A fuel flow meter is an instrument designed to measure the volume or mass of fuel passing through a system. These devices are widely used to monitor the consumption of fuels like diesel, gasoline, kerosene, and biodiesel in engines, generators, and fuel distribution systems.
Fuel flow meters provide critical data for:
- Monitoring and optimizing fuel usage.
- Detecting leaks or inefficiencies.
- Maintaining compliance with environmental and operational standards.
Table of Contents
Common Fuel Types
The choice of a fuel flow meter often depends on the type of fuel being measured. Common fuels include:
- Diesel: Widely used in industrial machinery, trucks, and generators due to its efficiency and energy density.
- Gasoline: Commonly used in vehicles and small machinery, requiring meters with high precision for small-volume measurements.
- Biodiesel: An eco-friendly alternative derived from vegetable oils or animal fats. Its viscosity can vary, affecting meter selection.
- Kerosene: Used in aviation and heating applications. Meters for kerosene must handle low-viscosity fluids.
- Heavy Fuel Oil (HFO): Utilized in large marine engines and power plants. It requires meters capable of handling high-viscosity and abrasive properties.
- Liquefied Petroleum Gas (LPG): Stored as a liquid and used in heating, cooking, and automotive applications. Meters must handle both liquid and vapor phases.
Top 5 Recommended Oil Flow Meters
Recommended Types of Fuel Flow Meters
There are several types of fuel flow meters, each suited for different applications:
1. Positive Displacement Flow Meters
Working Principle:
Positive displacement meters capture a known volume of fuel in chambers and count the number of times these chambers fill and empty, like oval gear flow meters.
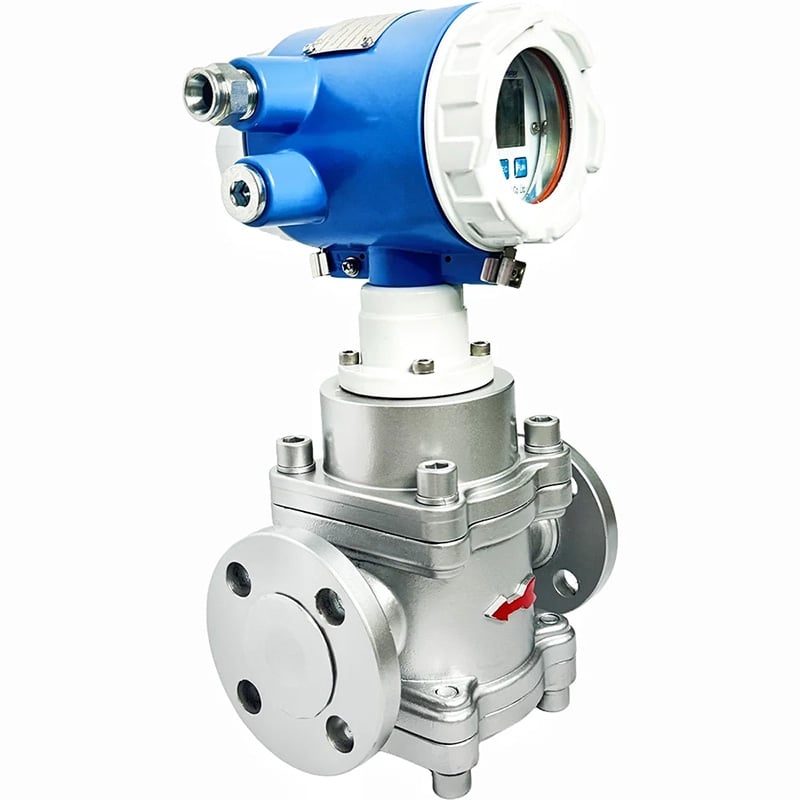
Features:
- High accuracy up to ±0.1 %, high process pressure up to 110 bar (1595 psi)
- Stable in running with low voice
- Good anti-interference performance and long service life
- Strong applicability to viscosity changes
Best for: Viscous fuels like diesel and heavy fuel oil.
Advantages:
- Highly accurate, even at low flow rates.
- Independent of temperature, pressure, or viscosity changes.
Limitations:
- Not ideal for abrasive or dirty fuels.
2. Turbine Flow Meter
Working Principle:
A turbine placed in the flow path spins as fuel passes through it. The rotational speed is proportional to the flow rate.
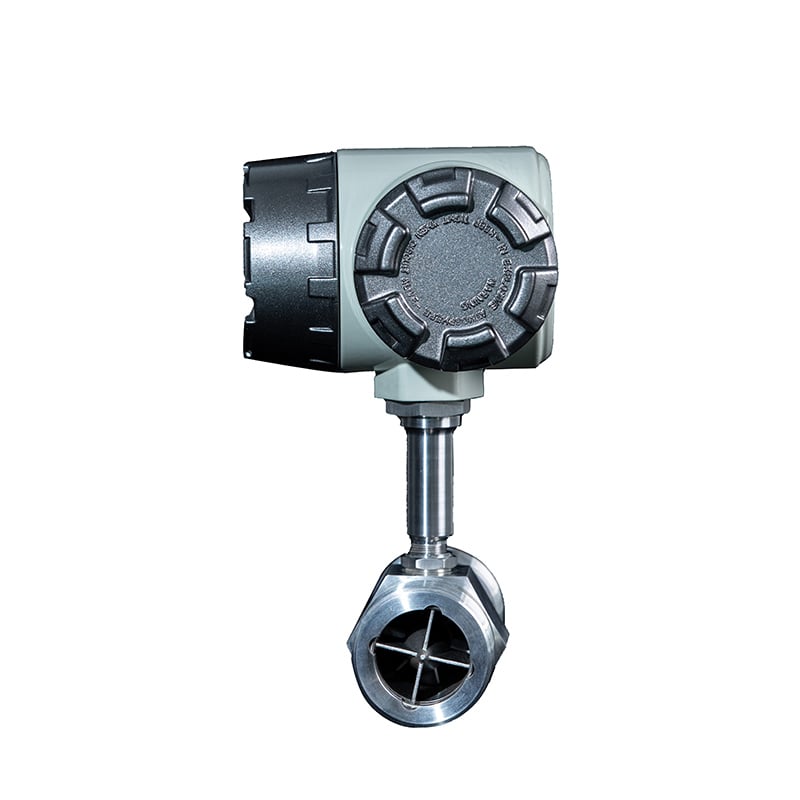
Features:
- Measurement of low viscosity fluids with high accuracy ±0.2 %
- Also available in customer specific construction.
- Colors and appearance can be customized as requested
Best for: Clean fuels like gasoline and kerosene.
Advantages:
- Cost-effective and easy to install.
- High accuracy for clean and low-viscosity fuels.
Limitations:
- Sensitive to fluid viscosity and cleanliness.
3. Coriolis Mass Flow Meter
Working Principle:
These meters measure the deflection caused by fuel flow in vibrating tubes. The deflection is proportional to the mass flow rate.
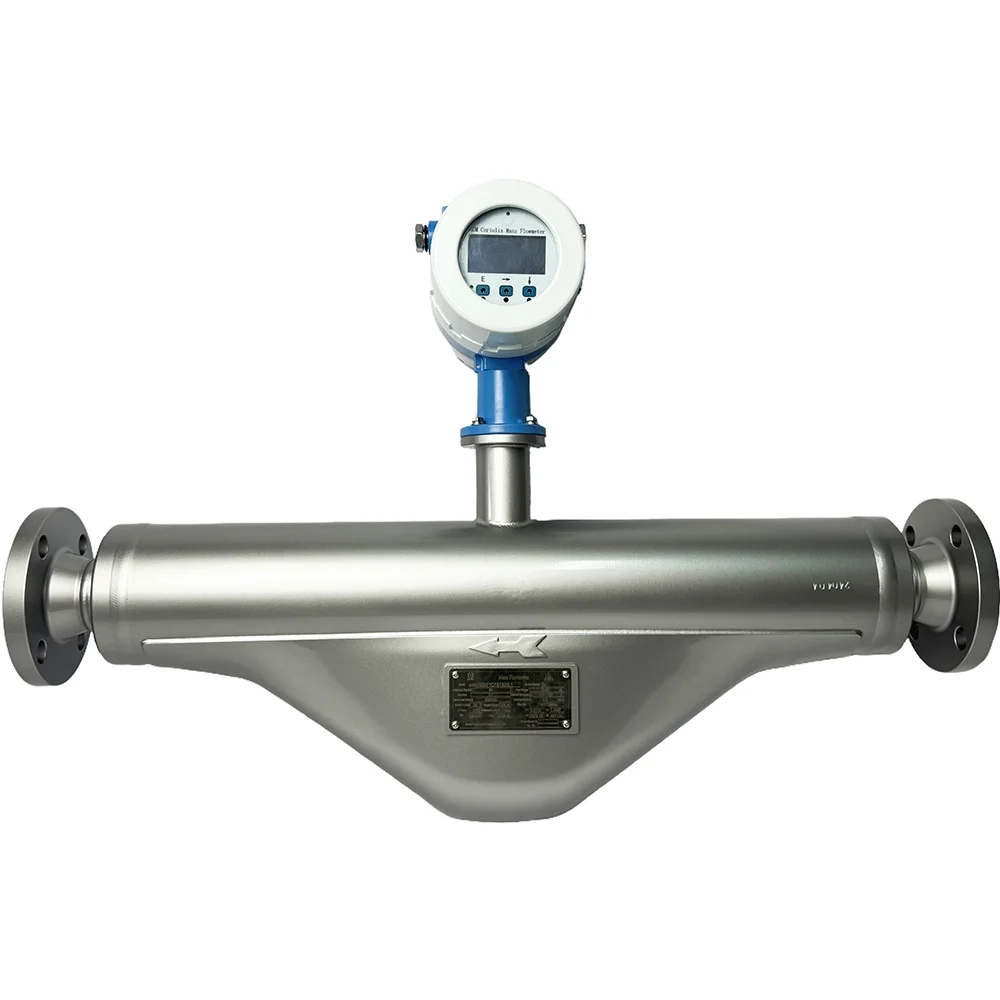
Features:
- High accuracy mass, density and volume flow measurement
- Certified for hygienic use
- Supporting CIP or SIP cleaning procedures
Best for: Measuring mass flow and density of any fuel.
Advantages:
- Direct measurement of mass flow and density.
- Handles a wide range of fuel types and viscosities.
- No moving parts, reducing maintenance needs.
Limitations:
- High initial cost.
- Sensitive to external vibrations.
4. Electromagnetic Flow Meter
Working Principle:
Based on Faraday’s Law of Electromagnetic Induction, these meters measure the voltage induced as conductive fuel flows through a magnetic field.
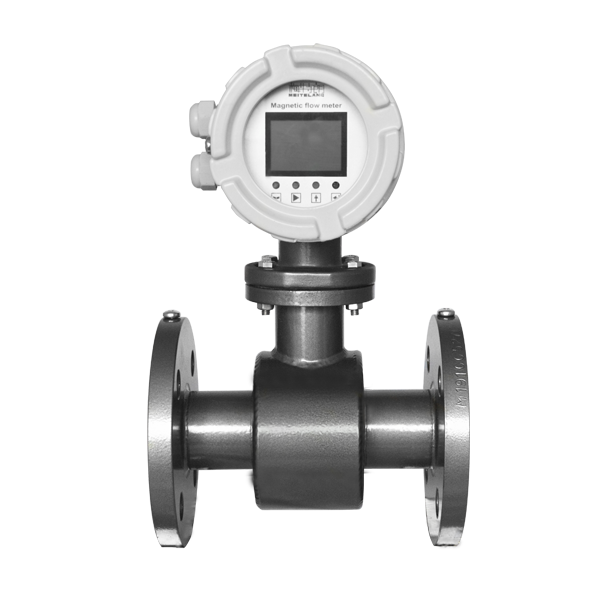
Features:
- The measuring principle is virtually independent of pressure, density, temperature and viscosity
- Wide range of liners and electrode materials
- No moving parts, no wear, no pressure loss
- Reliable measurement at constant accuracy
Best for: Conductive fuels like biodiesel blends.
Advantages:
- No moving parts, ensuring durability.
- Accurate measurement for conductive fuels.
Limitations:
- Cannot measure non-conductive fuels like gasoline.
- Requires an electrical power source.
5. Ultrasonic Flow Meter
Working Principle:
Ultrasonic flow meters use sound waves to measure flow. Transit-time meters calculate flow by measuring the time difference of sound waves traveling with and against the flow. Doppler meters use the frequency shift of sound waves reflecting off particles or bubbles.
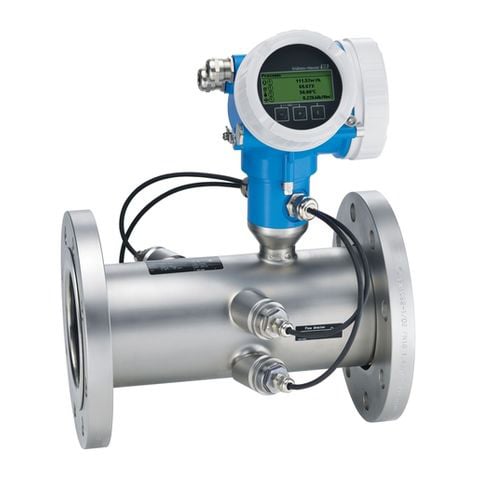
Best for: Monitoring fuel in large pipelines.
Advantages:
- Non-intrusive and no pressure loss.
- Suitable for large pipelines.
Limitations:
- Performance may degrade with dirty fuels or bubbles.
- High cost.
How to Choose a Fuel Flow Meter
Selecting the right fuel flow meter involves considering several factors:
1. Type of Fuel:
- Determine the viscosity, conductivity, and cleanliness of the fuel. For instance, Coriolis meters are ideal for viscous and multi-phase fuels, while turbine meters excel with clean, low-viscosity fuels.
2. Accuracy Requirements:
- For critical applications like custody transfer, opt for highly accurate meters like Coriolis or positive displacement meters.
3. Flow Range and Pressure:
- Ensure the meter can handle the expected flow range and pressure. Turbine meters work well for high flow rates, while PD meters are better for low flows.
4. Maintenance Needs:
- Consider meters with minimal maintenance requirements, such as electromagnetic or ultrasonic flow meters.
5. Installation Environment:
- For compact or restricted spaces, select meters with flexible installation options, such as clamp-on ultrasonic meters.
6. Budget:
- Balance cost and performance. Electromagnetic and turbine meters are cost-effective, while Coriolis meters offer premium accuracy at a higher price.
Fuel flow meters are indispensable tools for measuring fuel consumption, optimizing operations, and reducing costs. From positive displacement meters for viscous fuels to ultrasonic meters for large-scale monitoring, the choice of meter depends on the specific requirements of your application. By understanding the fuel type, flow conditions, and operational needs, you can select a fuel flow meter that delivers precision, efficiency, and reliability.
Leave a comment