Compressed air is often called the “fourth utility” in industrial settings, alongside electricity, water, and gas. It powers machinery, controls processes, and ensures operational efficiency across industries like manufacturing, automotive, and food production. However, compressed air systems are energy-intensive, accounting for up to 30% of a plant’s electricity costs. To optimize performance and reduce waste, businesses rely on compressed air flow meters—devices that measure airflow to ensure systems run lean, safe, and cost-effectively.
Table of Contents
Characteristics of Compressed Air and Industrial Applications
Compressed air is ambient air pressurized to store energy. Its unique traits include:
- Cleanliness: Free of contaminants when filtered, ideal for sensitive processes.
- Dryness: Moisture is removed to prevent corrosion and equipment damage.
- Versatility: Adjustable pressure (typically 7–15 bar) for diverse applications.
- Safety: Non-flammable and non-toxic, suitable for hazardous environments.
Why Are Compressed Air Flow Meters Important?
- Energy Savings:
- Compressed air systems waste 20–30% of energy through leaks and inefficiencies. Flow meters pinpoint losses, helping reduce electricity bills.
- Process Reliability:
- Ensure consistent air supply for critical operations (e.g., CNC machines).
- Leak Detection:
- A single 3mm leak can cost $1,000+ annually in wasted energy. Flow meters trigger alerts for timely repairs.
- Sustainability:
- Reducing air waste lowers carbon footprints, aligning with ESG goals.
- Cost Allocation:
- Monitor department-level usage for accurate billing in multi-tenant facilities.
Recommended Flow Meter Types for Compressed Air
Choosing the right meter depends on accuracy needs, pressure ranges, and budget. Below are the top options:
1. Thermal Mass Flow Meters
How They Work: Measure flow by detecting heat dissipation from a heated sensor.
Advantages:
- Direct mass flow measurement (no pressure/temperature compensation).
- High accuracy (±1–1.5% of reading).
- Low maintenance with no moving parts.
- Available for low flow rates
Disadvantages:
- Requires clean, dry air (moisture or oil affects accuracy).
Best For: Energy audits, leak detection, and general monitoring.
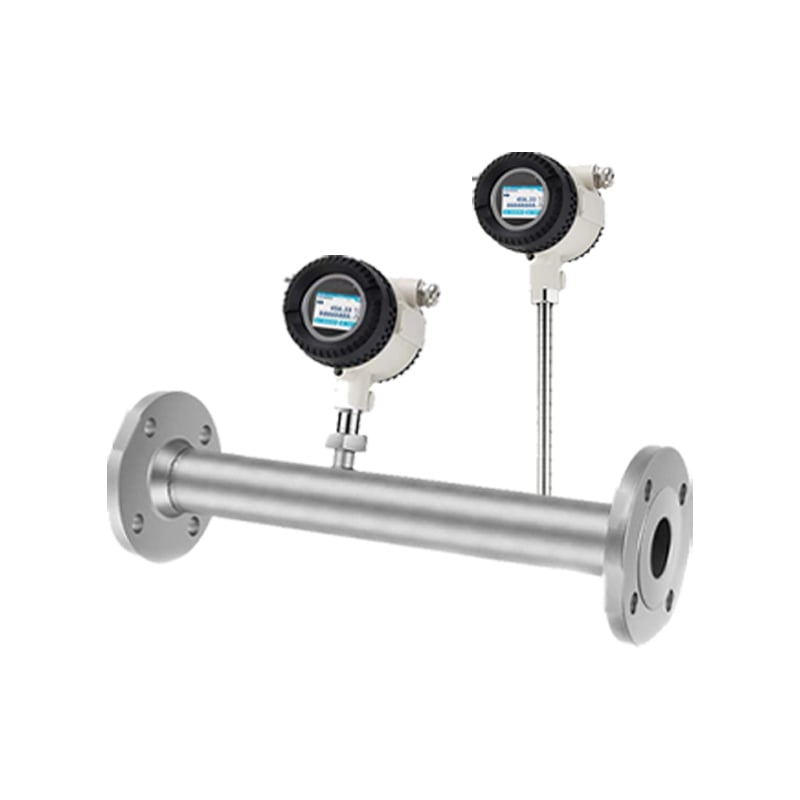
Features:
- Explosion-proof class: Ex db IIC T6 Gb / Ex tb IIIC T80°CDb.
- Ultra-wide 1:2500 turndown ratio.
- The measuring range is from 0.1 Nm/s to 250 Nm/s.
- Full-digital signal processing, higher accuracy, long-term stability.
- Suitable for pipes with diameters from DN15 to DN1000.
- Check More: Inline Explosion-proof Thermal Mass Flow Meter | Insertion Explosion-proof Thermal Mass Flow Meter
2. Ultrasonic Flow Meters
How They Work: Use ultrasonic waves to measure flow velocity (transit-time method).
Advantages:
- Non-invasive clamp-on models for easy retrofitting.
- No pressure drop or pipe modifications.
- Bidirectional flow measurement.
Disadvantages:
- Accuracy affected by pipe material and air purity.
- Higher cost for high-precision models.
Best For: Large pipelines in HVAC or industrial plants.
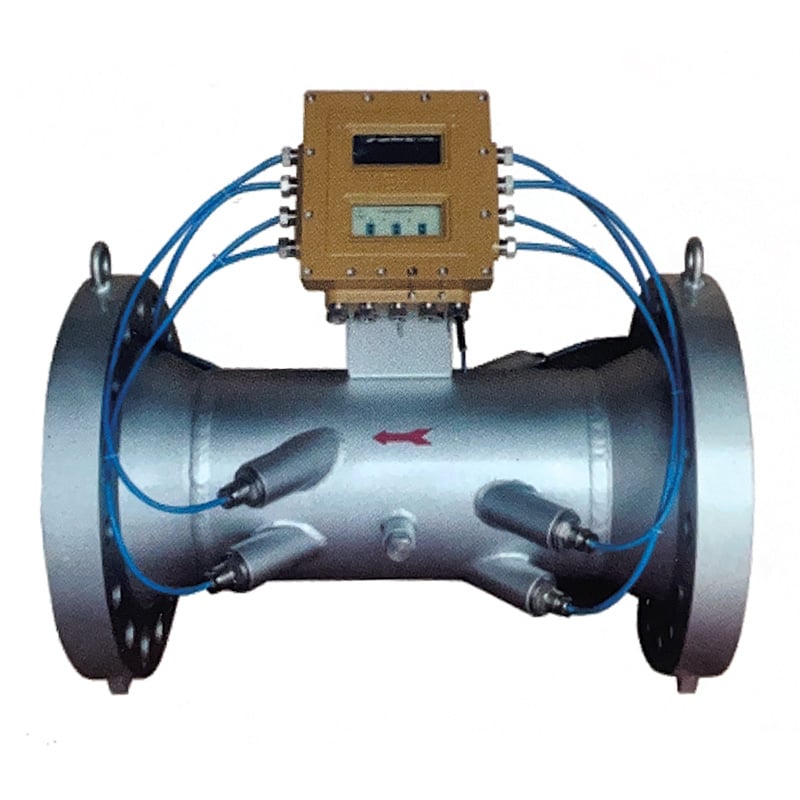
Features:
- High accuracy for gas up to ±0.5%.
- 100:1 Wide turndown ratio.
- No moving parts, no presure loss, no line obstructions.
- No lubrication or periodic maintenance.
- Measurement is not affected by gas properties.
- Bi-directional capability.
- Explosion-proof class: Ex db IIC T6 Gb.
- Check More: Ultrasonic High Accuracy Gas Flow Meter
3. Vortex Shedding Flow Meters
How They Work: Detect vortices created by a bluff body in the airflow.
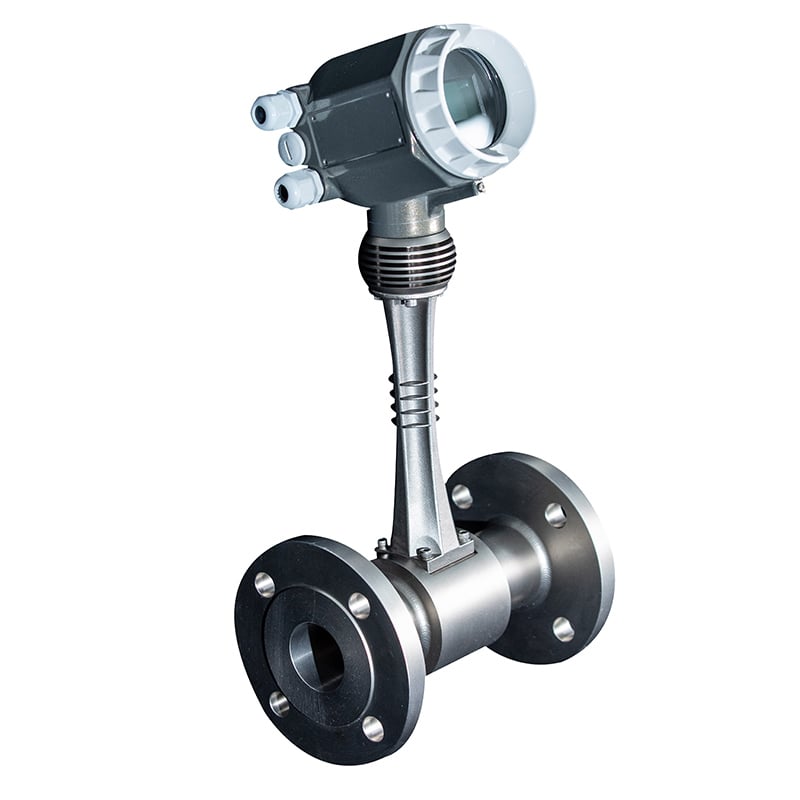
Advantages:
- Robust design for harsh environments.
- Minimal maintenance.
Disadvantages:
- Requires straight pipe runs for accuracy.
- Limited to turbulent flow regimes.
Best For: High-flow industrial processes.
4. Variable Area Flow Meters (Rotameters)
How They Work:
A float rises in a tapered tube proportionally to the flow rate.

Advantages:
- Low cost and visual flow indication.
- Easy installation.
Disadvantages:
- Low accuracy (Standard: ±2.5%).
- Requires vertical installation.
Best For: Small-scale applications or rough estimates.
Comparison Table: Compressed Air Flow Meters
Type | Accuracy | Cost | Maintenance | Best Use Case |
---|---|---|---|---|
Thermal Mass | ±1–2% | Medium | Low | Leak detection, audits |
Ultrasonic | ±0.5–1.5% | High | Low | Large pipelines |
Vortex Shedding | ±1–2.5% | Medium | Medium | High-flow industrial |
Variable Area | ±2.5% | Low | Low | Small-scale monitoring |
How to Choose a Compressed Air Flow Meter
Follow these steps to select the ideal meter:
1. Define Your Application Needs
- Flow Range: Measure typical and peak flow rates (e.g., 0–500 SCFM).
- Pressure: Ensure the meter matches system pressure (e.g., 100 PSI vs. 150 PSI).
- Accuracy: ±1% for energy audits vs. ±5% for general monitoring.
2. Assess Air Quality
- Oil-Free vs. Lubricated Systems: Thermal meters may fail in oily air.
- Moisture Content: Use desiccant dryers and avoid moisture-sensitive meters.
3. Installation Environment
- Pipe Size and Material: Clamp-on ultrasonic meters work on metal or plastic pipes.
- Hazardous Areas: Look for ATEX/IECEx certifications if explosive gases are present.
4. Total Cost of Ownership (TCO)
- Factor in maintenance, calibration, and energy savings over time.
5. Compliance and Reporting
- Choose meters with data logging or integration with SCADA/MES systems.
Common Mistakes to Avoid
- Ignoring Air Quality: Moisture or oil can damage sensitive meters.
- Overlooking Calibration: Even high-end meters drift over time.
- Choosing Based on Price Alone: Low-cost meters may lack needed accuracy.
Compressed air flow meters are indispensable for industries aiming to balance productivity, cost, and sustainability. Whether you’re optimizing a factory’s pneumatic network or ensuring sterile conditions in a food plant, selecting the right meter—thermal, ultrasonic, vortex, or another type—can slash energy bills, prevent downtime, and extend equipment life.