In the world of fluid dynamics and industrial process control, accurate flow measurement is critical for optimizing efficiency, ensuring safety, and reducing operational costs. Among the many tools available, the Pitot tube flow meter stands out for its simplicity, reliability, and cost-effectiveness. Originally invented in the 18th century by French engineer Henri Pitot, this device remains widely used in aviation, HVAC systems, and industrial applications.
Table of Contents
What is a Pitot Tube Flow Meter?
A Pitot tube flow meter is a device that measures fluid flow velocity by comparing static pressure and dynamic pressure in a fluid stream. It consists of two primary components:
- Static Pressure Port: Measures the pressure of the fluid when it is at rest.
- Dynamic Pressure Port (Pitot Tube): Captures the pressure of the fluid in motion.
The difference between these two pressures, known as stagnation pressure or total pressure, is used to calculate flow velocity. Pitot tubes are particularly effective for measuring airflow in aviation and gas/steam flow in industrial systems.
Principles of Pitot Tube Flow Meters
Bernoulli’s Equation: The Foundation
The Pitot tube operates on Bernoulli’s principle, which states that in a steady, incompressible flow, the total energy (sum of static pressure, dynamic pressure, and gravitational potential energy) remains constant. For horizontal flow, the equation simplifies to:

Where:
- Ptotal: Total pressure (measured by the Pitot tube).
- Pstatic: Static pressure.
- ρ: Fluid density.
- v: Flow velocity.
By rearranging the equation, velocity vv can be calculated as:

How It Works
- The Pitot tube is inserted into the fluid stream, aligning its opening with the flow direction.
- The dynamic pressure port captures the total pressure (Ptotal), while the static port measures ambient pressure (Pstatic).
- A differential pressure sensor calculates the difference (ΔP).
- Flow velocity is derived using Bernoulli’s equation.
Metlan Instruments Pitot Tube Gas Flow Meter
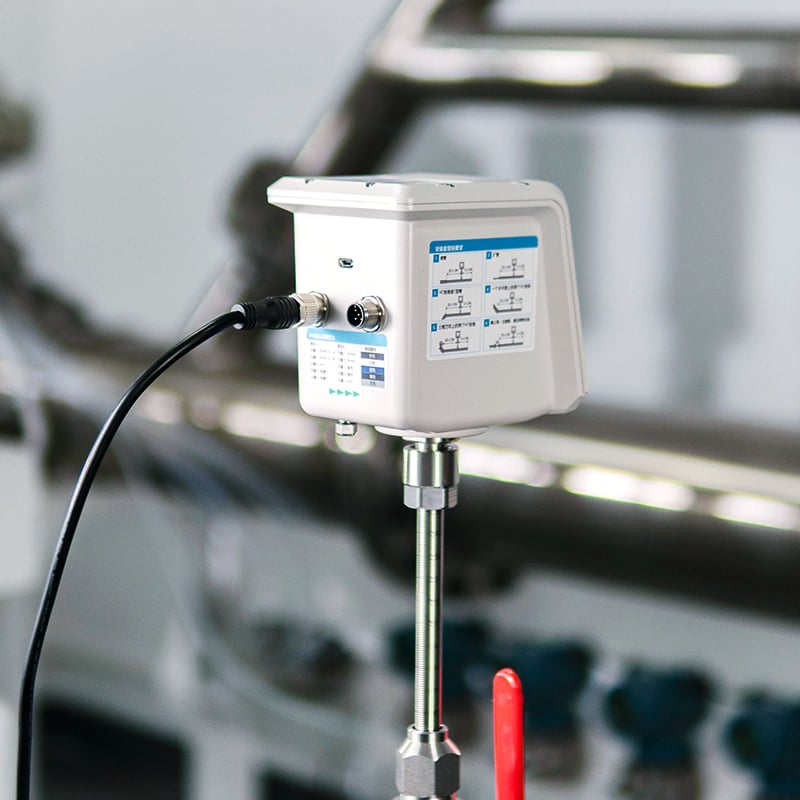
Features:
- It is not affected by pipeline vibration
- Applicable to the measurement of dirty and wet air
- Online auto-calibration reduces data drift
- High sensitivity, the lower limit is down to 5 Nm/s
- 1:60 wide turndown ratio
- Bidirectional flow measurement
- Integrates pressure and temperature sensors to monitor online gas pressure and temperature
- No moving parts, low pressure drop
Suitable Mediums for Pitot Tube Flow Meters
Pitot tubes excel in specific fluid conditions:
Ideal Fluids
- Clean Gases:
- Air, nitrogen, oxygen, and steam.
- Minimal particulates prevent clogging of the pressure ports.
- Low-Viscosity Liquids:
- Water, light oils, and chemicals.
- Steady, Turbulent Flow:
- Laminar flow (smooth, orderly motion) is less suitable due to inconsistent pressure readings.
Unsuitable Fluids
- High-Viscosity Fluids: Honey, heavy oils (cause pressure lag).
- Dirty or Slurry Fluids: Particles can block the tube.
- Multiphase Flows: Mixtures of gas and liquid (e.g., wet steam).
Applications of Pitot Tube Flow Meters
1. Aviation
- Airspeed Measurement: Pitot tubes on aircraft wings measure airspeed by comparing atmospheric and dynamic pressures.
- Critical Safety Role: Malfunctions (e.g., blockages from ice) can lead to erroneous readings, emphasizing the need for heating systems in modern planes.
2. HVAC Systems
- Duct Airflow Monitoring: Ensures balanced air distribution in commercial buildings.
- Energy Efficiency: Detects leaks or inefficiencies in ventilation systems.
3. Industrial Process Control
- Steam Flow Measurement: Monitors boiler output in power plants.
- Gas Pipeline Monitoring: Tracks natural gas flow in transmission lines.
4. Environmental Engineering
- Wind Tunnel Testing: Measures airflow velocity in aerodynamic research.
- Pollution Monitoring: Assesses stack gas emissions in factories.
5. Water Management
- Open-Channel Flow: Modified Pitot tubes measure river or canal flow rates.
How to Choose a Pitot Tube Flow Meter
1. Fluid Compatibility
- Ensure the tube material (e.g., stainless steel, brass) resists corrosion from the fluid.
2. Flow Profile
- Use averaging Pitot tubes (e.g., Annubar®) for non-uniform flow in large pipes.
3. Pressure Range
- Select a sensor capable of handling the system’s maximum pressure.
4. Temperature Conditions
- High-temperature applications may require cooling assemblies.
5. Output Requirements
- Choose analog (4–20 mA) or digital (Modbus, HART) outputs for integration with control systems.
Despite its 18th-century origins, the Pitot tube flow meter remains a cornerstone of fluid velocity measurement. Its simplicity, durability, and low cost make it indispensable in aviation, HVAC, and industrial settings. While newer technologies offer higher precision for complex flows, the Pitot tube’s reliability in clean, steady environments ensures its continued relevance.
By understanding its principles, limitations, and ideal applications, engineers can leverage this timeless tool to enhance system performance and sustainability.