity, and versatility make them suitable for many applications, from oil and gas to food and beverage production. However, understanding their limitations, such as sensitivity to viscosity changes and the need for regular maintenance, is crucial when selecting the right flow measurement technology. By considering the specific requirements of your application, turbine flow meters can offer precise and efficient flow measurement, ensuring optimal process control and efficiency.
Leave a comment